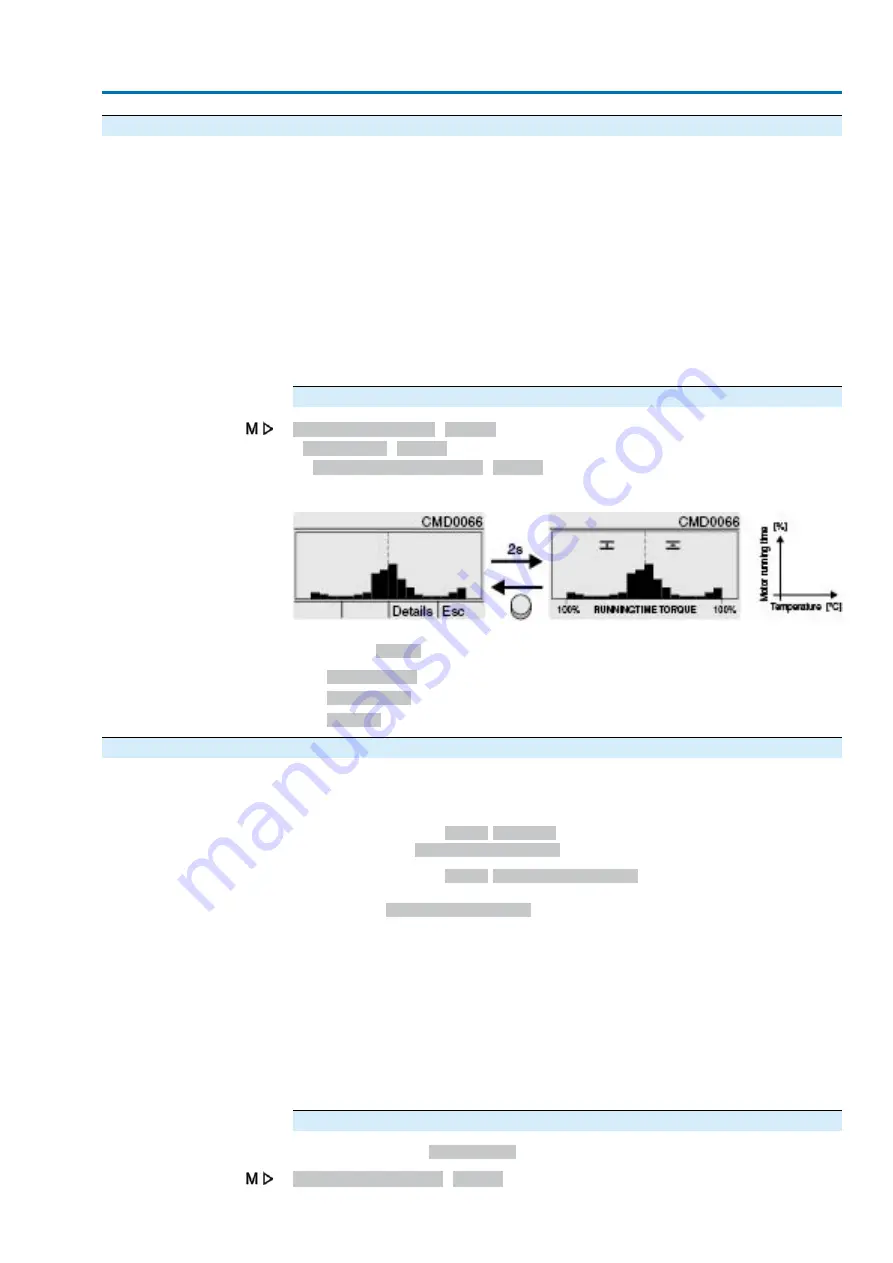
15.4.3.
Motor running time-torque (histogram)
Conditions
MWG position transmitter in actuator
Properties
The torque scale is divided into the following segments for both directions
(OPEN/CLOSE):
from 0 – 30 %
from 30 – 110 % (8 segments with a width of 10 % each)
more than 110 %
During each operation, the counter of the segment corresponding to the currently
required torque will be incremented. The result is shown in a bar chart. The histogram
is cyclically saved once a minute, in case a change has occurred.
Application
The motor running time-torque histogram indicates the actuator load during service
life.
Display motor running time-torque
Asset Management M1231
Histograms M0712
Motor TunTime-Torque M0830
Figure 64: Example of motor running time-torque histogram
The following further information is saved with the histogram (can be requested via
push button
Details
)
●
Starting date:
.
●
Saving date:
.
●
Scaling:
.
15.5.
Maintenance (information and signals)
Properties
Actuator controls monitor various parameters set in the factory which have an impact
on the wear of the actuator. Once one of these parameters exceeds a determined
limit, the actuator controls generate a signal:
●
Status indication:
S0005 Warnings
(AUMA category)
-
Details:
Maintenance required
●
Status indication:
S0010 Maintenance required
(NAMUR category)
-
Details: shows the parameter(s) for which the limit was exceeded, causing
the
Maintenance required
signal.
Apart from the parameter monitoring preset in the factory (MT lifetime
mechanics/seals/lubricant), a fixed maintenance interval can additionally be
configured, triggering the same signal when exceeding the configured time.
The current maintenance status of the monitored parameters is represented in a bar
chart.
Once maintenance is complete, the parameter initiating maintenance must be reset
to zero.
Application
Maintenance on demand, i.e. the function can be used to perform maintenance
depending on the intensity and load of the actuator.
Activate maintenance signals
Required user level:
Specialist (4)
or higher.
Device configuration M0053
141
Actuator controls
ACV 01.2/ACVExC 01.2 Profibus DP
Asset Management