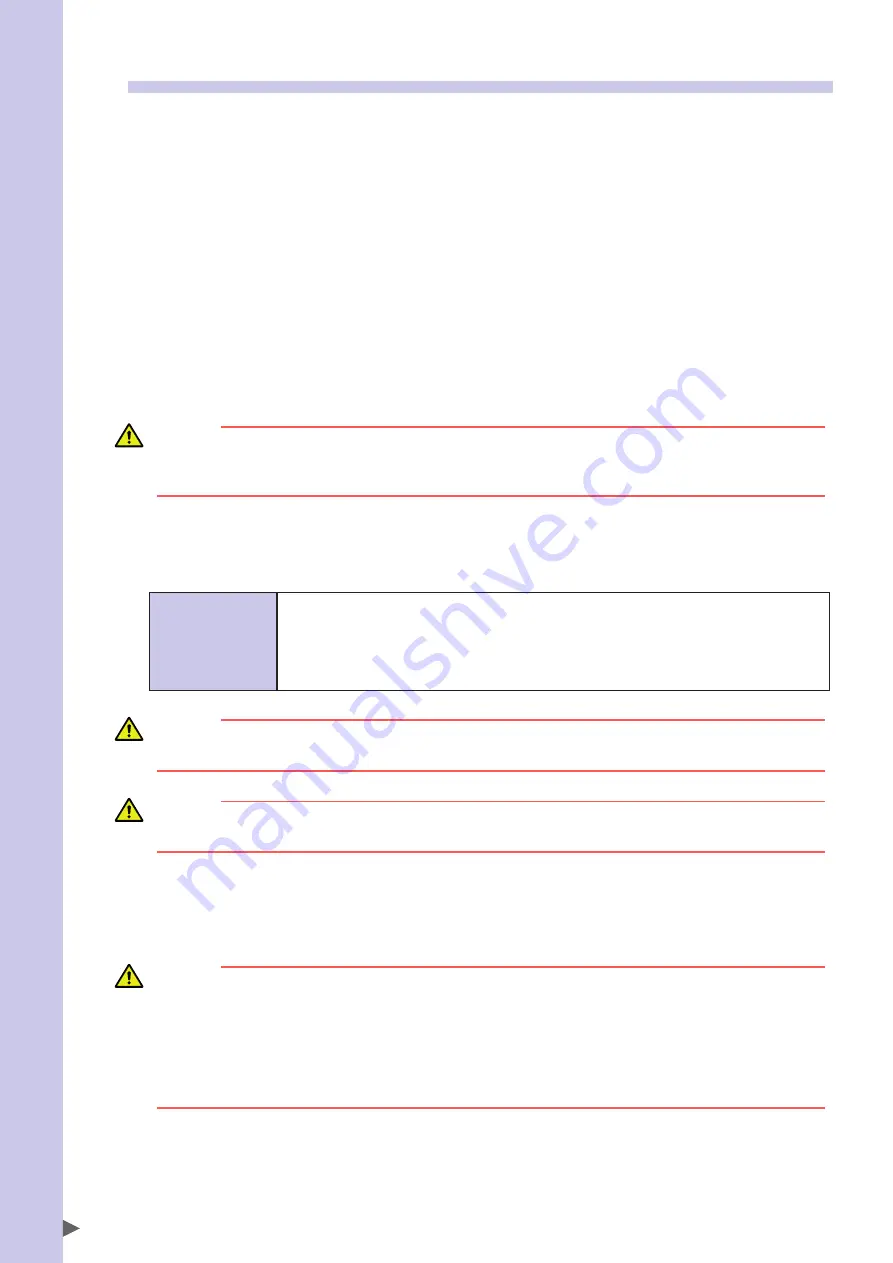
Safety Instr
uctions
S-24
7.2
Robot protective functions
Protective functions for OMRON robots are described below.
1.
Overload detection
This function detects an overload applied to the motor and turns off the servo.
