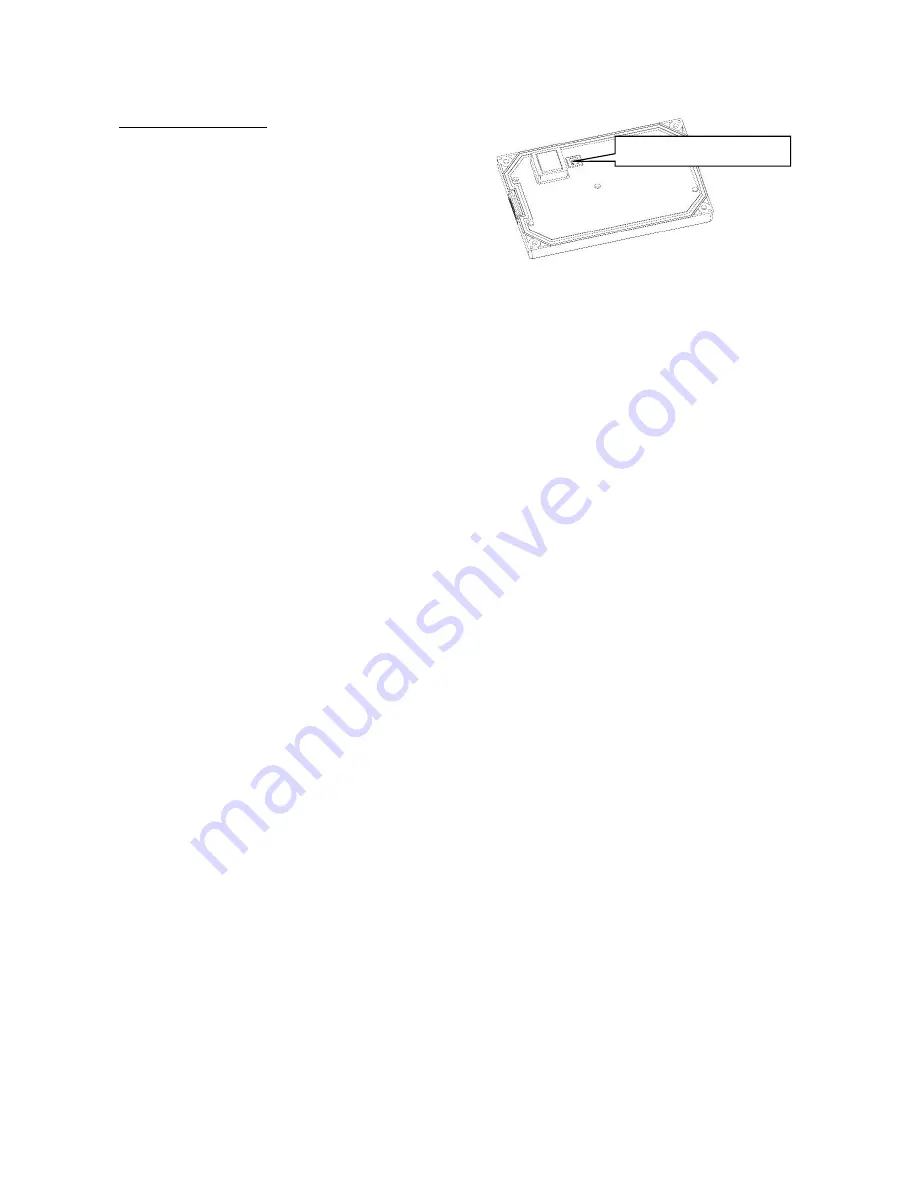
General Start-Up
18
Pre-Power Check
CAUTION
: TO PREVENT DAMAGE TO THE
DRIVE. THE FOLLOWING CHECKS MUST
BE PERFORMED BEFORE APPLYING THE
INPUT POWER.
Inspect all equipment for signs of damage,
loose connections, or other defects.
Ensure the three-phase line voltage is
within
10% of the nominal input voltage.
Also verify the frequency (50 or 60 Hz) is
correct for the elevator control system.
Remove all shipping devices.
Ensure all electrical connections are
secure.
Ensure that all transformers are connected
for proper voltage.
IMPORTANT: Double-check all the power
wires and motor wires (R, S, T, U, V, & W) to
make sure that they are securely tightened
down to their respective lugs (loose wire
connections may cause problems at any time).
IMPORTANT: Insure the incoming line supply
IS CONNECTED to the drive INPUT
TERMINALS R, S, & T and NOT to the output
motor terminals U, V, & W.
9. Insure the DC Choke link is in place, if a
DC choke is NOT used.
10. Insure a Dynamic Braking Resistor is
connected to the drive, see page 178
11. Measure and verify transformer primary
and secondary volts
12. Check for balanced Vac from phase to
ground.
13.
Verify the accuracy of the drive’s input line-
to-line voltage in parameter INPUT L-L
VOLTS (A4)
NOTE: The INPUT L-L VOLTS (A4)
parameter helps to determine the DC bus
undervoltage alarm/fault level.
Real Time Clock Setup
The HPV900 Series 2 operator comes with a
real time clock and battery. As part of the
startup, it is beneficial to the user to setup the
real time clock by following the instructions
below:
1. With power removed from the drive,
remove the operator from the drive by
unplugging the connector.
2. As seen in Figure 1, set the power switch
to “1”. Plug operator back into drive.
Figure 1: Back of Operator
3. Turn on power to the drive and set the
following parameters in the Time, U11
submenu:
Year
Month
Day
Hour (use 24 hour clock)
Minute
Second
4. These number(s) / date(s) will be
automatically stored, however, after setting
these value in the U11 submenu, it may be
viewed on the top of the display or logged
into fault history when a fault occurs and
the U11 parameter will reset back to zero.
This completes the recommended general
start-up procedure. For Close-Loop Adaptive
Tune procedure, please see page 152.
CSA Warnings
The following are written warnings located on
the drive chassis. They appear in both English
and French. In this section, these warnings
appear in English only.
Caution
—Risk of Electric Shock:
Capacitive voltages above 50V may
remain for 5 minutes after power is
disconnected
Caution
—Risk of Electric Shock: More
than one live circuit: See diagram
The following written warning is also located
on the drive chassis.
This device provides motor overload
protection in accordance with NEC and
CEC requirements. This device is
factory configured to stop the motor
from a motor overload trip. See
instruction manual for options.
WARNING: Separate Motor Overcurrent
Protection is required to be provided in
accordance with the Canadian Electrical Code,
Part 1, and NEC.
Operator power switch