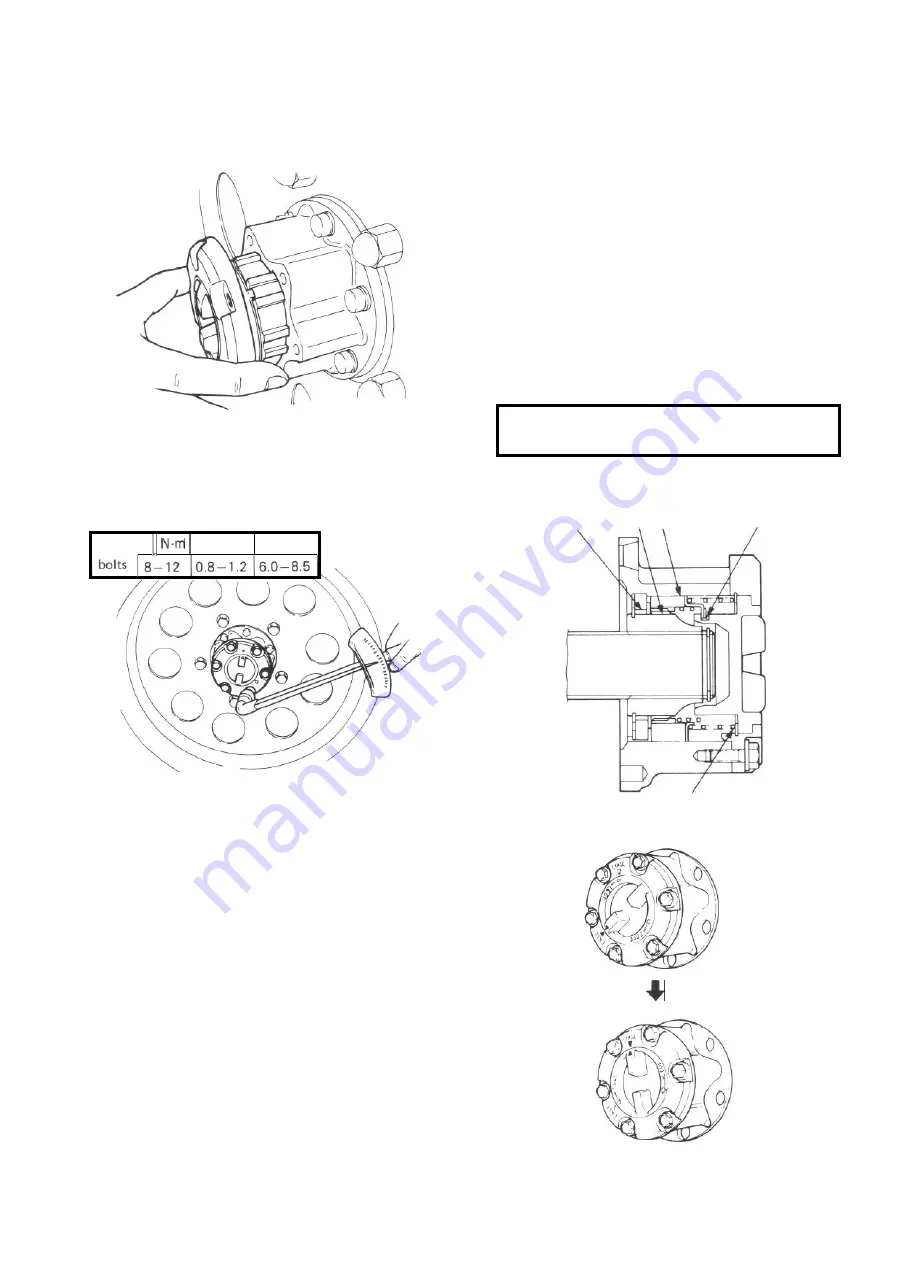
There are two follower stopper nails and two
grooves which can be fitted freely.
Fig. 17-5-8
6) Fix cover ass’y to body ass’y with cover
bolts.
Tightening torque
Cover
kg-m
lb-ft
Fig. 17-5-9
7) To check free wheeling hub operation, jack
up the front end, move the knob of free
wheeling hub between “FREE” and “LOCK”
positions and check for smoothness. Also
check if wheel operates correctly with the
k n o b a t “ F R E E ” a n d “ L O C K ” p o s i t i o n s
and by rotating wheel by hand.
Maintenance Service
The car equipped with free wheeling hubs are
subject to the following periodical checks.
To check free wheeling hubs operation, jack up
the front end, move the knob of free wheeling
hub between “FREE” and “LOCK” positions
and check for smoothness. Also check if wheel
operates correctly with the knob at “FREE”
and “LOCK” positions and by rotating wheel by
hand.
Should the check result be unsatisfactory,
remove free wheeling hub cover and grease each
sliding surface with SUZUKI SUPER GREASE
A (99000-25010) or multipurpose grease after
cleaning each sliding part.
If faulty operation is still noted even after
greasing, correct defective part or replace it
with a new one.
CAUTION:
Hubs should not be packed with grease.
For installation, refer to
“Installation Instruc-
tion”
in this section.
Greasing point
FREE POSITION
LOCK POSITION
Fig. 17-5-11
17-29
Fig. 17-5-10
Summary of Contents for Samurai 1986
Page 1: ......
Page 9: ...0 9...
Page 10: ...0 6...
Page 11: ...0 7...
Page 12: ...0 8...
Page 13: ...0 9...
Page 14: ...0 10...
Page 15: ...0 11...
Page 19: ...1 2...
Page 20: ...1 3...
Page 119: ...r a l I 29 Fig 4 1 1 Carburetor exploded view 4 3...
Page 120: ...N Fig 4 l 2 Carburetor cross section 4 4...
Page 154: ......
Page 155: ...T c c x 5 5 3...
Page 347: ...Fig 17 1 34 17 12...
Page 348: ...17 13...
Page 353: ...Fig 17 2 12 17 18...
Page 354: ...17 19...
Page 360: ...Fig 17 3 19 Fig 17 3 20 Fig 17 3 21 5 Fig 17 3 23 Ci Fig 17 3 24 Fig 17 3 22 17 25...
Page 424: ...Fig 19 6 1 19 38 19 6 PARKING BRAKE...
Page 448: ...20 13...
Page 450: ...21 2...
Page 475: ...22 5...
Page 476: ...22 6...
Page 477: ...22 7...
Page 478: ...22 8...
Page 479: ...22 9...
Page 480: ......
Page 481: ......