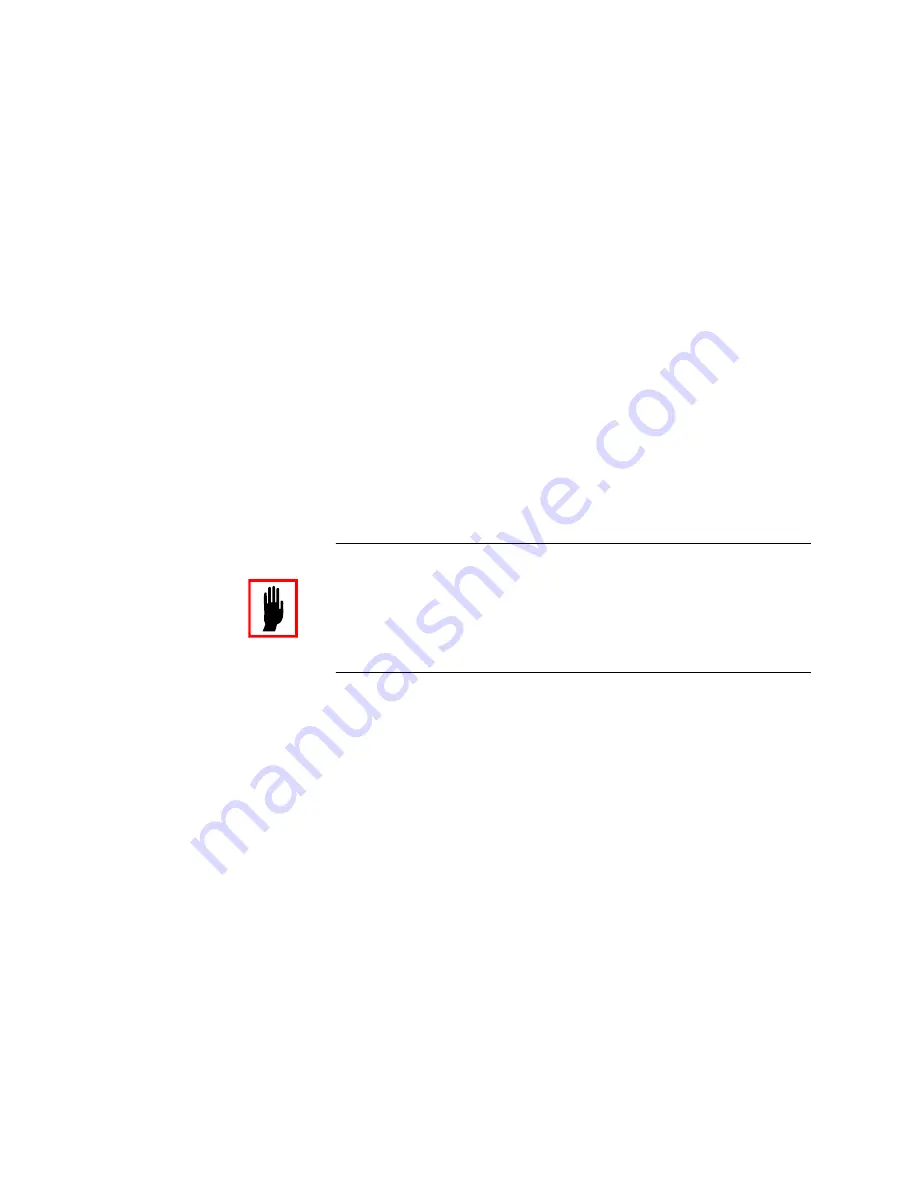
Weld Schedules
4 - 4
Modified: 9/17/08
MedWeld 4000 Operator’s Guide
M-032116 Programs #T03300, #T02300 and #T02400
•
MFDC operation:
High-frequency DC welding has the following
characteristic differences from conventional single-phase welding:
•
There is
essentially no power factor or impedance
in high-
frequency welding that corresponds to the power factor issues
of AC welding. The power factor is high and constant, and the
weld transformer’s secondary circuit is direct current (DC).
•
The welding transformer depends on the applied voltage and
circuit resistance. It is generally independent of the magnetic
effects of the secondary circuit. (Magnetic material in the
secondary is not a consideration.)
•
Given a constant applied voltage, the weld current depends
primarily on the resistance of the weld itself. (Welds with
different resistances will result in different weld current.)
Functions using the AVC firing mode specify weld current as nn%I
(representing the
percentage of maximum available
current). Functions
using the ACC firing mode specify a set amount of
secondary current
,
displayed as
nnnn0 AMPS
.
Caution:
The Transformer Turns Ratio setup parameter
(described on page 5-14) must be accurately
programmed for the control to supply the correct
amount of secondary current in ACC firing mode.
NOTE:
The weld data generated by the control (and displayed at the DEP or a
data monitoring device) does
NOT
include every function that provides
weld current. Keep this in mind when programming a weld schedule.
Only the following functions are included in the Weld Data display:
AVC Firing Mode (%I)
20
WELD nn CY mm %I *
21
TEMPER nn CY mm %I
22
PREHEAT nn CY mm %I
23
POSTHEAT nn CY mm %I
24
PRE-WELD nn CY mm %I
25
WELD nn CY mm.m %I *
26
WELD nn HALF CYCLES mm.m %I *
* The stepper is active during this function. Functions #20–26
select the AVC firing mode.
NOTE:
For all weld functions, mm = 20 – 99
.
(The processor can fire a range
from 20% to 99% I.) For half-cycle functions, the range is from 20.0% to