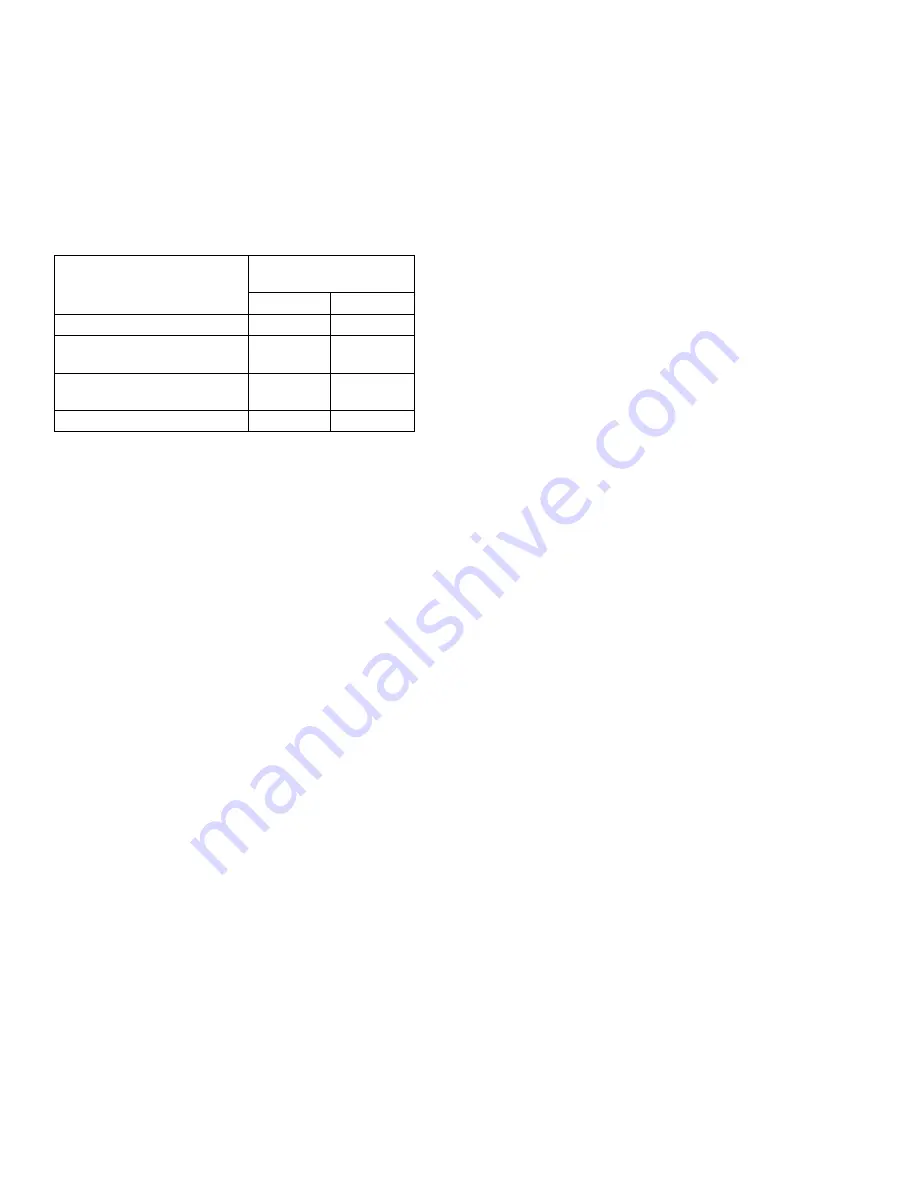
62-11389
4
−
2
The engine start sequence consists of periods of time
with the intake air heater relay (IAHR) or glow heater
relay (GPR) and starter solenoid relay (SSR) energized
and de-energized for up to three start attempts. See
Figure 4
−
1.
Energizing the heater relay closes its contacts to energize
the intake air heater (IAH), the heating time will vary in
duration based on engine coolant temperature (refer to
Table 4
−
1).
