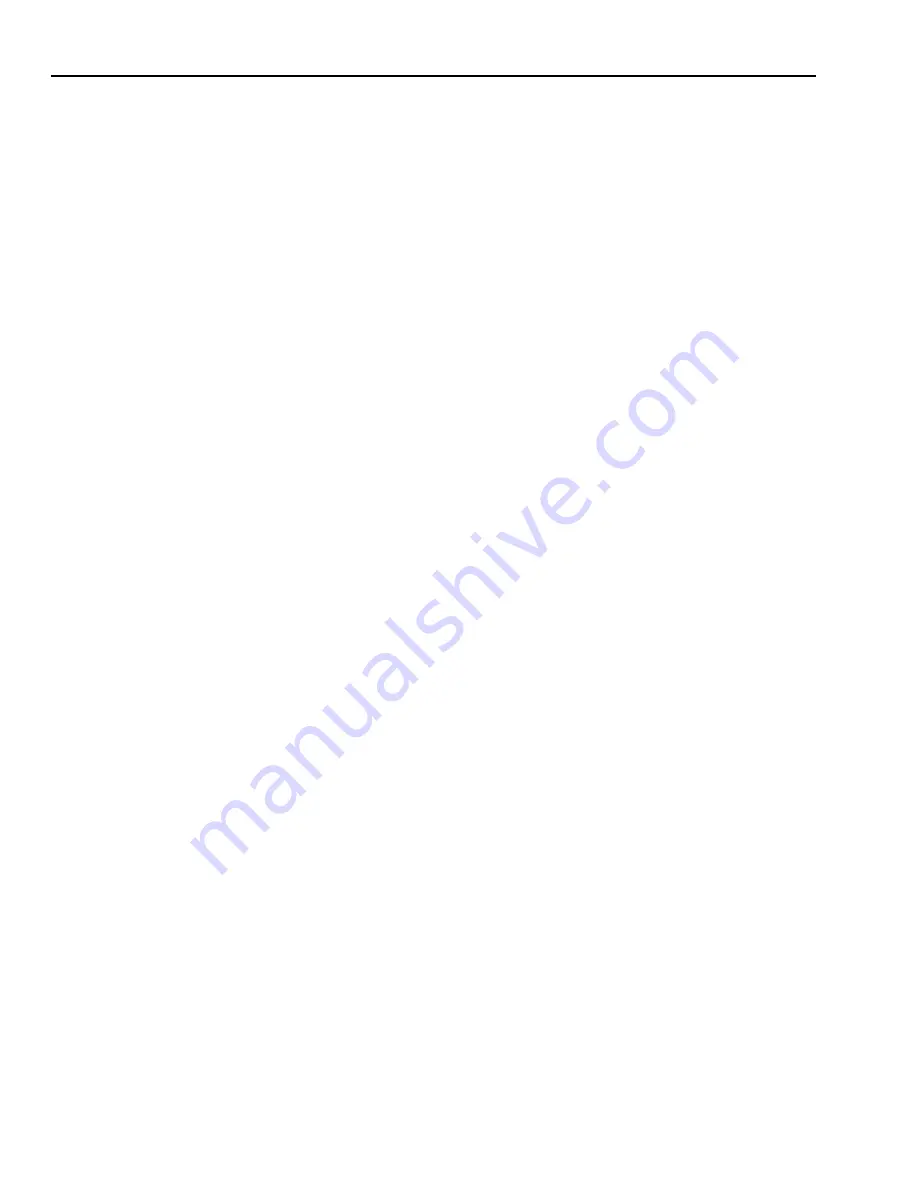
MICROPROCESSOR-BASED/DDC FUNDAMENTALS
140
ENGINEERING MANUAL OF AUTOMATIC CONTROL
Without knowledge of the actual instantaneous demands of
the loads that load reset controls, systems must run at the
theoretical worst-case setpoints for temperature and pressure.
As with most powerful application programs, load reset
requires a great depth of knowledge of the HVAC and control
process. The problem is that if load demands indicate that a
higher chilled water temperature would be appropriate and the
temperature increase is made, all loads are upset because of
the chilled water temperature change. The loads must adjust
and stabilize before another load reset adjustment is made.
Monitoring and tuning is required to assure high performance
control and loop stability. Three parameters determine the
performance and stability of the system: the magnitude of the
incremental corrections, the time interval between correction,
and the magnitude of the hysteresis between raising and
lowering the temperature.
Sun, weather, and occupancy (building utilization) dictate
load reset demands. The sun and weather effects are relatively
slow and occur as the sun and seasons change. Occupancy
changes are abrupt and occur over brief periods of time.
If a chiller plant with 44F design chilled water temperature
is controlled to increase chilled water temperature any time
all control valves are less than 80 percent open. Two air
handling units with different control sequences are compared.
1. Control valves are on a VAV AHU chilled water coil and
are part of a 55F discharge air temperature control loop.
