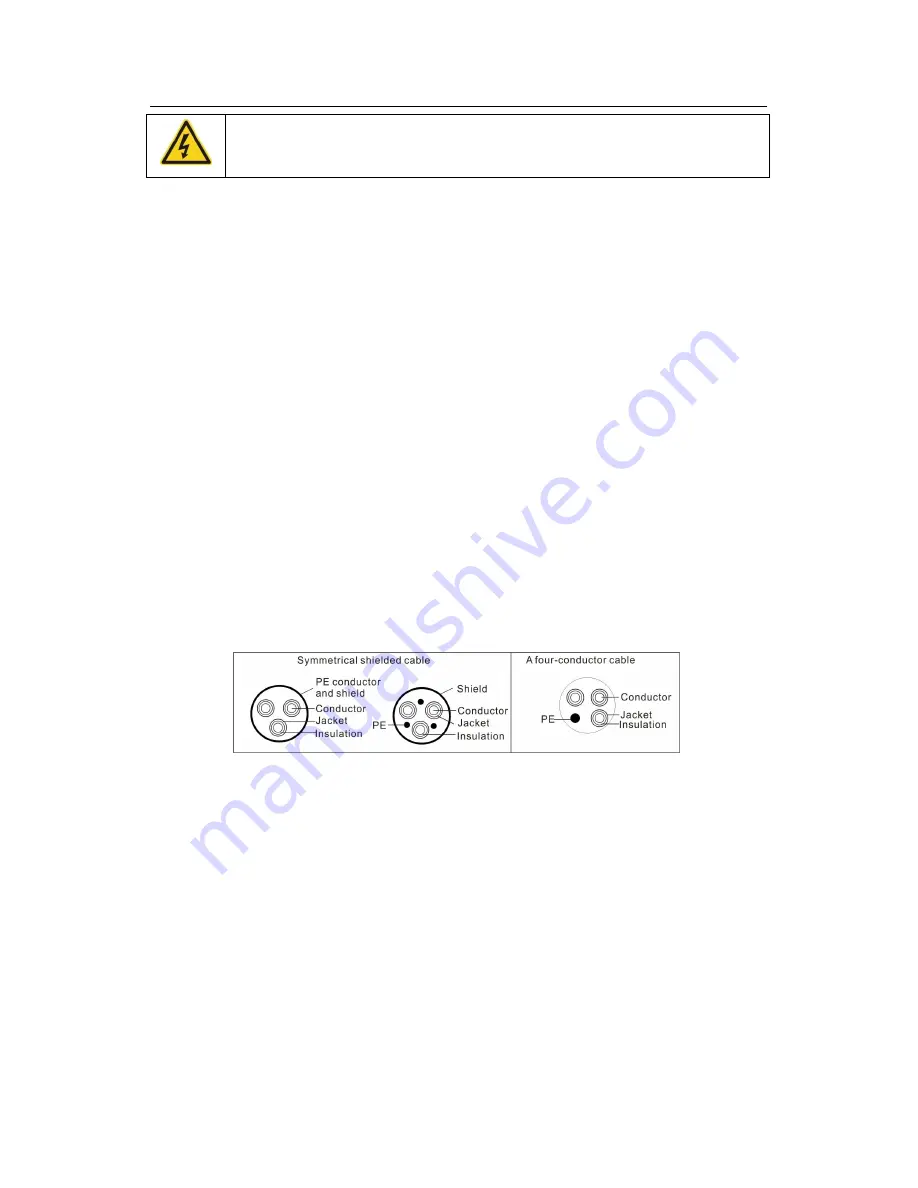
Goodrive200 inverters Appendix C
251
Check that the voltage degree of the inverter complies with the voltage
of the supply power voltage.
C.4 Cables
C.4.1 Power cables
Dimension the input power and motor cables according to local regulations.
•
The input power and the motor cables must be able to carry the corresponding load
currents.
•
The cable must be rated for at least 70 °C maximum permissible temperature of the
conductor in continuous use.
•
The conductivity of the PE conductor must be equal to that of the phase conductor
(same cross-sectional area).
•
Refer to chapter
Technical Data
for the EMC requirements.
A symmetrical shielded motor cable (see the figure below) must be used to meet the EMC
requirements of the CE.
A four-conductor system is allowed for input cabling, but a shielded symmetrical cable is
recommended. Compared to a four-conductor system, the use of a symmetrical shielded
cable reduces electromagnetic emission of the whole drive system as well as motor bearing
currents and wear.
Note:
A separate PE conductor is required if the conductivity of the cable shield is not
sufficient for the purpose.
To function as a protective conductor, the shield must have the same cross-sectional area as
the phase conductors when they are made of the same metal.
To effectively suppress radiated and conducted radio-frequency emissions, the shield
conductivity must be at least 1/10 of the phase conductor conductivity. The requirements are
easily met with a copper or aluminum shield. The minimum requirement of the motor cable
shield of the drive is shown below. It consists of a concentric layer of copper wires. The
better and tighter the shield, the lower the emission level and bearing currents.
Summary of Contents for GD200-037G/045P-4
Page 1: ...Goodrive 200 Inverter ...
Page 44: ...Goodrive200 inverters Keypad operation procedure 43 Fig 5 5 Sketch map of state watching ...
Page 158: ...Goodrive200 inverters Basic operation instruction 157 ...
Page 208: ...Goodrive200 inverters Fault tracking 207 8 6 2 Motor vibration 8 6 3 Overvoltage ...
Page 209: ...Goodrive200 inverters Fault tracking 208 8 6 4 Undervoltage fault 8 6 5 Inverter overheating ...
Page 210: ...Goodrive200 inverters Fault tracking 209 8 6 6 Abnormal motor heat ...
Page 211: ...Goodrive200 inverters Fault tracking 210 8 6 7 Stall during the acceleration of the motor ...
Page 266: ...1 1 0 0 1 0 0 7 7 9 6 6 0 0 1 0 0 0 9 5 201701 V2 2 ...