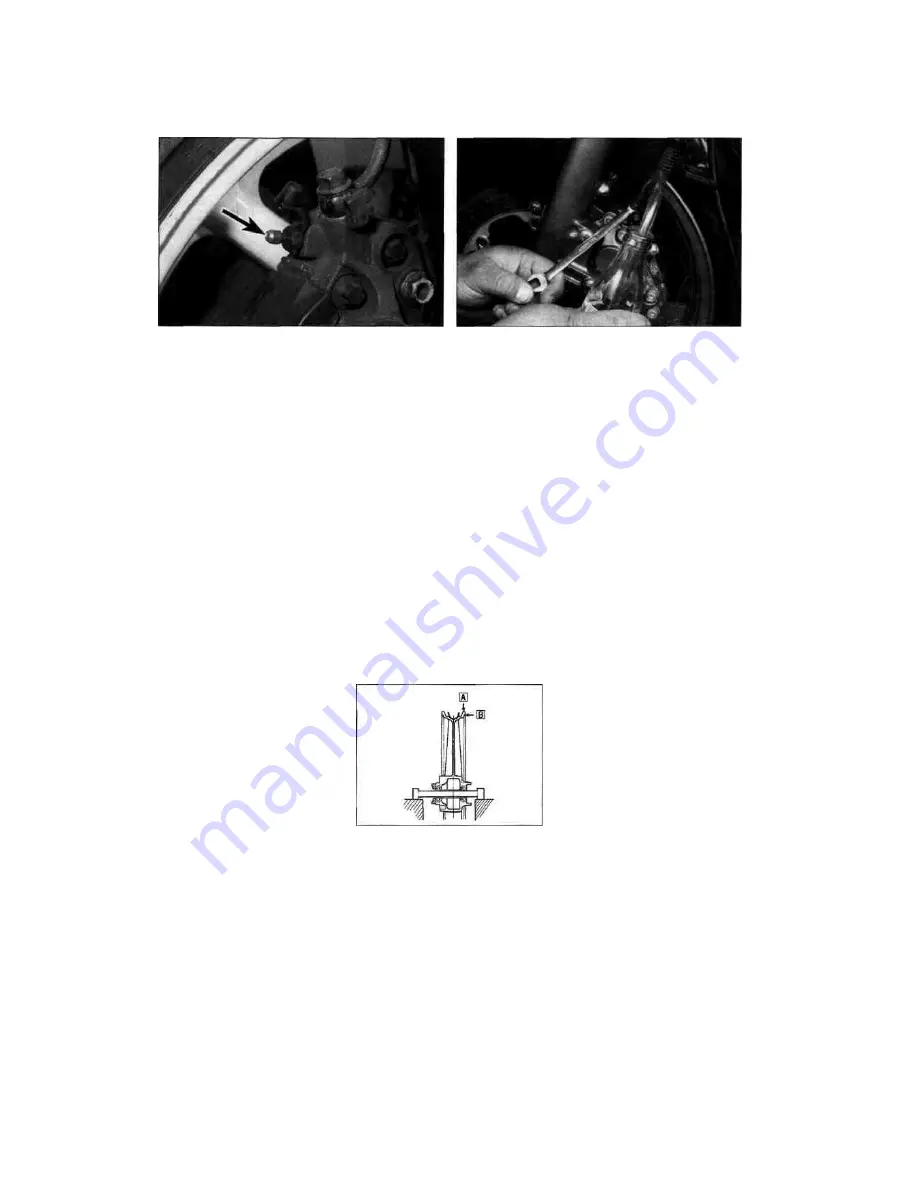
Brakes, wheels and tyres 7*13
8.6a Brake caliper bleed valve
8.6b To bleed the brakes, you need a spanner, a short section of
clear tubing, and a clear container half-filled with brake fluid
6
Flush the old brake fluid from the system, refill
with new DOT 4 brake fluid (see Da//y
(pre-ride)
checks)
and bleed the air from the system (see
Section 8). Check the operation of the brakes
carefully before riding the motorcycle.