If an overload error occurs, take the following measures to avoid such errors:
1. Insert a timer in the program.
2. Reduce the acceleration.
2.
Overheat detection
This function detects an abnormal temperature rise in the driver inside the controller and turns off the servo.
If an overheat error occurs, take the following measures to avoid the error:
1. Insert a timer in the program.
2. Reduce the acceleration.
3.
Soft limits
Soft limits can be set on each axis to limit the working envelope in manual operation after return-to-origin and during automatic
operation. The working envelope is the area limited by soft limits.
WARNING
SOFT LIMIT FUNCTION IS NOT A SAFETY-RELATED FUNCTION INTENDED TO PROTECT THE HUMAN BODY.
TO RESTRICT THE ROBOT MOVEMENT RANGE TO PROTECT THE HUMAN BODY, USE THE MECHANICAL STOPPERS
INSTALLED IN THE ROBOT (OR AVAILABLE AS OPTIONS).
4.
Mechanical stoppers
If the servo is turned off by emergency stop operation or protective function while the robot is moving, then these mechanical
stoppers prevent the axis from exceeding the movement range. The movement range is the area limited by the mechanical
stoppers.
SCARA robots
• The X and Y axes have mechanical stoppers that are installed at both ends of the maximum movement range. Some
robot models have a standard feature that allows changing the mechanical stopper positions. On some other
models, the mechanical stopper positions can also be changed by using option parts.
• The Z-axis has a mechanical stopper at the upper end and lower end. The stopper positions can be changed by
using option parts.
• No mechanical stopper is provided on the R-axis.
WARNING
AXIS MOVEMENT DOES NOT STOP IMMEDIATELY AFTER THE SERVO IS TURNED OFF BY EMERGENCY STOP OR
OTHER PROTECTIVE FUNCTIONS, SO USE CAUTION.
CAUTION
If the robot moving at high speed collides with a mechanical stopper installed in the robot (or available as option), the robot may be
damaged.
5.
Z-axis (vertical axis) brake
An electromagnetic brake is installed on the Z-axis to prevent the Z-axis from sliding downward when the servo is OFF. This
brake is working when the controller is OFF or the Z-axis servo power is OFF even when the controller is ON. The Z-axis brake
can be released by the programming unit / handy terminal or by a command in the program when the controller is ON.
WARNING
THE VERTICAL AXIS WILL SLIDE DOWNWARD WHEN THE BRAKE IS RELEASED, CAUSING A HAZARDOUS
SITUATION. TAKE ADEQUATE SAFETY MEASURES IN CONSIDERATION BY TAKING THE WEIGHT AND SHAPE INTO
ACCOUNT.
• BEFORE RELEASING THE BRAKE AFTER PRESSING THE EMERGENCY STOP BUTTON, PLACE A SUPPORT UNDER
THE VERTICAL AXIS SO THAT IT WILL NOT SLIDE DOWN.
• BE CAREFUL NOT TO LET YOUR BODY GET CAUGHT BETWEEN THE VERTICAL AXIS AND THE INSTALLATION
BASE WHEN PERFORMING TASKS (DIRECT TEACHING, ETC.) WITH THE BRAKE RELEASED.
Summary of Contents for R6YXGLC250
Page 1: ...ZX T Series Cat No I158E EN 02A R6Y XGC XGP series INSTALLATION MANUAL SCARA Robots XG Series...
Page 2: ......
Page 8: ......
Page 34: ......
Page 36: ......
Page 38: ......
Page 42: ......
Page 44: ......
Page 50: ......
Page 86: ......
Page 91: ...Chapter 4 Periodic inspection Contents 1 List of inspection items 4 1...
Page 92: ......
Page 95: ...Chapter 5 Harmonic drive replacement period Contents 1 Overview 5 1 2 Replacement period 5 2...
Page 96: ......
Page 100: ......
Page 104: ......
Page 106: ......
Page 135: ......