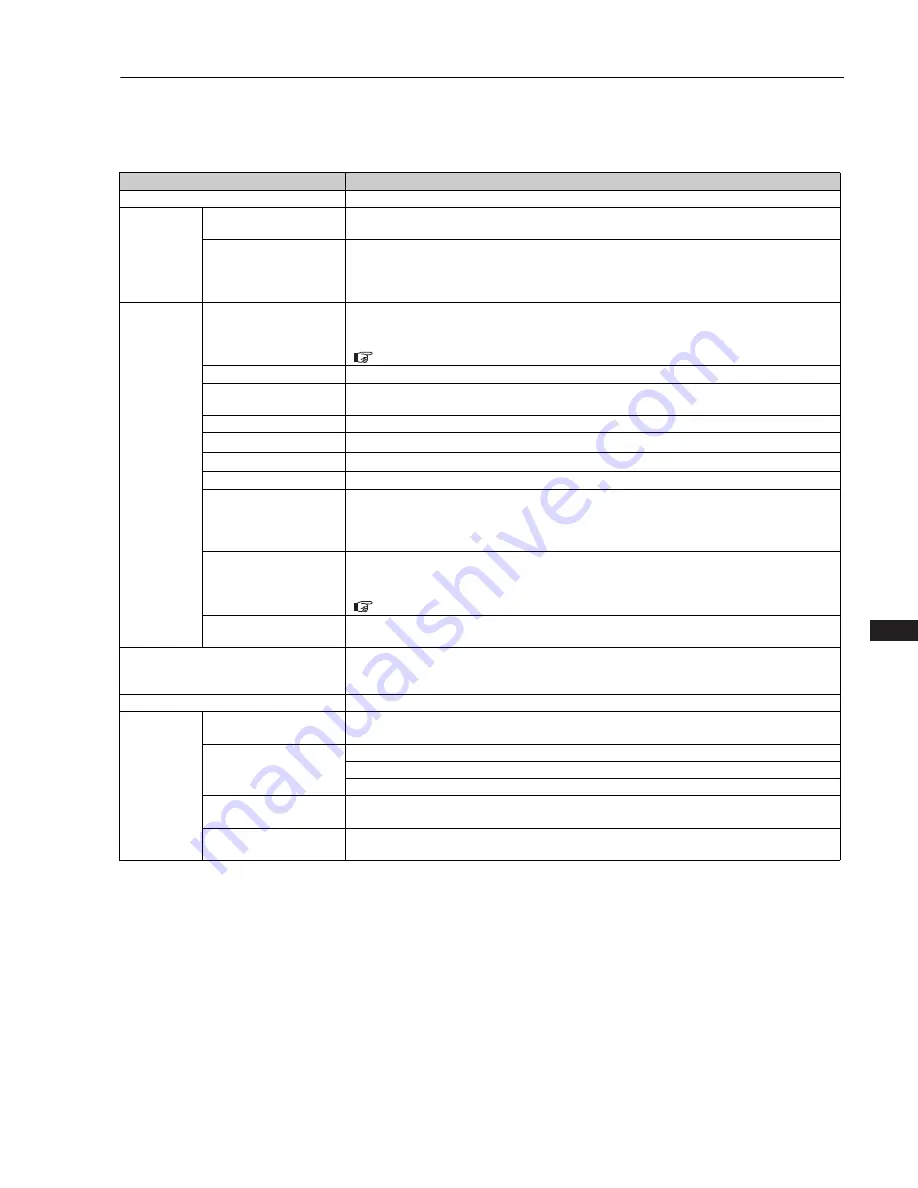
SERVOPACKs
-7W Two-axis EtherCAT Communications Reference SERVOPACKs
481
SER
VOP
A
CKs
Specifications
Item
Specification
Control Method
IGBT-based PWM control, sine wave current drive
Feedback
With Rotary
Servo Motor
Serial encoder: 24 bits (incremental encoder/absolute encoder)
With Linear
Servo Motor
•
Absolute linear encoder (The signal resolution depends on the absolute linear
encoder.)
