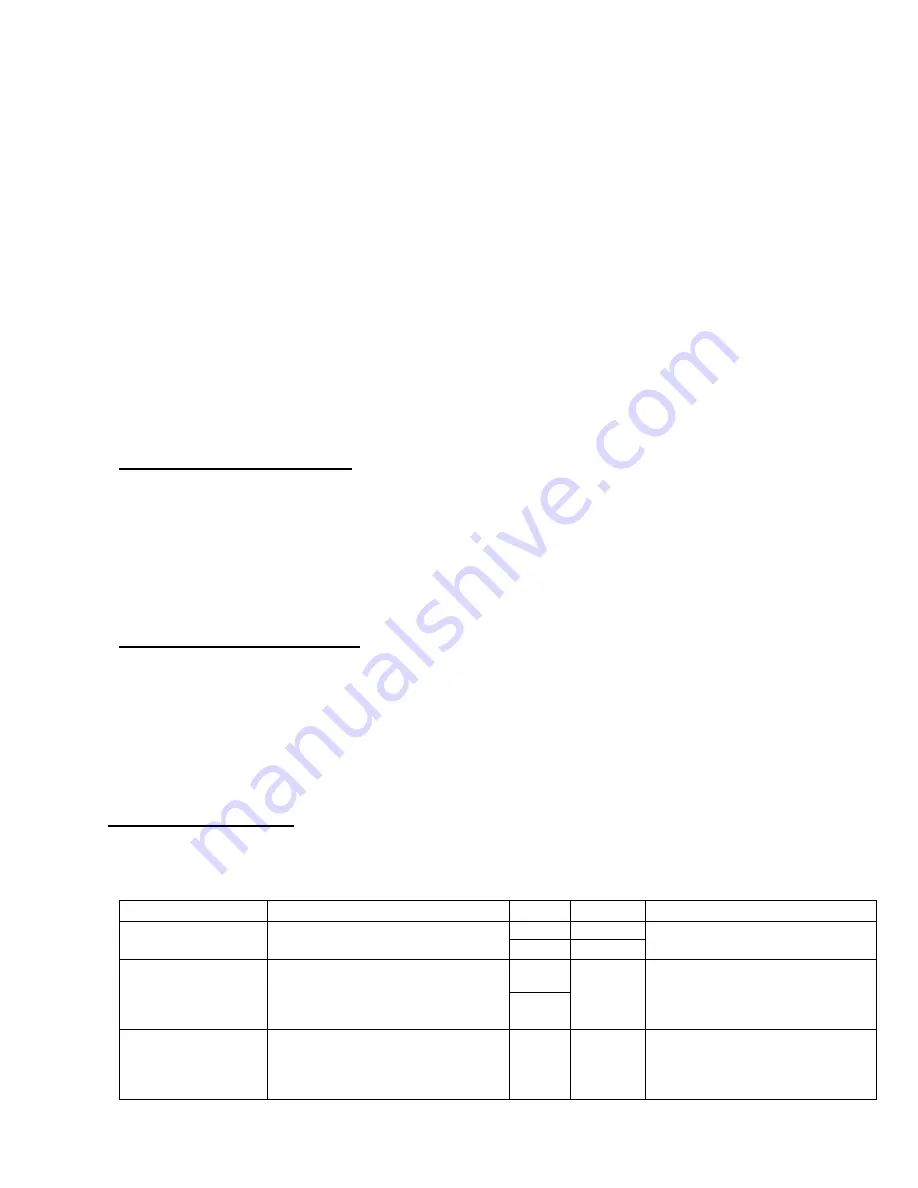
ii
Electrical Considerations
If possible, insulate both the encoder case and shaft from the motor.
Use twisted pair cable with shield tied to chassis ground at drive end
Use limited slew rate differential line drivers.
Do not allow capacitors from internal encoder electronics to case.
Do not exceed the operating specification of the encoder/drive.
Use the proper encoder supply voltage and use the highest possible voltage available. (i.e.
12V
DC
is preferred because less susceptible to noise)
Mechanical Considerations
Use direct motor mounting without couplings where possible.
Use hub or hollow shaft encoder with concentric motor stub shaft.
If possible, use a mechanical protective cover for exposed encoders.
NOTE:
Refer to Encoder Mounting on page 187 for illustrations on mounting encoder
5) Enter / verify the encoder pulses entered in the ENCODER PULSES (A1) parameter matches the
encoder’s nameplate.
Hoistway Parameter Set-up
6) Enter / verify the hoistway parameters:
CONTRACT CAR SPD (A1) parameter should be the elevator contract speed in ft/min.
CONTRACT MTR SPD (A1) parameter should be set to a RPM that will make the elevator
travel at desired car speed (measured with hand tachometer).
NOTE:
The above two parameters are utilized by the drive for many purposes regarding speed
control of the lift, therefore its important these are set correctly.
Low speed inspection mode
7)
Run the drive in low speed inspection mode and…
Start with default values for INERTIA (A1) and % NO LOAD CURR (A5) parameters.
Verify encoder polarity… the motor phasing should match the encoder phasing.
If you
experience ENCODER FAULT/ HIT TRQ LIM alarm the phasing may be incorrect
-
this can be
reversed using ENCODER CONNECT(C1)
Verify proper hoistway direction…can be reversed with the MOTOR ROTATION (C1)
parameter.
Key Drive Parameters
NOTE:
Key parameters that are
not
listed below are parameters that are set for drive/controller
interface in the C0 menu and A2 and A3 sub menus
Drive Menu A1
Parameter
Description
Default
Units
Suggested Adjustment
CONTRACT CAR SPD
Elevator contract speed
400.0
fpm
Adjust to speed the installation is rated
to run at.
0.0
m/s
CONTRACT MTR SPD
Motor speed at elevator contract speed
1130.0
rpm
Adjust this value to ensure the actual
running speed of the car matches the
parameter above - If the car is traveling
too fast then reduce this value, if too
slow then increase it.
0.0
RESPONSE
Sensitivity of the speed regulator
10.0
rad/sec
Set to 20 to improve the drive response
to changes in speed reference. If the
motor current and speed becomes
unstable, reduce however if the value is
too small, the response will be sluggish.