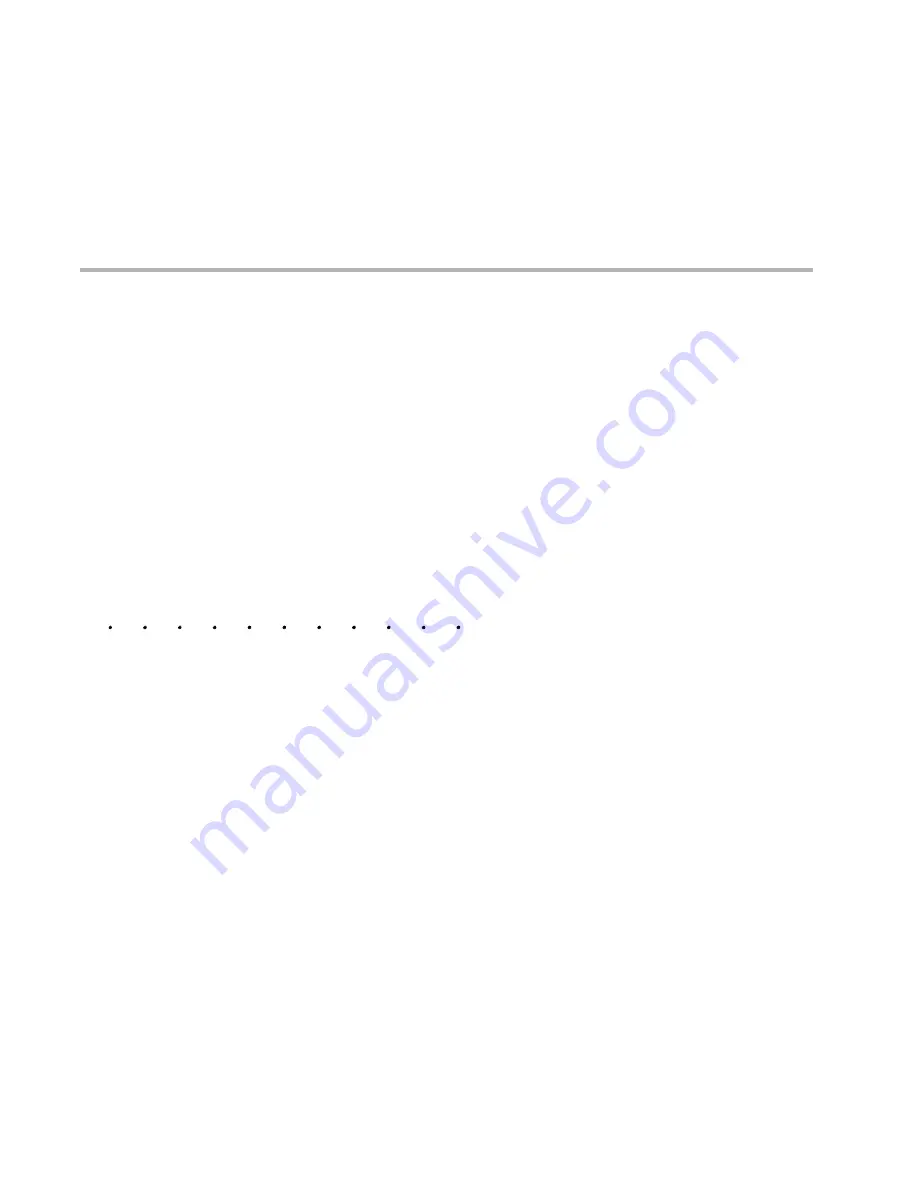
MedWeld 4000 Operator’s Guide
Modified: 9/17/08
4 - 1
M-032116 Programs #T03300, #T02300 and #T02400
Weld Schedules
4
The MedWeld 4000 control is a full-function device, capable of storing
up to 99 unique weld schedules. Each weld schedule can then be
assigned to one of 99 independent steppers.
Several methods are available to program the weld processor. Refer to
“Programming the Weld Processor” on page 2-12 for more information,
or refer to the documentation provided with each programming device.
This chapter does not describe how to create or modify a weld schedule.
(These steps will depend on the programming device.) This chapter only
describes all of the weld functions available for use in programming a
weld schedule.
What is a Weld Schedule?
A weld
schedule
is a list of commands that the control is to execute. For
example, to perform a simple spot weld, you might use a weld schedule
consisting of the following functions:
LINEAR STEPPER #2 ASSIGNED
TURN ON WELD VALVE #1
TURN ON ISOLATION CONTACTOR
SQUEEZE 20 CYCLES
WELD 10 CY 50% I
HOLD 02 CYCLES
WAIT FOR NO INITIATE IF FAULT
TURN OFF WELD VALVE #1
TURN OFF ISOLATION CONTACTOR