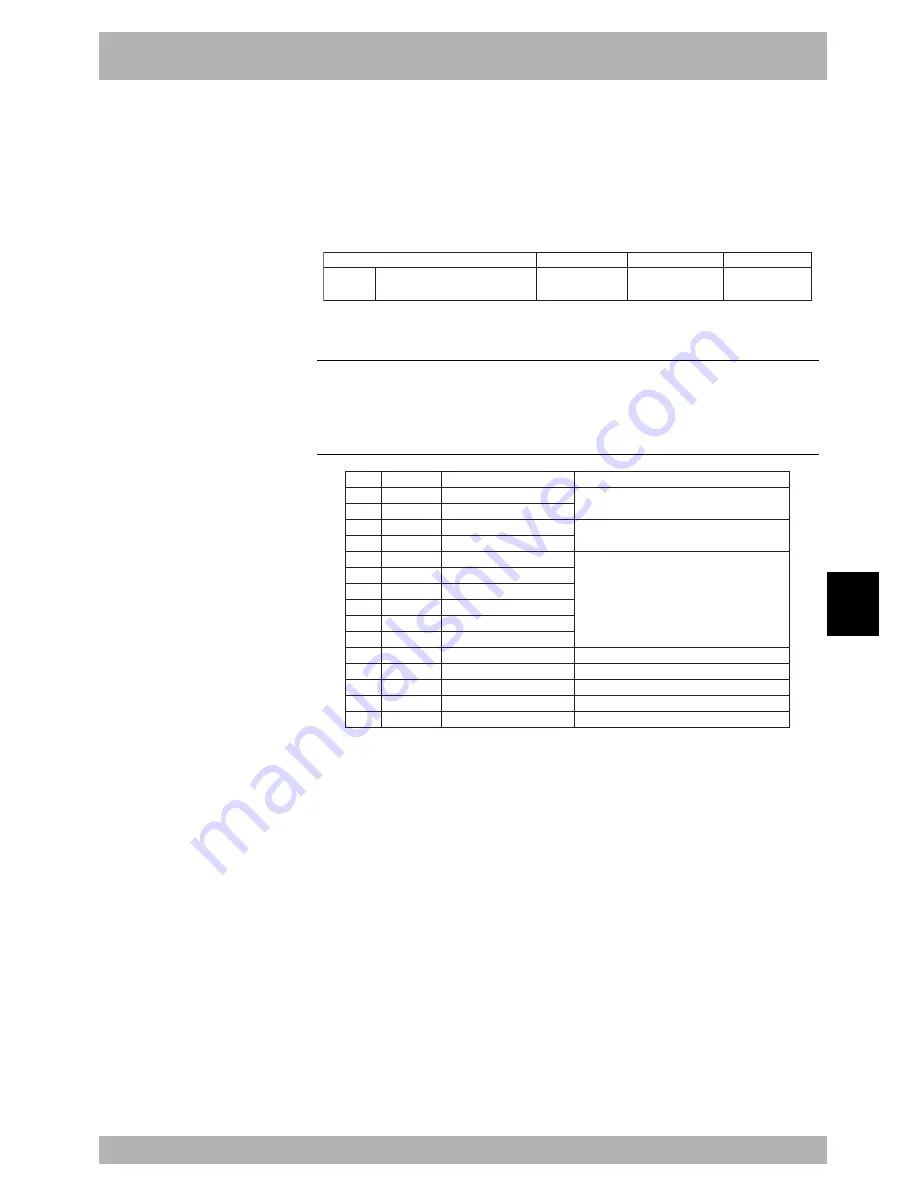
7-
1
7
SAFETY I/O interface
1. SAFETY I/O interface overview
The robot controller is provided with SAFETY I/O interfaces for compatibility with the
system used by the customer. A description of the I/O terminals and connection methods
are explained below.
Connect the I/O terminals correctly for effective operation.
The SAFETY I/O interface contains an emergency stop input and one dedicated input
point.
The input signal is from hereon referred to as DI and the output signal as DO.
Specifications
Connector name Connector model No.
Wire material
SAFETY Emergency stop input : 1 point
Dedicated input
: 1 point
SAFETY
D-SUB15 (male) 0.3mm
2
or more
1.1
Power
The emergency stop input utilizes internal power for emergency stop.
The dedicated input utilizes external 24V power connected via the standard I/O interface.
1.2
Connector I/O signals
PIN
1
2
3
4
5
6
7
8
9
10
11
12
13
14
15
I/O No.
Name
Remarks
DI02
Reserved
EMGIN1
EMGIN2
EMGIN3
EMGIN4
LCKIN1
LCKIN2
LCKIN3
LCKIN4
P.COM
N.COM
EMG 24V
EMG RDY
Reserved
SERVICE mode
Do not use.
Emergency stop input 1
Emergency stop input 2
Emergency stop input 3
Emergency stop input 4
Enable switch input 1
Enable switch input 2
Enable switch input 3
Enable switch input 4
DC+24V (P.COMDI)
GND (N.COMDI)
Emergency stop input power
Emergency stop READY signal
Do not use.
NPN/PNP specs conform to STD. DIO settings.
Common terminal: P. COM / N. COM
Usable only when enable switch
compatible programming box is used.
(MPB-E2)
Internally connected with P. COMDI terminal of STD. DIO.
Internally connected with N. COMDI terminal of STD. DIO.
c
CAUTION
• On the SAFETY connector
supplied with the controller, pin 3
is shorted to pin 13, and pin 4 is
shorted to pin 14. Use these pins
to make an interlock circuit to
ensure the system including the
robot controller operates safely.
• Do not connect an external DC
24V to EMG 24.
• NPN and PNP specifications are
each defined in " 7. I/O
connections" in Chapter 3.
• Do not connect any external
signals to the reserved terminals.
c
CAUTION
Do not keep supplying the external
24V DC power to the standard I/O
interface while controller power is off.
The controller might malfunction if
the external 24V is continuously
supplied.
Summary of Contents for RCX142
Page 1: ...User s Manual ENGLISH E YAMAHA 4 AXIS ROBOT CONTROLLER E92 Ver 1 09 RCX142 ...
Page 2: ......
Page 18: ...MEMO ...
Page 24: ...1 6 MEMO ...
Page 26: ...MEMO ...
Page 36: ...MEMO ...
Page 300: ...4 238 MEMO ...
Page 302: ...MEMO ...
Page 336: ...MEMO ...
Page 360: ...6 24 MEMO ...
Page 362: ...MEMO ...
Page 374: ...MEMO ...
Page 384: ...8 10 MEMO ...
Page 386: ...MEMO ...
Page 394: ...MEMO ...