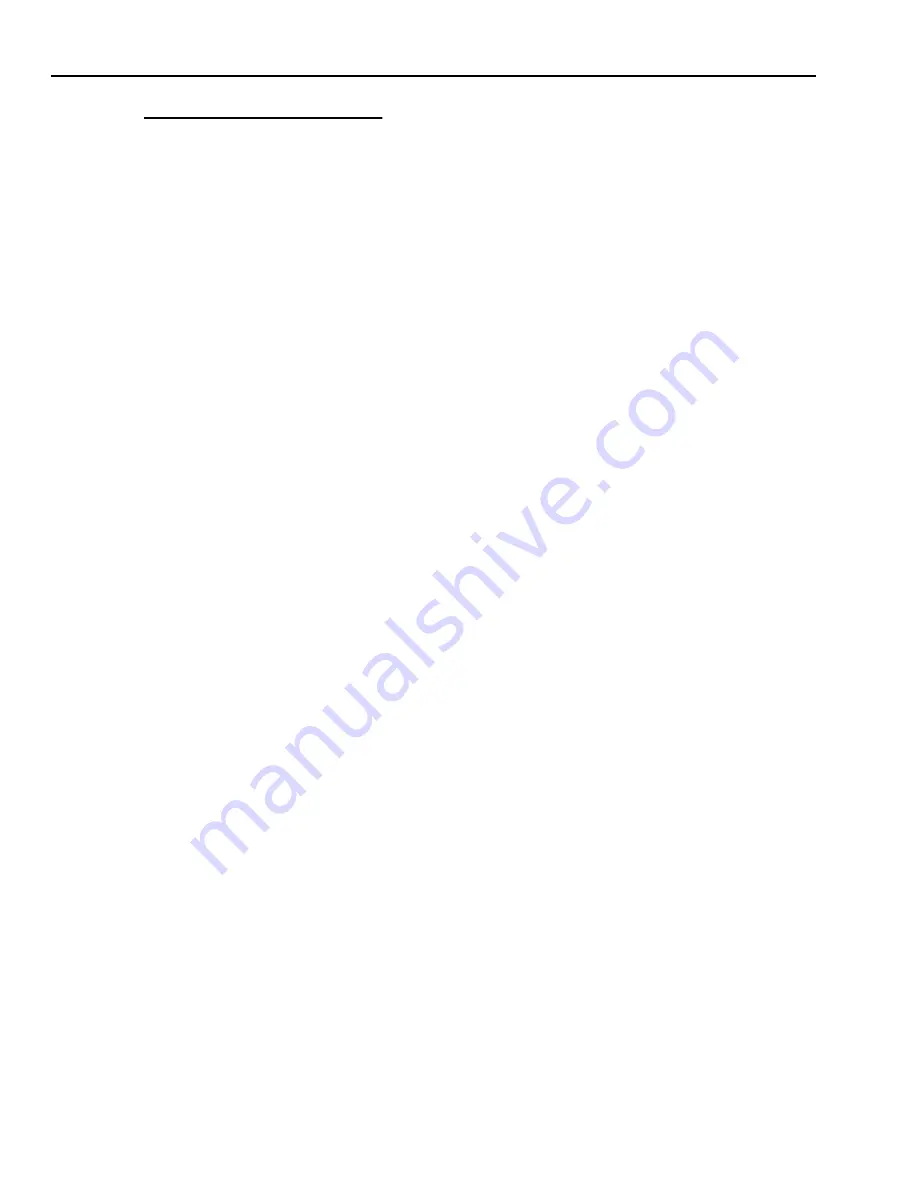
ENGINEERING MANUAL OF AUTOMATIC CONTROL
CHILLER, BOILER, AND DISTRIBUTION SYSTEM CONTROL APPLICATIONS
360
Where:
BHP = Horsepower
∆
T = Low flow water temperature rise across the
pump
The minimum flow for 10 horsepower with a 10 degree
∆
T
(attributed to the pump heating the water) is only 5 gpm. The
bypass may be fixed or if there is a remote AHU in the 12 to 25
gpm size, using a three-way valve on that AHU with the bypass
in the bypass leg of the three-way valve prevents bypass water
from flowing during full-load periods. Another option is an
automatic bypass valve programmed to open anytime all AHU
control valves are less than 10% open.
