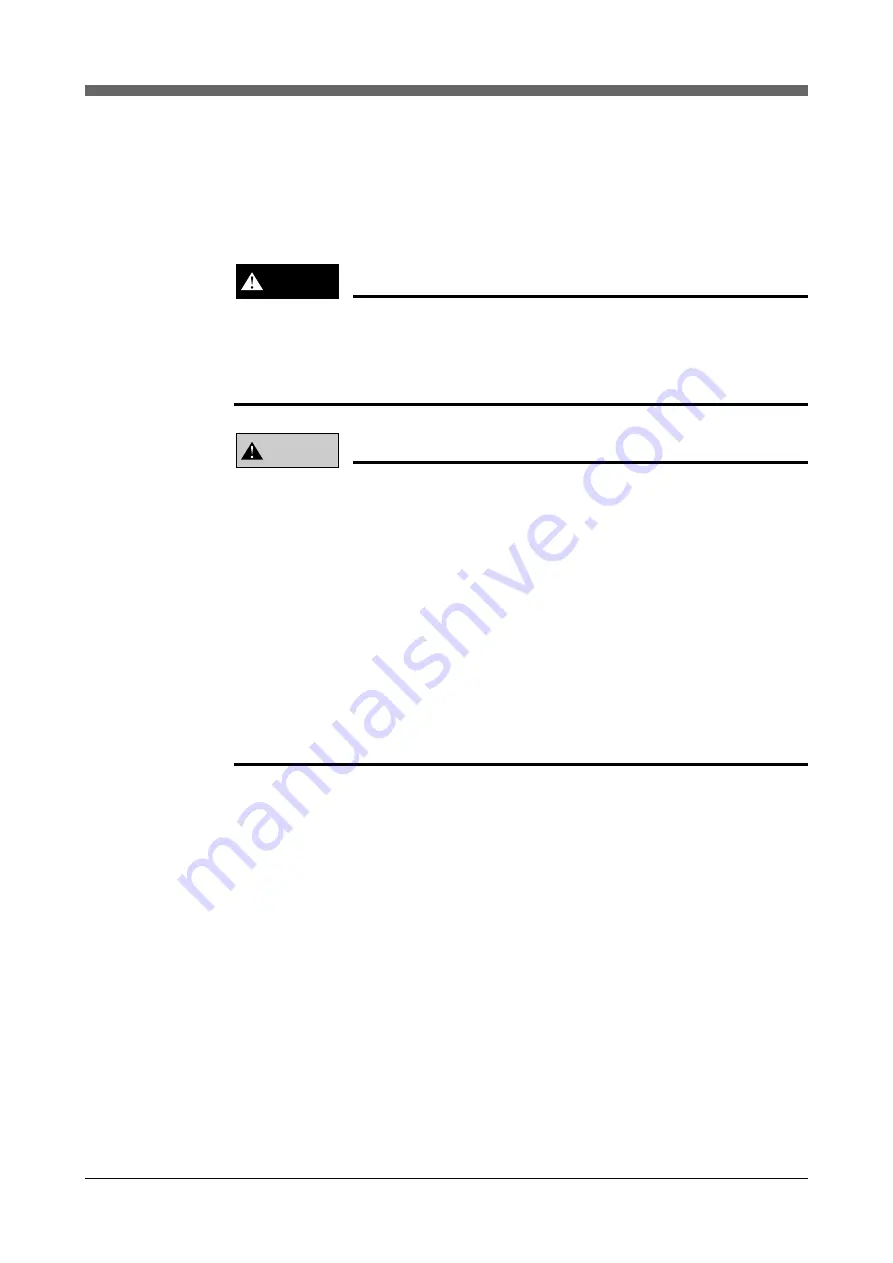
Chapter 4 Periodic Inspection
4-3
4-1
Before beginning work
Periodic inspection and maintenance are essential to ensure safe and efficient operation of
YAMAHA robots. This chapter describes periodic inspection items and procedures for the FLIP-
X series. Before beginning work, read the precautions below and also in Chapter 1 “About Safety”
and follow the instructions.
DANGER
If the inspection or maintenance procedure calls for operation of the robot, stay out of
the working area of the robot during operation. Do not touch any parts inside the
controller.
Keep watching the robot movement and surrounding area so that the operator can
press the emergency stop button if any danger occurs.
WARNING
· When the robot does not need to be operated during adjustment or maintenance,
always turn off the controller and the external switch board.
· Do not touch internal parts of the controller for 5 seconds after the controller has
been turned off.
· Use only lubricant and greases specified by YAMAHA sales office or dealer.
· Use only parts specified by YAMAHA sales office or dealer. Take sufficient care not
to allow any foreign matter to contaminate them during adjustment, parts replace-
ment or reassembly.
· Do not modify any parts on the robot or controller. Modification may result in unsat-
isfactory specifications or threaten operator safety.
· When adjustment or maintenance is complete, retighten the bolts and screws
securely.
· During robot adjustment or maintenance, place a sign indicating that the robot is
being adjusted or serviced, to prevent others from touching the control keys or
switches. Provide a lock on the switch keys or ask someone to keep watch as
needed.
Summary of Contents for FLIP-X Series
Page 1: ...User s Manual ENGLISH E YAMAHA SINGLE AXIS ROBOT E21 Ver 1 15 FLIP Xseries ...
Page 2: ......
Page 6: ...MEMO ...
Page 10: ...MEMO ...
Page 12: ...1 2 MEMO ...
Page 24: ...1 14 MEMO ...
Page 26: ...2 2 MEMO ...
Page 66: ...3 2 MEMO ...
Page 78: ...4 2 MEMO ...
Page 98: ...4 22 MEMO ...
Page 100: ...5 2 MEMO ...
Page 120: ...5 22 MEMO ...
Page 121: ...Chapter 6 Troubleshooting 6 1 Positioning error 6 3 6 2 Feedback error 6 4 ...
Page 122: ...6 2 MEMO ...
Page 125: ...Appendix About machine reference iii Equation of moment of inertia calculation iv ...
Page 126: ...ii MEMO ...