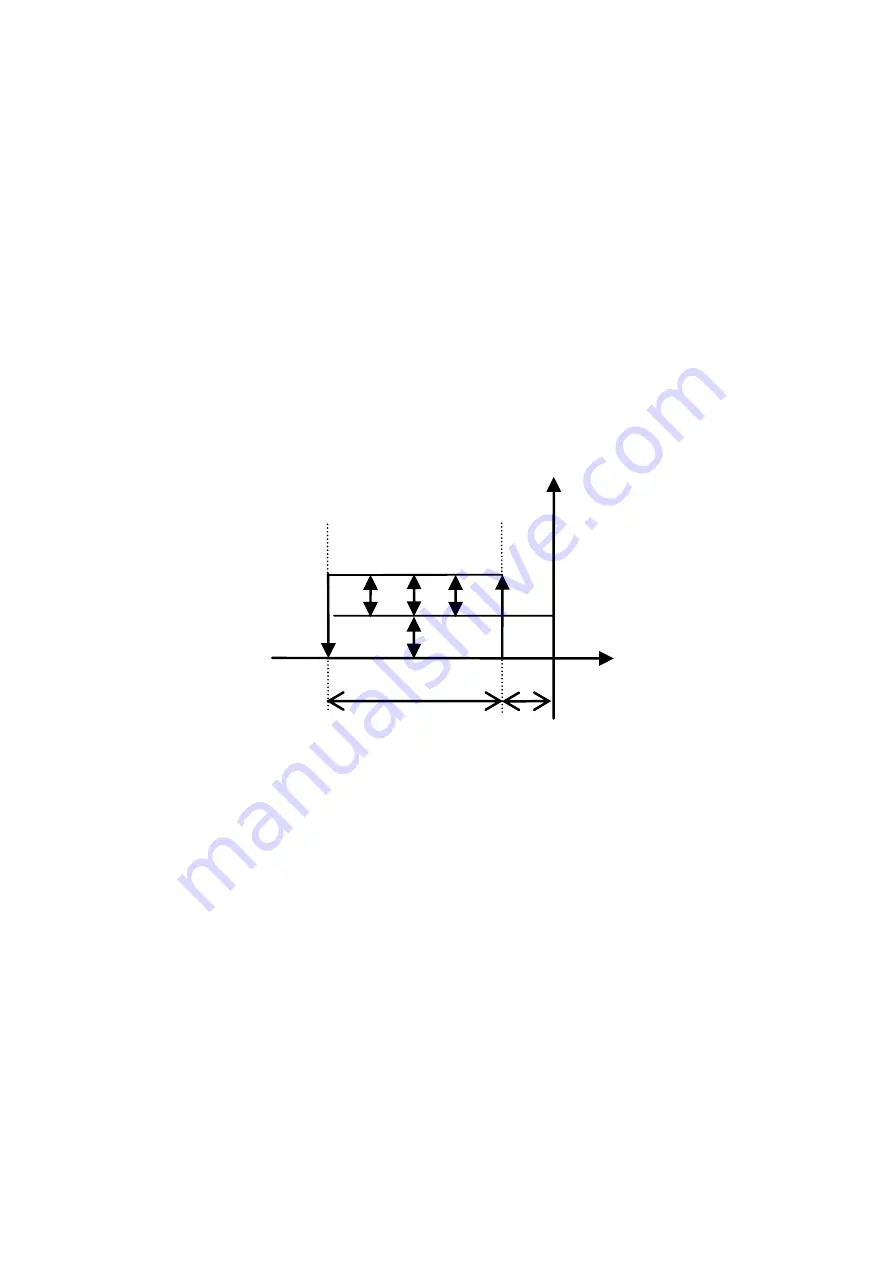
We reserve the right to make changes without prior notice
39
The setup values given to the parameters above help to control the priority of the cooling devices according to
the combinations below:
the free cooling damper is opened first; the compressors are only started after the damper has
achieved its max. opening, if the ambient air temperature setpoint is not met;
compressors are started first; the free cooling damper is only opened if the ambient air temperature
setpoint is not met;
the free cooling damper and the compressors are started in parallel.
6.4.2 Air heating
Units featuring a heat pump warm the air using compressors. Alternatively, all units can be supplied with
heating devices such as electric coils or hot water coils with a modulating valve.
6.4.2.1 Compressor heating
The compressors used for the heating cycle are activated proportionally as the ambient temperature (Ta) drops
with respect to the winter setpoint (SPh) and within the heating differential (DTh), which is divided in equal
parts depending on the number of compressors fitted in the unit. A “dead zone” (ZN) may be envisaged within
which the controller does not activate the compressors. The software manages the dead zone in such way
that half of the dead zone value (1/2 ZN) is between the winter setpoint and the beginning of the cooling
differential.
C1
C2
DTh
1/2
ZN
C4 C3
C2
C1
SPh
Ta
The controller automatically starts the compressors when the unit is in operation and there are no active alarms
affecting either the entire unit or the compressors that are to be started. Compressors are started in sequence
so as to minimise inrush currents.
After a settable delay to unit start-up, the air flow switch input must get closed so that the controller can enable
the compressors. If the input of the air flow switch opens during unit operation, the air flow alarm triggers after
a settable delay, which causes the unit and the compressors to stop.
The compressor controller described above is purely proportional, so it has an intrinsic defect: the error, i.e.
the distance between the setpoint and the ambient temperature, tends to zero, but never reaches it. If you wish
to have a more accurate temperature control, the PI (proportional and integral) controller can be enabled so
as to successfully achieve the setpoint to the detriment of a possible over elongation, i.e. the temperature may
rise above the stored setpoint for a span of time. This option is designed for the controller to override activation
of the next step (compressor) after the integral time has elapsed in cases when the activation of some
compressors leads to a deadlock and the ambient temperature setpoint is not achieved.