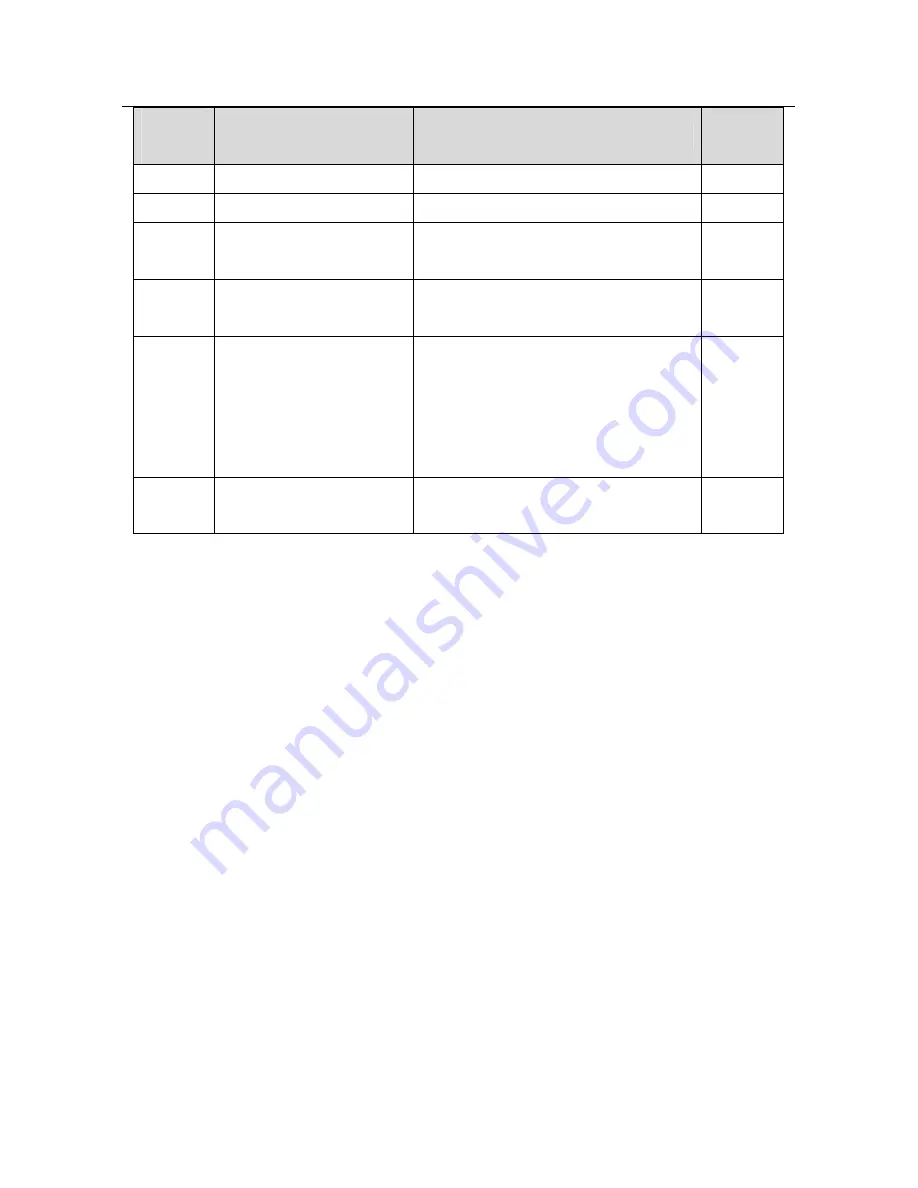
Goodrive200
inverters Basic operation instruction
186
Function
code
Name
Detailed instruction of parameters
Default
value
P10.32
Multi-step speed 15
-100.0~100.0%
0.0%
P10.33
The running time of step 15 0.0~6553.5s(min)
0.0s
P10.34
Simple PLC 0~7 step
ACC/DEC time
0x0000~0XFFFF
0000
P10.35
Simple PLC 8~15 step
ACC/DEC time
0x0000~0XFFFF
0000
P05.01~
P05.09
Digital input function
selection
16:Multi-step speed terminal 1
17:Multi-step speed terminal 2
18:Multi-step speed terminal 3
19:Multi- step speed terminal 4
20:Multi- step speed pause
P17.27
Simple PLC and the current
step of the multi-step speed
7.15 PID control
PID control is commonly used to control the procedure. Adjust the output frequency by proportional,
integral, differential operation with the dispersion of the target signals to stabilize the value on the
target. It is possible to apply to the flow, pressure and temperature control. Figure of basic control
is as below:
Summary of Contents for GD200-037G/045P-4
Page 1: ...Goodrive 200 Inverter ...
Page 44: ...Goodrive200 inverters Keypad operation procedure 43 Fig 5 5 Sketch map of state watching ...
Page 158: ...Goodrive200 inverters Basic operation instruction 157 ...
Page 208: ...Goodrive200 inverters Fault tracking 207 8 6 2 Motor vibration 8 6 3 Overvoltage ...
Page 209: ...Goodrive200 inverters Fault tracking 208 8 6 4 Undervoltage fault 8 6 5 Inverter overheating ...
Page 210: ...Goodrive200 inverters Fault tracking 209 8 6 6 Abnormal motor heat ...
Page 211: ...Goodrive200 inverters Fault tracking 210 8 6 7 Stall during the acceleration of the motor ...
Page 266: ...1 1 0 0 1 0 0 7 7 9 6 6 0 0 1 0 0 0 9 5 201701 V2 2 ...