Table 4
−
1 Intake Air Heat Time
Engine Coolant
Temperature
Heat Time
in Seconds
Preheat
Post Heat
Less than 33
F (1.0
C)
30
180
33
F to 51
F (1.0
C to
11
C)
20
120
51
F to 78
F (11
C to
26
C)
10
60
Greater than 78
F (26
C)
0
0
If the A129 - “CHECK ENGINE COOLANT SENSOR”
alarm is active, the microprocessor assumes a
temperature of less than 32
F (0
C) for the heat timing.
During the last five seconds of Preheat
OR
for 5
seconds before a start attempt, if no Preheat is required,
the buzzer (B) is energized; then the starter solenoid
relay (SSR) will be energized for a maximum of ten
seconds while the engine condition is checked each two
seconds during the cranking period. The engine is
considered to be running, and the start sequence will be
stopped, when engine speed is greater than 1000 rpm.
During the second and third attempts, the
microprocessor will monitor additional inputs.
When engine speed reading is less that 1000 rpm,
ambient temperature is above 32
°
F (0
°
C) and the
ENOPS is closed the A130 - “CHECK ENGINE RPM
SENSOR” alarm will be activated and the engine will be
considered running.
When engine speed reading is less that 1000 rpm,
ambient temperature is below 32
°
F (0
°
C), the ENOPS is
closed and DC current is more than 2 amps the A130 -
“CHECK ENGINE RPM SENSOR” alarm will be
activated and the engine will be considered running.
Once the engine is considered running, the
microprocessor will keep the intake air heater energized
for an additional 0 to 180 seconds of Post Heat,
depending on engine coolant temperature (refer to
Table 4
−
1).
During the start sequence the microprocessor monitors
engine speed while cranking. If engine speed drops
below 50 rpm for three seconds the starter solenoid
contactor will be de-energized and the A35 - “CHECK
STARTER CIRCUIT” alarm will be activated.
If the unit fails to start after three start attempts, the A31
- “FAILED TO START-AUTO” alarm will be activated.
If the unit is equipped with a fuel heater, the
microprocessor will monitor ambient temperature. If
ambient is below 77
°
F (25
°
C) power will be supplied to
the fuel heater relay (FHR). Energizing FHR closes its
normally open contacts to supply power through the fuel
heater temperature switch (FHTS) to the heater. Refer
to Section 2.8 for FHTS settings.
4.2.3 Transition To High Speed
After a successful start, the microprocessor may call for
the engine to transition to high speed. Three factors
control this transition.
•
First, transition may be delayed if a time value is
entered in either the START-STOP HIGH SPEED
DELAY or CONTINUOUS HIGH SPEED DELAY
Configuration. The delay may be set to OFF
or
from 0
to 255 minutes. The factory default setting for
Start-Stop Operation is 10 minutes while the factory
default setting for Continuous Operation is OFF. If the
entered value for the present mode of operation is
OFF, high speed operation is not allowed for two
minutes following start.
•
Second, the engine cannot transition if the SILENT
MODE functional parameter is set to YES. The value
may be set to YES or NO. The factory default setting
is NO. (Refer to Table 3-2).
•
Third, transition will be based on the need for temper-
ature control. Generally, the engine will operate in
high speed when the unit is in Pulldown or Pull-Up
Mode (full capacity required) and in low speed when
the unit is in most less than full capacity required op-
erating states.
4.3 TEMPERATURE CONTROL
4.3.1 Temperature Determination
The microprocessor monitors the temperature readings
from the supply and return temperature sensors to
determine the mode of operation required to maintain
compartment temperature in accordance with the set
point.
The sensor used for temperature control is dependent
on the selection made in the “TEMP CONTROL”
functional parameter.
If the selection is “RETURN AIR” the return
air sensor (RAT) will be used, for any set
point.
If the selection is “SUPPLY AIR” the
microprocessor will switch to the supply air
sensor (SAT) when operating with a
perishable set point (refer to Section 4.3.2
for more information on frozen and
perishable set points) and the return air
sensor will continue to be used for frozen
set points.
The modes of operation include Pulldown, Pull-Up,
Cooling, Heating and Null.