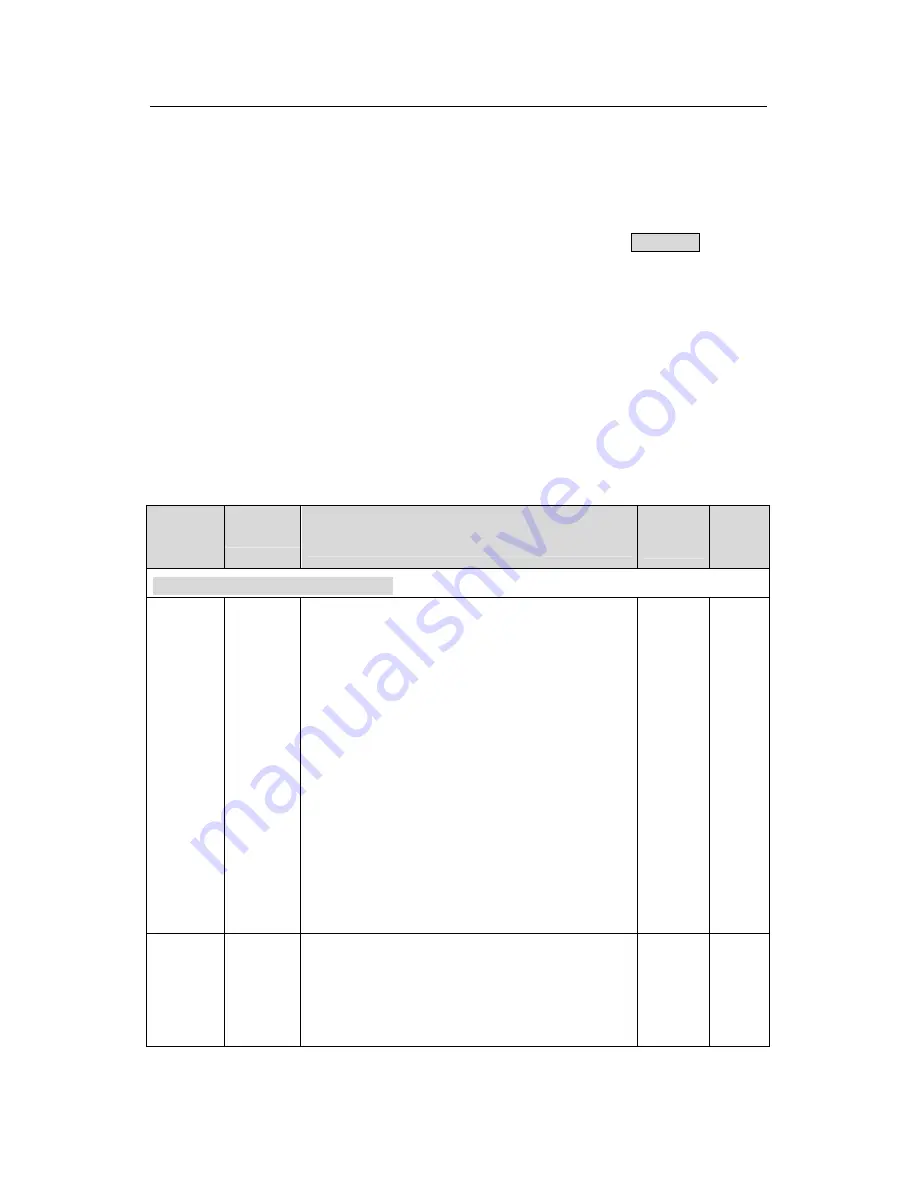
Goodrive200 inverters Function codes
45
default parameters restoring. But the detected parameter or recorded value won’t be
restored.
4.
For a better parameter protection, the inverter provides password protection to the
parameters. After setting the password (set P07.00 to any non-zero number), the system will
come into the state of password verification firstly after the user press PRG/ESC to come
into the function code editing state. And then “0.0.0.0.0.” will be displayed. Unless the user
input right password, they cannot enter into the system. For the factory setting parameter
zone, it needs correct factory password (remind that the users can not modify the factory
parameters by themselves, otherwise, if the parameter setting is incorrect, damage to the
inverter may occur). If the password protection is unlocked, the user can modify the
password freely and the inverter will work as the last setting one. When P07.00 is set to 0,
the password can be canceled. If P07.00 is not 0 during powering on, then the parameter is
protected by the password. When modify the parameters by serial communication, the
function of the password follows the above rules, too.
Function
code
Name
Detailed instruction of parameters
Default
value
Modify
P00 Group Basic function group
P00.00
Speed
control
mode
1: Sensorless vector control mode 1 (applying to
AM)
No need to install encoders. It is suitable in cases
with high speed control accuracy for accurate
speed and torque control at all power ratings.
2:SVPWM control
No need to install encoders. It can improve the
control accuracy with the advantages of stable
operation, valid low-frequency torque boost and
current vibration suppression and the functions of
slip compensation and voltage adjustment.
Note
: AM-Asynchronous motor
2
◎
P00.01
Run
command
channel
Select the run command channel of the inverter.
The control command of the inverter includes:
start-up, stop, forward, reverse, jogging and fault
reset.
0
○
Summary of Contents for GD200-037G/045P-4
Page 1: ...Goodrive 200 Inverter ...
Page 44: ...Goodrive200 inverters Keypad operation procedure 43 Fig 5 5 Sketch map of state watching ...
Page 158: ...Goodrive200 inverters Basic operation instruction 157 ...
Page 208: ...Goodrive200 inverters Fault tracking 207 8 6 2 Motor vibration 8 6 3 Overvoltage ...
Page 209: ...Goodrive200 inverters Fault tracking 208 8 6 4 Undervoltage fault 8 6 5 Inverter overheating ...
Page 210: ...Goodrive200 inverters Fault tracking 209 8 6 6 Abnormal motor heat ...
Page 211: ...Goodrive200 inverters Fault tracking 210 8 6 7 Stall during the acceleration of the motor ...
Page 266: ...1 1 0 0 1 0 0 7 7 9 6 6 0 0 1 0 0 0 9 5 201701 V2 2 ...