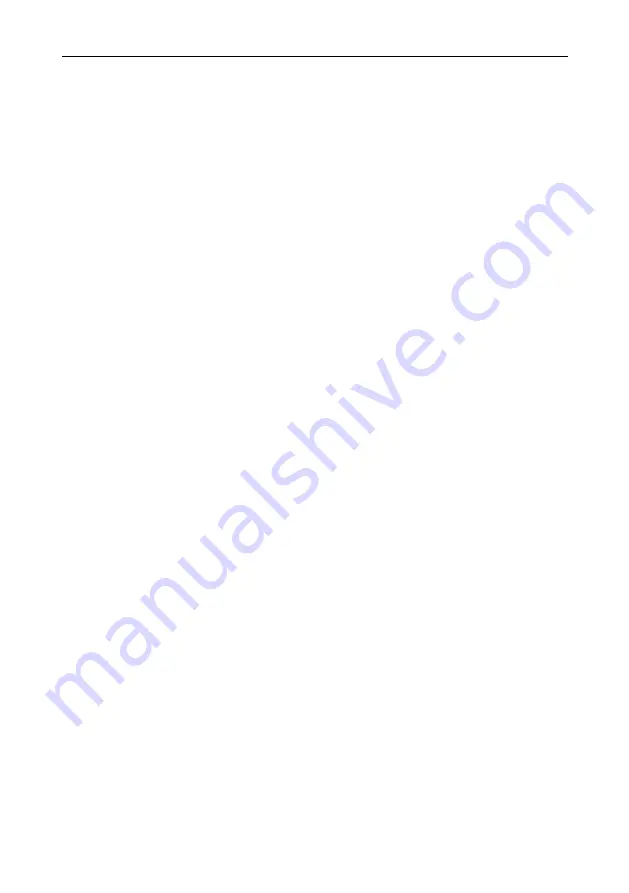
Operation and Display
VD300 Series Inverter User Manual
- 40 -
2) The function code cannot be modified in running status, and inverter in running state, it can be
modified only after the it stopped; the parameter values in the condition of running normally on display,
in the condition of stop flashing.
4.1.4 State Display
The state display of operation panel is divided into stopping states parameter display, run state
parameter display, function code parameter editing state display and fault alarm state display and so
on.
1. Stop parameter display state
When the inverter is in the stopping state, the keyboard will display stopping parameters which is
shown in figure. The 3bits on right indicator stand for the unit of the parameter, the 3bits on left
indicator stand for current status. Such as, the run direction signal is reverse, then FWD/REV light on.
Select check menu(also called user setup/user customize), only display the function code which is
different from parameter set value and manufacturer value, press ^/v can browse function code which
is different from all the parameter set value and manufacturer value, are convenient for the user to
confirm which parameter are changed.
Press>> key to display stop status parameter recycling. Function code P10.05 defines stop status
parameter.
2. Displayed state of run parameters
After the inverter receives Enabled run commands, the inverter will enter into the run state and the
keypad will display the run parameters. RUN is on while the FWD/REV is determined by the current
run direction which is shown as flow.
Press>> key to display run status parameter recycling. Function code P10.03 P10.04 defines run
status parameter.
3. Function code editing status
In stop/run/error alarm status, press MENU/ESC can enter into edit status (if with password then input
it, refer to P29.00). Edit status has 2 levels menu in sequence: function code group or function
code----function code parameter, press ENTER/DATA key enter into function parameter display status.
In function parameter display status, press ENTER/DATA key to save and jump to the next parameter,
press MENU/ESC to quit to previous parameter.
4.2 Motor Parameter Self-learning
Select vector control mode, before inverter operation, must input the parameter from the nameplate of
the motor, VD300 series inverter will match standard motor parameter according to this message.
Vector control mode is highly dependent on motor parameter, so to acquire good control performance,
it needs correct motor parameter.
Pay attention to below points during motor parameter self-learning.
1) Firstly to set run command source parameter P00.01=0 as control panel command channel, if
motor self-learning required, then remove motor loading.
2) Input motor nameplate parameter correctly, including rate power/rate voltage/rate current/rate
frequency/rate RPM, its corresponding function code P02.01~P02.05. If select motor 2,
corresponding function code P20.01~P20.05
3) Via set function code P00.23 to select self-learning type, press ENTER/DATA to confirm displayed
“-TUN-”. Press RUN to start motor self-learning, and RUN light on, motor parameter self-learning is
beginning. Once it is completed, LED will display “END”.
4) After motor self-learning check P02.10 parameter, generally this value less than 60% of rate
current P02.03, if not it is abnormal, need to do self-learning again, and confirm if motor is with empty
loading.
5) When it is unavailable to get motor nameplate message, manufacturer set value can be used. It is
only need to input motor power (motor 1 is P02.01, motor 2 is P20.01), no need motor self-learning.
6) If need to get the motor self-learning result recovered to manufacturer value, only need to revise
motor rate power(motor 1 is P02.01, motor 2 is P20.01) then change back to required power, the
parameter after self-learning can recover to manufacturer value automatically.
Summary of Contents for VD300 Series
Page 2: ......