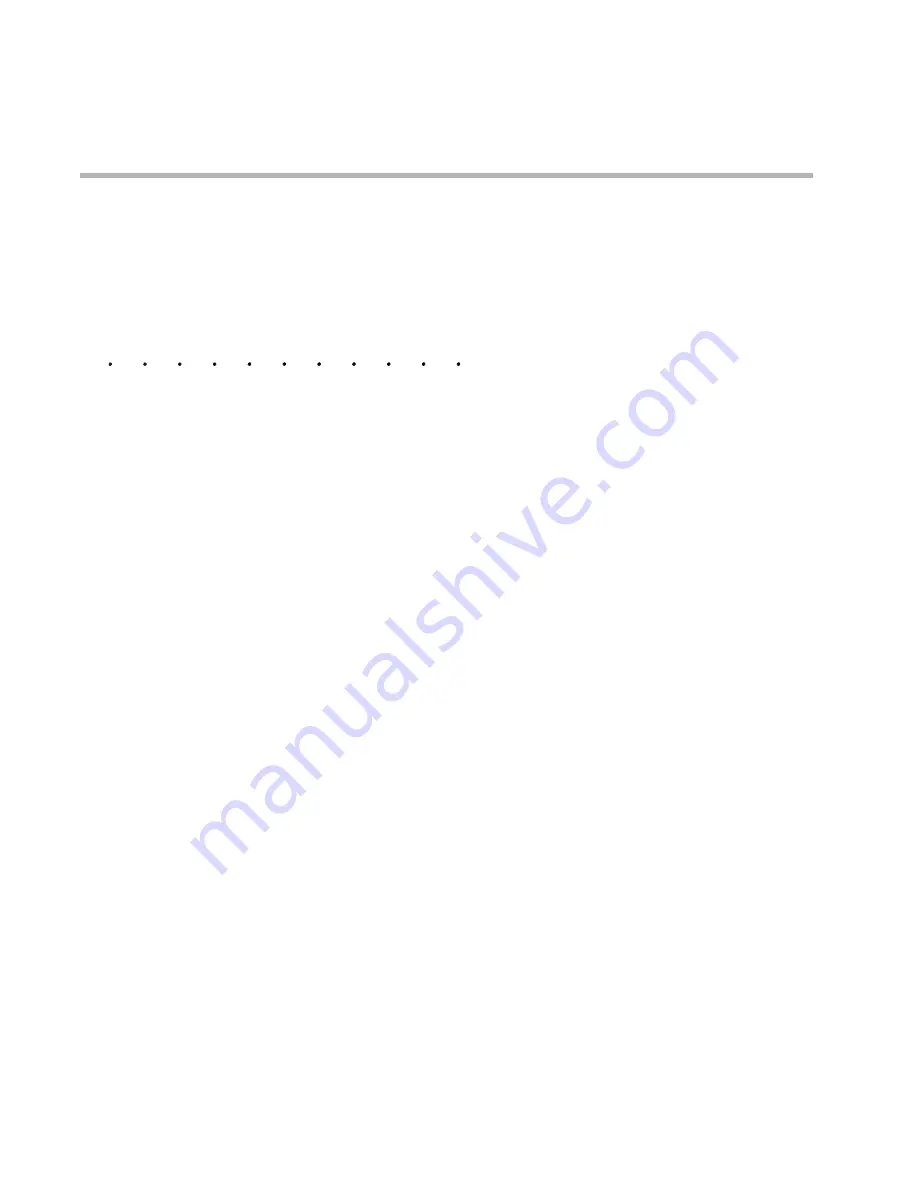
ML-010041 Application Note: Current Compensation
1
Application Note: Current Compensation
Scope
This application note is intended for customers using single-phase, AC
welding controls only. The door of your welding control will be labeled
"AC" or "MFDC". This not does NOT apply to MFDC welding
controls.
Current Compensation Information for AC Products
Background
Information
In order to more accurately control the welding current, the MedWeld
4000 AC welding controls “learn” the characteristics of the welding
transformer and the weld itself. The characteristics “learned” from
previous welds are used to control the current in the weld which is now
being made.
If for any reason, the welding current is not the proper value at any time
during a weld, these ”learned” characteristics allow the weld control to
react very quickly and bring the welding current back to the correct
value to avoid a bad weld. If something has changed on the welding
machine between one weld and the next, the ”learned” information
might cause incorrect welding current for one or two welds after the
change is made.
Changes to the welding machine that could cause momentary incorrect
weld current values are:
1.
Replacement or redressing of welding electrodes.
2.
Replacement of secondary cables or flexible shunts.
3.
Changing the welding transformer tap setting.
4.
Maintenance or parts replacement on the welding gun
5.
Changing the welding force (changing the air pressure on the
welding gun)
For safety reasons, the welding controller should be powered down
before any of the above changes are made. Once the operator verifies is
powered down, make the change, and then turn the welding control back
ON again.
If the electrodes are replaced or redressed, the weld stepper (if one is
being used) must be reset. The action of resetting the stepper will alert
the weld control that the "learned" data will not be valid.
Then, make two welds on a weld coupon or scrap part. Test the second
weld (pull it apart) to be sure it is good. If necessary, readjust the weld
current setting on the control and re-test to be sure a good weld is made.
Once the operator achieves a good weld, they can resume production.