The load reset sequence events are:
a. The most demanding AHU valve closes to below
80 percent open.
b. The load reset program raises the chilled water
temperature setpoint.
c. The chiller unloads to maintain the raised
setpoint.
d. As the chilled water temperature increases, the
discharge air temperature increases.
e. The discharge air temperature controls open the
AHU valves to maintain the discharge air
temperature setpoint.
f. The most demanding AHU valve opens to
greater than 80 percent but less than 95 percent.
g. The other AHU valves open increasing the
chiller load.
h. The two temperature loops stabilize in time. The
chiller loop is usually set for a fast response and
the discharge air loop is set for a slow response.
2. Control valves are on single zone AHU chilled water
coil, controlled from space temperature at 76F.
a. The most demanding AHU valve closes to below
80 percent open.
b. The load reset program raises the chilled water
temperature setpoint.
c. The chiller unloads to maintain the raised
setpoint.
d. As the chilled water temperature increases, the
discharge air temperature increases.
e. The space temperature control opens the valves
to maintain the space temperature setpoint. This
response takes several minutes in space
temperature control.
f. The most demanding AHU valve opens to
greater than 80 percent but less than 95 percent.
g. The other AHU valves open increasing the
chiller load.
h. The two temperature loops stabilize in time. The
chiller loop is usually set for a fast response and
the discharge air loop is set for a slow response.
The events of the first scenario occur within seconds because
both loops (leaving water temperature controlling the chiller
load and discharge air temperature controlling chilled water
flow) are close coupled and fast. Because the two loops oppose
each other (a chilled water temperature rise causes discharge
air temperature to rise which demands more chilled water flow),
a few minutes must be allowed for system stabilization. The
chilled water temperature control loop should be fast and keep
the chilled water near the new setpoint while the AHU
temperature loops slowly adjust to the new temperature.
Hysteresis is a critical load reset parameter. Water
temperature is raised if all valves are less than 80 percent open
but, is not lowered until one valve is greater than 95 percent
open. This 15 percent dead band allows lengthy periods of
stability between load reset increases and decreases. Properly
tuned load reset programs do not reverse the commands more
than once or twice a day.
Scenario 1 initial parameters could be; command chilled
water temperature increments of 0.3F, a load reset program
execution interval of 4.0 minutes, a decrement threshold of
80 percent, (most demanding valve percent open), an increment
threshold of 95 percent (most demanding valve percent open),
a start-up chilled water temperature setpoint of 45F, a maximum
chilled water temperature setpoint of 51F, and a minimum
chilled water temperature setpoint of 44F. The load reset chilled
water temperature program may include an AUTO-MANUAL
software selector and a manual chilled water temperature
setpoint for use in the manual mode.
Unlike scenario 1, the events within scenario 2 occur over
several minutes (not seconds) because when the chilled water
temperature setpoint is raised, it takes several minutes for the
water temperature rise and the resulting air temperature
increase to be fully sensed by the space temperature sensor.
Scenario 2 parameters could be the same as scenario 1 with
the exception of the execution interval which should be about
15 minutes.
All parameters should be clearly presented and easily
commandable. Figure 10 is an example of dynamic data display
for scenario 1.
Summary of Contents for AUTOMATIC CONTROL
Page 4: ...ENGINEERING MANUAL OF AUTOMATIC CONTROL iv ...
Page 6: ...ENGINEERING MANUAL OF AUTOMATIC CONTROL vi ...
Page 11: ...ENGINEERING MANUAL OF AUTOMATIC CONTROL CONTROL FUNDAMENTALS 1 CONTROL SYSTEMS FUNDMENTALS ...
Page 12: ......
Page 46: ...ENGINEERING MANUAL OF AUTOMATIC CONTROL CONTROL FUNDAMENTALS 36 ...
Page 66: ...PSYCHROMETRIC CHART FUNDAMENTALS 56 ENGINEERING MANUAL OF AUTOMATIC CONTROL ...
Page 128: ...ENGINEERING MANUAL OF AUTOMATION CONTROL ELECTRIC CONTROL FUNDAMENTALS 118 ...
Page 158: ...MICROPROCESSOR BASED DDC FUNDAMENTALS 148 ENGINEERING MANUAL OF AUTOMATIC CONTROL ...
Page 210: ...ENGINEERING MANUAL OF AUTOMATIC CONTROL BUILDING MANAGEMENT SYSTEM FUNDAMENTALS 200 ...
Page 440: ...ENGINEERING MANULA OF AUTOMATIC CONTROL INDIVIDUAL ROOM CONTROL APPLICATIONS 430 ...
Page 516: ...ENGINEERING MANUAL OF AUTOMATIC CONTROL GENERAL ENGINEERING DATA 506 Notes ...
Page 517: ...ENGINEERING MANUAL OF AUTOMATIC CONTROL GENERAL ENGINEERING DATA 507 Notes ...
Page 518: ...ENGINEERING MANUAL OF AUTOMATIC CONTROL GENERAL ENGINEERING DATA 508 ...