8 Brake system - bleeding
1
Bleeding the brakes is simply the
process of removing all the air bubbles from the
brake fluid reservoirs, the hoses and the brake
calipers. Bleeding is necessary whenever a
brake system hydraulic connection is loosened,
when a component or hose is renewed, or when
the master cylinder or caliper is overhauled.
Leaks in the system may also allow air to enter,
but leaking brake fluid will reveal their presence
and warn you of the need for repair.
2 To bleed the brakes, you will need some new
DOT 4 brake fluid, a length of clear vinyl or
plastic tubing, a small container partially filled
with clean brake fluid, some rags and a spanner
to fit the brake caliper bleed valves.
3 Cover the fuel tank and other painted
components to prevent damage in the event that
brake fluid is spilled.
4 When bleeding the rear brake, on TDM
models, remove the seat, and on XTZ models
remove the right-hand side cover (see Chapter
8) for access to the fluid reservoir.
5 Remove the reservoir cover or cap, diaphragm
plate (where fitted) and diaphragm and slowly
pump the brake lever or pedal a few times, until
no air bubbles can be seen floating up from the
holes in the bottom of the reservoir. Doing this
bleeds the air from the master cylinder end of the
line. Loosely refit the reservoir cover.
6 Pull the dust cap off the bleed valve
(see
illustration).
Attach one end of the clear vinyl or
plastic tubing to the bleed valve and
submerge the other end in the brake fluid in the
container
(see illustration).
7
Remove the reservoir cover and check the
fluid level. Do not allow the fluid level to drop
below the lower mark during the bleeding
process.
8 Carefully pump the brake lever or pedal three
or four times and hold it in (front) or down (rear)
while opening the caliper bleed valve. When the
valve is opened, brake fluid will flow out of the
caliper into the clear tubing and the lever will
move toward the handlebar or the pedal will
move down.
9 Retighten the bleed valve, then release the
brake lever or pedal gradually. Repeat the
process until no air bubbles are visible in the
brake fluid leaving the caliper and the lever or
pedal is firm when applied. On completion,
disconnect the bleeding equipment, then tighten
the bleed valve to the torque setting specified at
the beginning of the chapter and install the dust
cap.
10 On TDM and TRX models front brakes, go
on to bleed air from the other brake caliper. On
the rear brake of TDM and TRX models, go on to
bleed air from the other side of the caliper (two
bleed valves are fitted).
11 Install the diaphragm and cover assembly,
wipe up any spilled brake fluid and check the
entire system for leaks.
BWJjrPI
If it's not possible to
.
produce a firm feel to the
HllUT
lever or
pedal the fluid my
be
aerated. Let the brake fluid in the
system stabilise for a few hours and
then repeat the procedure when the
tiny bubbles in the system have settled
out.
Wheels -
inspection and repair
1
In order to carry out a proper inspection
of the wheels, it is necessary to support the bike
upright so that the wheel being inspected is
raised off the ground. Position the motorcycle on
an auxiliary stand. Clean the wheels thoroughly
to remove mud and dirt that may interfere with
the inspection procedure or mask defects. Make
a general check of the wheels (see Chapter 1)
and tyres (see
Daily (pre-ride) checks).
2 Attach a dial gauge to the fork slider or the
swingarm and position its stem against the side
of the rim. Spin the wheel slowly and check the
axial (side-to-side) runout of the rim. In order to
accurately check radial (out of round) runout with
the dial gauge, the wheel would have to be
removed from the machine, and the tyre from the
wheel. With the axle clamped in a vice and the
dial gauge positioned on the top of the rim, the
wheel can be rotated to check the runout
(see
illustration).
3
An easier, though slightly less accurate,
method is to attach a stiff wire pointer to the fork
slider or the swingarm and position the end a
fraction of an inch from the wheel (where the
wheel and tyre join). If the wheel is true, the
distance from the pointer to the rim will be
constant as the wheel is rotated.
Note:
If wheel
runout is excessive, check the wheel or hub
bearings very carefully before replacing the
wheel.
Scaned by Stalker
I
9.2 Check the wheel for radial (out-of-
round) runout (A) and axial (side-to-side)
runout (B)
1