•
Incremental linear encoder (The signal resolution depends on the incremental linear
encoder or Serial Converter Unit.)
Environ-
mental Con-
ditions
Surrounding Air
Temperature
-5
C to 55
C
With derating, usage is possible between 55
C and 60
C.
Refer to the following section for derating specifications.
Storage Temperature
-20
C to 85
C
Surrounding Air Humid-
ity
95% relative humidity max. (with no freezing or condensation)
Storage Humidity
95% relative humidity max. (with no freezing or condensation)
Vibration Resistance
4.9 m/s
2
Shock Resistance
19.6 m/s
2
Degree of Protection
IP10
Pollution Degree
2
•
Must be no corrosive or flammable gases.
•
Must be no exposure to water, oil, or chemicals.
•
Must be no dust, salts, or iron dust.
Altitude
1,000 m or less.
With derating, usage is possible between 1,000 m and 2,000 m.
Refer to the following section for derating specifications.
Others
Do not use the SERVOPACK in the following locations: Locations subject to static elec-
tricity noise, strong electromagnetic/magnetic fields, or radioactivity
Applicable Standards
UL 61800-5-1, CSA C22.2 No.274, EN50178, EN 61800-5-1,
EN 55011 group 1 class A, EN 61000-6-2, EN 61000-6-4,
and EN 61800-3
Mounting Base-mounted
Perfor-
mance
Speed Control Range
1:5000 (At the rated torque, the lower limit of the speed control range must not cause
the Servo Motor to stop.)
Coefficient of Speed
Fluctuation*
0.01% of rated speed max. (for a load fluctuation of 0% to 100%)
0% of rated speed max. (for a voltage fluctuation of
10%)
0.1% of rated speed max. (for a temperature fluctuation of 25
C
25
C)
Torque Control Preci-
sion (Repeatability)
1%
Soft Start Time
Setting
0 s to 10 s (Can be set separately for acceleration and deceleration.)
Continued on next page.
Summary of Contents for SGM7J-A5A
Page 1: ...yaskawa com SIGMA 7 AC Servo Drives and Motors Technical Supplement...
Page 18: ...18...
Page 21: ...SGMMV 4 SGM7J 18 SGM7A 54 SGM7P 116 SGM7G 134 Rotary Servo Motors...
Page 133: ...Rotary Servo Motors SGM7A 115 Rotary Servo Motors...
Page 151: ...Rotary Servo Motors SGM7P 133 Rotary Servo Motors...
Page 206: ...Rotary Servo Motors SGM7G 188...
Page 223: ...Direct Drive Servo Motors SGM7F With Core Inner Rotor 205 Direct Drive Servo Motors...
Page 251: ...Direct Drive Servo Motors SGM7D With Core Outer Rotor 233 Direct Drive Servo Motors...
Page 276: ...Direct Drive Servo Motors SGMCS Small Capacity Coreless or Medium Capacity with Core 258...
Page 409: ...Linear Servo Motors Recommended Linear Encoders and Cables 391 Cables and Peripheral Devices...
Page 435: ...ST2F Sigma Trac II Linear Stages 418 Sigma Trac II Linear Stages...
Page 495: ...SERVOPACKs 7W Two axis MECHATROLINK III Communications Reference SERVOPACKs 477 SERVOPACKs...
Page 516: ...SERVOPACKs SERVOPACK External Dimensions 498...
Page 547: ...SERVOPACK Cables 530 SERVOPACK Peripheral Devices 540 SERVOPACK Cables Peripherals...
Page 557: ...SERVOPACK Cables Peripherals SERVOPACK Cables 539 Cables and Peripheral Devices...
Page 599: ...Appendices Capacity Selection for Servo Motors 581 Appendices...
Page 615: ...Appendices Capacity Selection for Regenerative Resistors 597 Appendices...
Page 617: ...Appendices International Standards 599 Appendices...
Page 620: ......
Page 621: ......