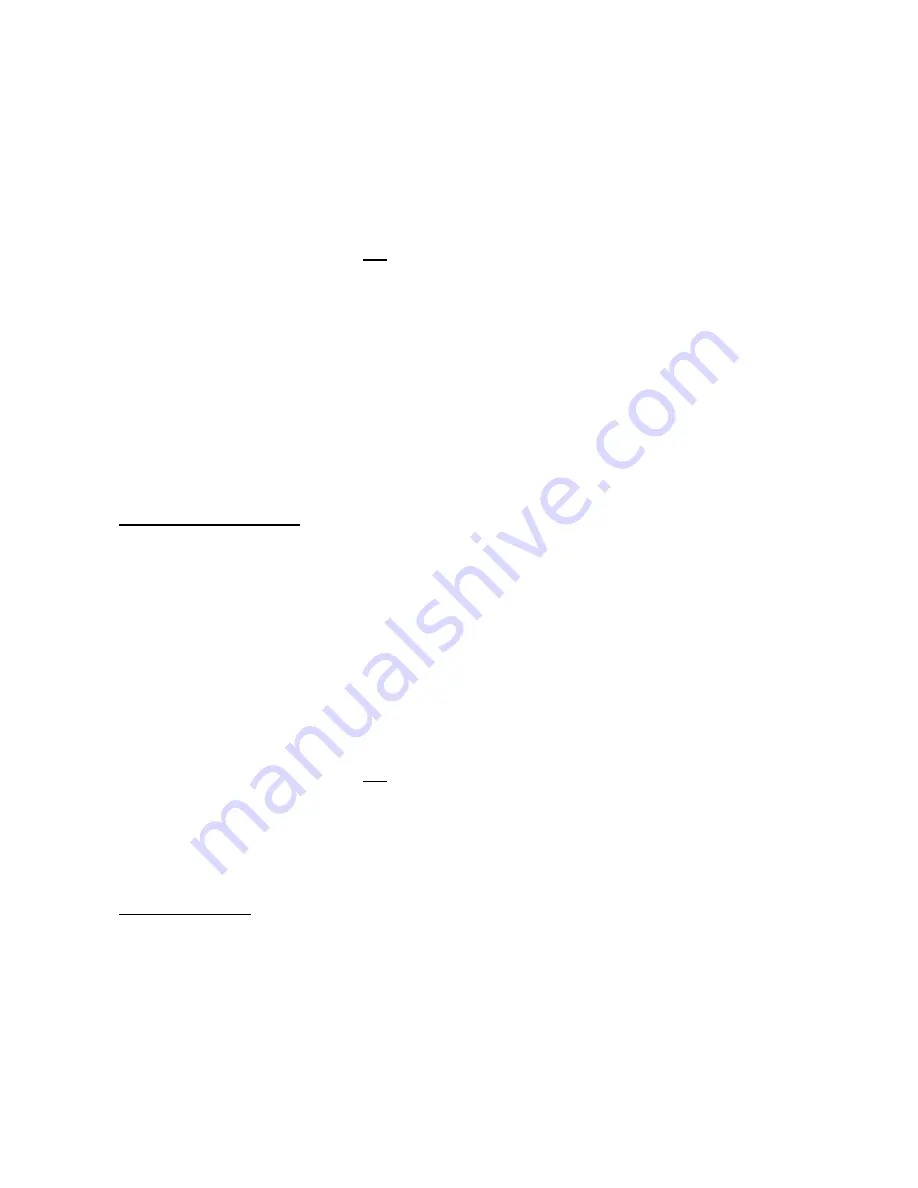
xiii
Also in the U10 alignment menu ensure the parameter ALIGNMENT METHOD is set to
HF INJECT or AUTO ALIGN
Next change the parameter BEGIN ALIGNMENT to ON RUN
The drive is now ready for alignment, so simply press and hold the RUN, RUN UP, or
RUN DOWN buttons. You should see the run LED on the drive illuminate and the motor
will ‘buzz’, the brake will
not
lift however. It will only take a couple of seconds and when
completed the RUN LED on the drives operator will extinguish and you may release your
buttons.
Assuming this went successfully the drive will have established the encoders position
relative to the motor poles, this value can be checked in the drives A5 menu (parameter
ENCODER ANG OFFST). The procedure should be run 5 times. The value should be
consistent, if not check for proper grounding. You are then able to attempt to run on
inspection control to verify.
If this procedure didn’t complete successfully and a fault was displayed, please refer to
the fault section of this supplement or the drives technical manual for diagnostic
information
Step 4
– Motor Auto Tune
7) After the encoder angle offset is obtained and as a final optimization procedure, it is possible to
gather some further motor characteristics from the motor as part of an ‘AutoTune’
In this test the A5 Parameters D AXIS INDUCTANCE, Q AXIS INDUCTANCE & STATOR
RESISTANCE are obtained and updated automatically
To perform this:
Clear any active faults in the drive in the F1 menu (and verify they have cleared)
Scroll to U12 menu
– AUTOTUNE SEL and change the parameter AUTOTUNE
SELECT to ON RUN
The drive is now ready for Auto Tune, so simply press and hold your RUN, RUN UP, or
RUN DOWN buttons. You should see the run LED on the drive illuminate and the motor
will ‘buzz’, the brake will
not
lift however. It will only take a couple of seconds and when
completed the RUN LED on the drives operator will extinguish and you may release your
buttons.
The values obtained from this Auto Tune will be automatically saved and can be viewed
in the A5 Menu
Step 5
– Fine Tune
8) Assuming the above steps have been carried out in full, on most occasions the alignment values
obtained will give near perfect alignment results, however if you observe higher than expected
motor current, vibrations or encoder relate
d trips we do have a ‘fine tune procedure’ which can be
used to either diagnose if the encoder alignment is correct or assist with correcting it if it is found
not to be correct. This procedure is rarely required, however if you do find an application where
you would like to perform it a step by step guide can be found in Fine Tune Alignment Procedure.