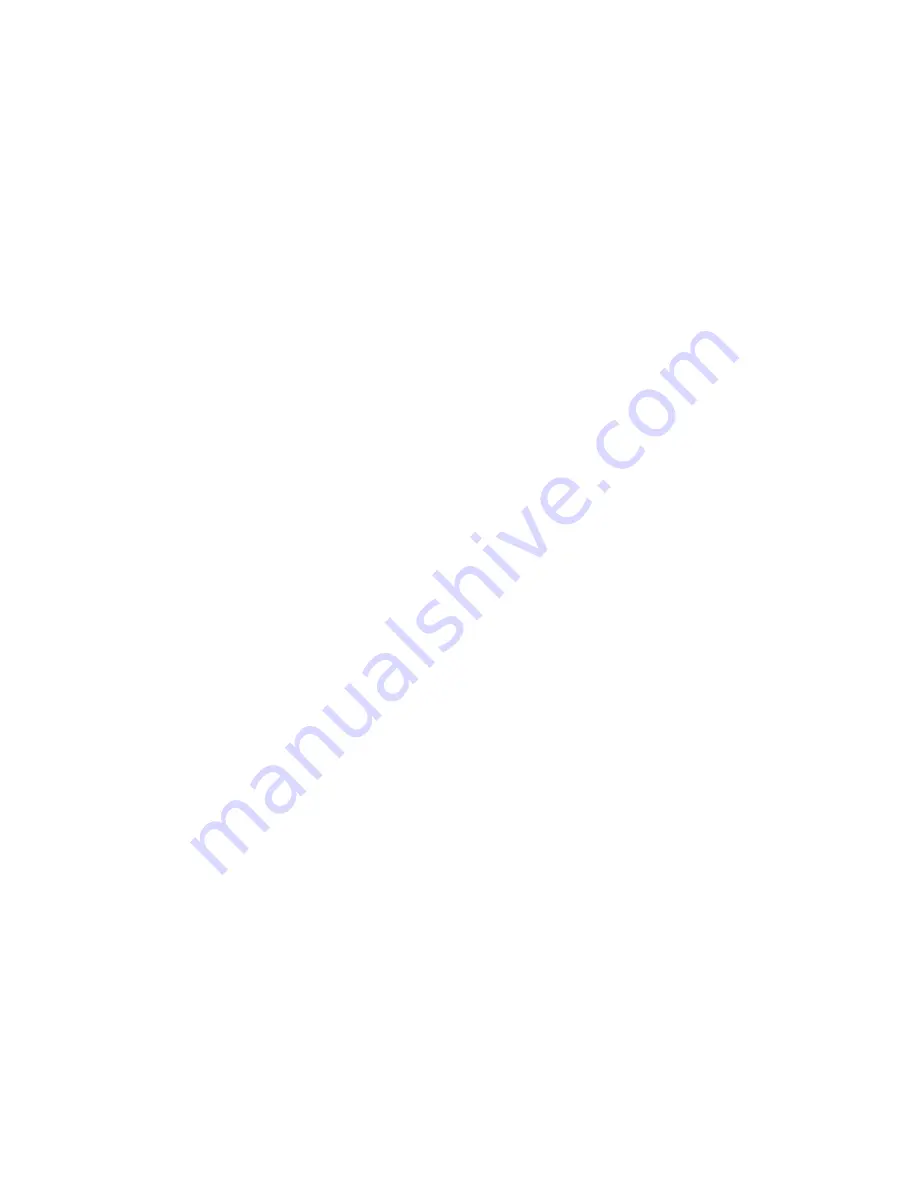
Setup Parameters
MedWeld 4000 Operator’s Guide
Modified: 9/17/08
5 - 13
M-032116 Programs #T03300, #T02300 and #T02400
VALVE 1 INITIAL PRESSURE (PSI): (
T03300 only
)(nn)
VALVE 2 INITIAL PRESSURE (PSI): (
T03300 only
)(nn)
This parameter lets you set a base pressure for each pressure valve.
This sets the initial pressure to be supplied to the valve at power-up
and at the end of a weld sequence.
nn
sets the pressure in the range 0 – 99 PSI. The default setting is
50
PSI.
HEAT CYCLE LIMIT (0=SEAM):
(0–99)
This parameter defines the maximum number of consecutive cycles
of heat conduction. (After nine consecutive cycles without
conduction, the heat cycle counter is reset to zero.)
For seam welding applications, disable this function by setting the
cycle limit to zero.
ISOLATION CONTACTOR DELAY (SEC): (0–99)
This parameter tells the control how long to hold the isolation
contactor pulled in after the function TURN OFF ISOLATION
CONTACTOR executes. This is designed to prevent wear on the
isolation contactor caused by dropping in and out between welds.
When the ISOLATION CONTACTOR SAVER input is available
and set LOW, it disables this delay timer.
NOTE:
The function ISO CONTACTOR DELAY can be inserted into the weld
schedule. If written in the weld schedule the function will override this
setup parameter, but only applies for that particular weld schedule and
when in sequence. If not programmed into a weld schedule all delays for
the contact default to the setup parameter. If programmed as a function
in the weld schedule the delay function must come before TURN ON ISO
CONTACTOR.
HIGH CURRENT LIMIT WINDOW:
(0–99)
LOW CURRENT LIMIT WINDOW:
(0–99)
These two parameters define a global current range for every weld
schedule.
The MedWeld 4000 calculates the high current window as a
percentage boost over the current expected. The low current
window is a percentage decrease from the expected current. (The
expected current is the base current—programmed in the weld
function—plus the current that the stepper is providing.)
For ACC, the base is the actual secondary current value
programmed. %I is derived by determining the maximum current
deliverable, and the percentage of that current programmed in the
weld schedule.