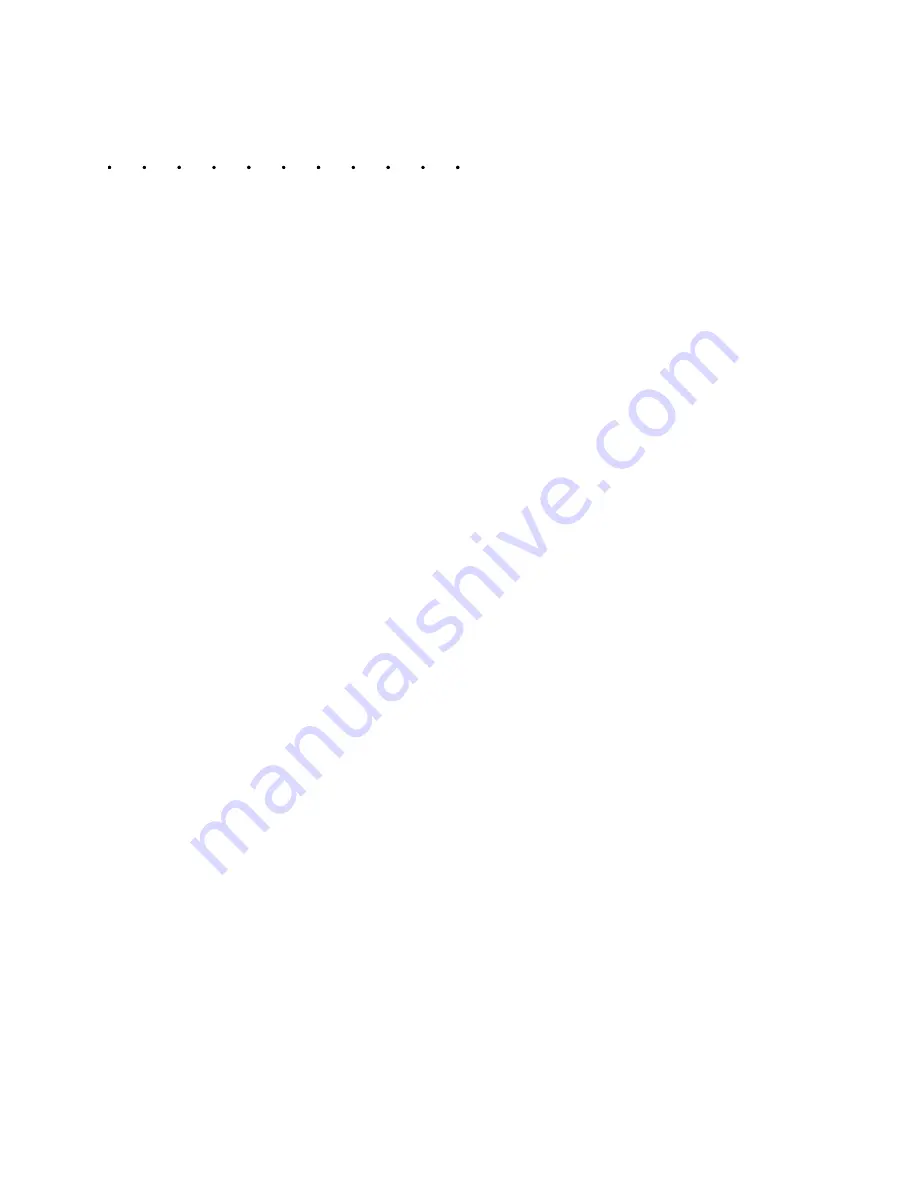
9^cdQ\\Y^WdXU=UTGU\T$
=UTGU\T$ ?`UbQd_bµc7eYTU
=_TYVYUT*'") #
""#
= #"!!&@b_WbQ]cD ## D "# Q^TD "$
5HTXLUHG(OHFWULFDO&RQQHFWLRQV
All electrical connections must be mechanically clean and secure. They
should have no signs of wear, fretting, damage or chemical corrosion.
These requirements are CRITICAL for the high-voltage power
connections to, from and within the control. The customer must
complete these connections:
3RZHU&RQQHFWLRQV
•
The incoming power feed lines L1, L2 and L3 enter the circuit
breaker 1CB. For more details, refer to “Required Torque for
Electrical Connections” on page 2-24.
•
The connection between connector 1CI on the 689 board and the
1PD board (for a Type 1 inverter, p/n 955-5000), or the 1CPU board
(for a Type 2 inverter, p/n 955-6000). This applies only to
integration kits.
,2&RQQHFWLRQV
•
If operating the control on a network, connect the MedLAN
connector J2 on the weld processor board 1CPU.
•
For support of analog I/O, either or both connectors J4 and/or J5 on
the weld processor board 1CPU (Type 2 inverter). Wire a ferrite
bead across each connection.
•
If using the transformer over-temperature switch, wire to terminals
1TB/TS1 and 1TB/TS2 on terminal block 1TB.
•
The CONTROL STOP signal can be internally- or externally-
sourced. Refer to the schematics supplied with the control for the
available wiring options.
•
If using the Type 1 inverter, the secondary current-sensing coil 1CC
has leads designated 1RD-J2-1 and 1RD-J2-2. Connect these leads
to terminals 1 and 2 on connector J2 of the 7923 board, 1RD.
•
Connect the I/O according the communication scheme being used:
•
DIO:
Discrete wiring to each required connector.
•
DNET:
Connect the DeviceNet cable to connector J3 on the
communications daughter board.
•
Profibus:
Connect the DB-9 cable to connector J2 on the
communications daughter board.
•
Serial I/O:
Connect Belden #9463 (“Blue Hose”) cable to
connector J4 on the communications daughter board.