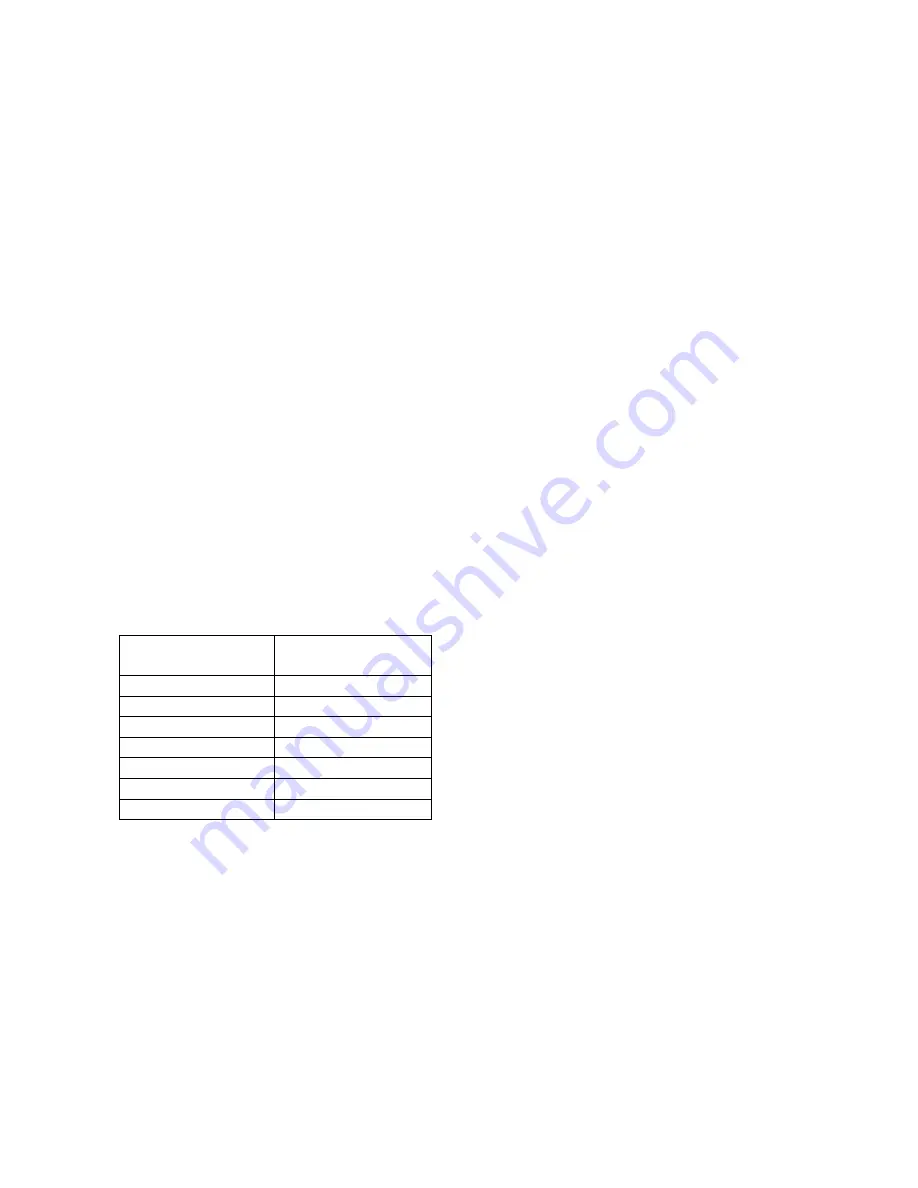
User Switches C1 Submenu
99
MAINS DIP ENABLE
(Mains Dip Enable)
When enabled, the function will reduce the
speed (by the percentage defined by the
MAINS DIP SPEED parameter) when the drive
goes into ‘low voltage’ mode. ‘Low voltage’
mode is defined as when the drive declares a
UV alarm, which is defined by the Input line-to-
line voltage (INPUT L-L VOLTS) parameter
and the Undervoltage Alarm Level (UV ALARM
LEVEL).
ENDAT INTERPOLATION
(EnDat Interpolation)
This parameter determines how precisely the
drive is able to sense the angular position of
the motor shaft. Higher interpolation values
correspond to a more precise sensing of the
shaft position. The default setting provides an
optimal ride quality for most applications. It
may be necessary to lower this parameter for
faster motors or to raise it for slower motors.
For any installation the Contract Mtr Spd (A1)
should not exceed the value shown in Table 16
for a given EnDat Interpolation setting. The
recommended maximum Contract Mtr Spd
(A1) settings will allow over-speed test
operation up to 150%.
Setting of EnDat
Interp (C1)
Maximum Contract
Mtr Spd (A1) in RPM
8
1200 RPM
32
1200 RPM
64
580 RPM
128
290 RPM
256
140 RPM
512
70 RPM
1024
30 RPM
Table 16: Maximum acceptable setting of
Contract Mtr Spd (A1) for a given EnDat
Interp (C1)
PULSE PRETORQUE (PPT)
PPT
The Pulse PreTorque (PPT) function
determines the car loading before releasing
the brake. This feature is best suited to brakes
where there is a small amount of mechanical
float as is typical on some MRL applications.
This feature can be used where a traditional
Load Weighing device is not available and
instead of the existing Anti-Rollback (ARB)
function. Where the ARB function is a reactive
solution to rollback, PPT function determines
the car loading before releasing the brake so
as to greatly reduce rollback. This feature will
disable ARB when PPT is enabled.
This feature is turned on simply by setting PPT
Select in the C1 menu to ‘ENABLED’.
UMD Brake Monitoring
Brake Monitoring
This feature is intended to conform as part of
an Uncontrolled Movement Detection System.
From this release, the drive now has the option
to separately monitor the status of two
Mechanical Brake switches. In addition, there
are now two Brake Pick Faults (One for each
switch), to help fault finding in the event that
the feedback from the switches isn’t as the
drive expects.
The way the Brake Pick Faults are declared
has also changed, and they will now persist
through a power cycle and Fault Reset signal
to ensure the fault is cleared by a competent
person. To clear a Brake Pick Fault, the
parameter Brake Pick Flt Ena (C1) must be
changed from ’Active’ to ‘Enabled’.