Decoupled Variable Speed Pump Control,
Reverse Return
In these examples, the design differential pressure for all AHUs
is 16 ft with reverse return, since the balancing-valve drop becomes
negligible. If approximately 18 ft is maintained at AHU 1, design
flow is available to all AHUs during any non-symmetrical flow
condition. With a reverse return system locate the differential
pressure sensor across AHU 1 with a setpoint of 18 ft. Advantages
of valve position load reset are much less with reverse return
systems, however, resetting the setpoint from 18 ft to 8 or 10 ft
based upon load is worthwhile on large systems.
HOT WATER DISTRIBUTION SYSTEMS
GENERAL
Advantages of hot water compared to steam for heat
distribution within commercial buildings are:
— Water temperature can be varied to suit variable loads.
— Hot water boilers typically do not require a licensed
operating engineer.
— Heat loss from piping is less than steam systems because
fluid temperatures are usually lower.
— Temperature control is easier and more stable because
water temperature is matched to the load.
— Fewer piping accessories to maintain than steam systems.
— Reduced air stratification at light loads with reset hot water.
The control objectives for a hot water distribution system
providing space heating are:
1. Provide adequate hot water flow to all heating units.
2. Maintain a stable pressure difference between supply and
return mains at all load conditions.
3. Match hot water temperature to the heating load based
on outdoor air temperature and/or occupancy.
a. Avoid heat exchanger flow velocities dropping into
the laminar range.
b. Keep water velocities up to prevent freezing.
c. Reduce mixed air temperature stratification.
– No stratified cold air to trip low temperature
controllers or cause freeze-up.
– Minimizes stratified air from having adverse
effects on coil discharge temperature sensing.
– Minimizes possibilities of hot air flowing out
some duct outlets and cold air flowing out others.
Refer to METHODS OF CONTROLLING DISTRIBUTION
SYSTEMS for additional information on control objectives.
HOT WATER CONVERTERS
A hot water converter uses either hot water or steam to raise
the temperature of heating system water to a temperature which
satisfies the heating requirements of the system. The most
widely used hot water converters use steam.
Steam is often supplied to remote buildings or mechanical
rooms from a central plant. Within the buildings or zones, hot
water is often preferred because of its ease of control. Steam to
water converters are used for these applications.
A converter consists of a shell and tubes. The water to be
heated passes through the tubes. Steam or hot water circulates
in the shell around the tubes. Heat transfers from the steam or
hot water in the shell to the heating system water in the tubes.
If the pressure on the water in a converter drops below the
vaporization pressure for the temperature of the water, the water
can flash to steam. Pumps are usually located on the return
side of the converter to provide a positive pressure and
minimize flashing.
Figures 83 and 84 show commonly used controls for hot water
converters. See HOT WATER RESET for converter control.
=
BHP x 0.746 kW/bhp x 3
,412 Btu/kW
8.33 lb/gal x 60 min/hr x
∆
T
Minimum
flow (gpm)
Summary of Contents for AUTOMATIC CONTROL
Page 4: ...ENGINEERING MANUAL OF AUTOMATIC CONTROL iv ...
Page 6: ...ENGINEERING MANUAL OF AUTOMATIC CONTROL vi ...
Page 11: ...ENGINEERING MANUAL OF AUTOMATIC CONTROL CONTROL FUNDAMENTALS 1 CONTROL SYSTEMS FUNDMENTALS ...
Page 12: ......
Page 46: ...ENGINEERING MANUAL OF AUTOMATIC CONTROL CONTROL FUNDAMENTALS 36 ...
Page 66: ...PSYCHROMETRIC CHART FUNDAMENTALS 56 ENGINEERING MANUAL OF AUTOMATIC CONTROL ...
Page 128: ...ENGINEERING MANUAL OF AUTOMATION CONTROL ELECTRIC CONTROL FUNDAMENTALS 118 ...
Page 158: ...MICROPROCESSOR BASED DDC FUNDAMENTALS 148 ENGINEERING MANUAL OF AUTOMATIC CONTROL ...
Page 210: ...ENGINEERING MANUAL OF AUTOMATIC CONTROL BUILDING MANAGEMENT SYSTEM FUNDAMENTALS 200 ...
Page 440: ...ENGINEERING MANULA OF AUTOMATIC CONTROL INDIVIDUAL ROOM CONTROL APPLICATIONS 430 ...
Page 516: ...ENGINEERING MANUAL OF AUTOMATIC CONTROL GENERAL ENGINEERING DATA 506 Notes ...
Page 517: ...ENGINEERING MANUAL OF AUTOMATIC CONTROL GENERAL ENGINEERING DATA 507 Notes ...
Page 518: ...ENGINEERING MANUAL OF AUTOMATIC CONTROL GENERAL ENGINEERING DATA 508 ...