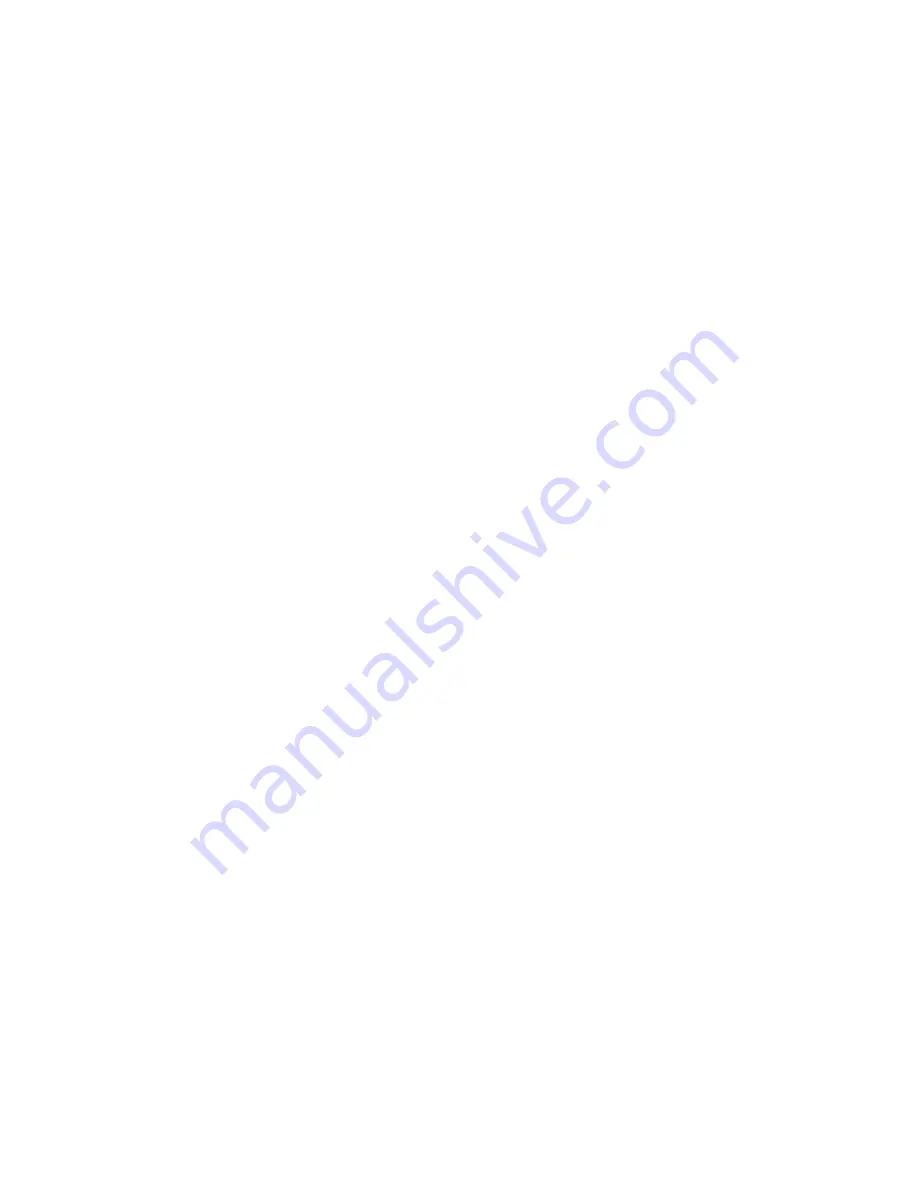
MedWeld 4000 Overview
1 - 26
Modified: 12/16/08
MedWeld 4000 Operator’s Guide
M-032116 Programs #T03300, #T02300 and #T02400
Weld Processor
The weld processor provides direct communications.
When it receives a START WELD command from the host, the weld
processor starts executing the weld sequence selected. When weld
current will be required, it tells the inverter to fire. (The charging pack is
already activated before the START WELD command.)
When the DC bus voltage stabilizes, the inverter is ready to weld. It
activates the IRTW signal, and the weld processor is capable of sending
firing signals to the inverter. The inverter performs the power
conversion to provide the high-voltage DC current to the welding
transformer.
At the end of the weld sequence, the weld processor drops out the
isolation contactor for the weld transformer.
NOTE:
If your configuration provides the weld transformer isolation contactor,
the inverter remains activated and is de-activated only by inverter fault
conditions or power-down of the weld control. Refer to the drawings
provided with your system for more information.
The weld processor requests an upload of weld data and active fault
conditions from the inverter. It functions as a slave device in the
communications link. (It can only respond to requests for data; it cannot
initiate communications with the weld processor.)
The weld processor indicates any fault conditions detected at the
inverter, either at the data entry panel, or at another MedLAN device
connected to the weld processor. (This can be the
Weld Support System
or
MedVIEW
.)
Faults generated in this system are of two types:
•
Faults generated by the weld processor, and
•
Faults generated by the MFDC inverter.
Inverter faults will de-energize the charging pack. Processor faults will
inhibit the firing signal to the inverter (but do not de-energize the
charging pack).