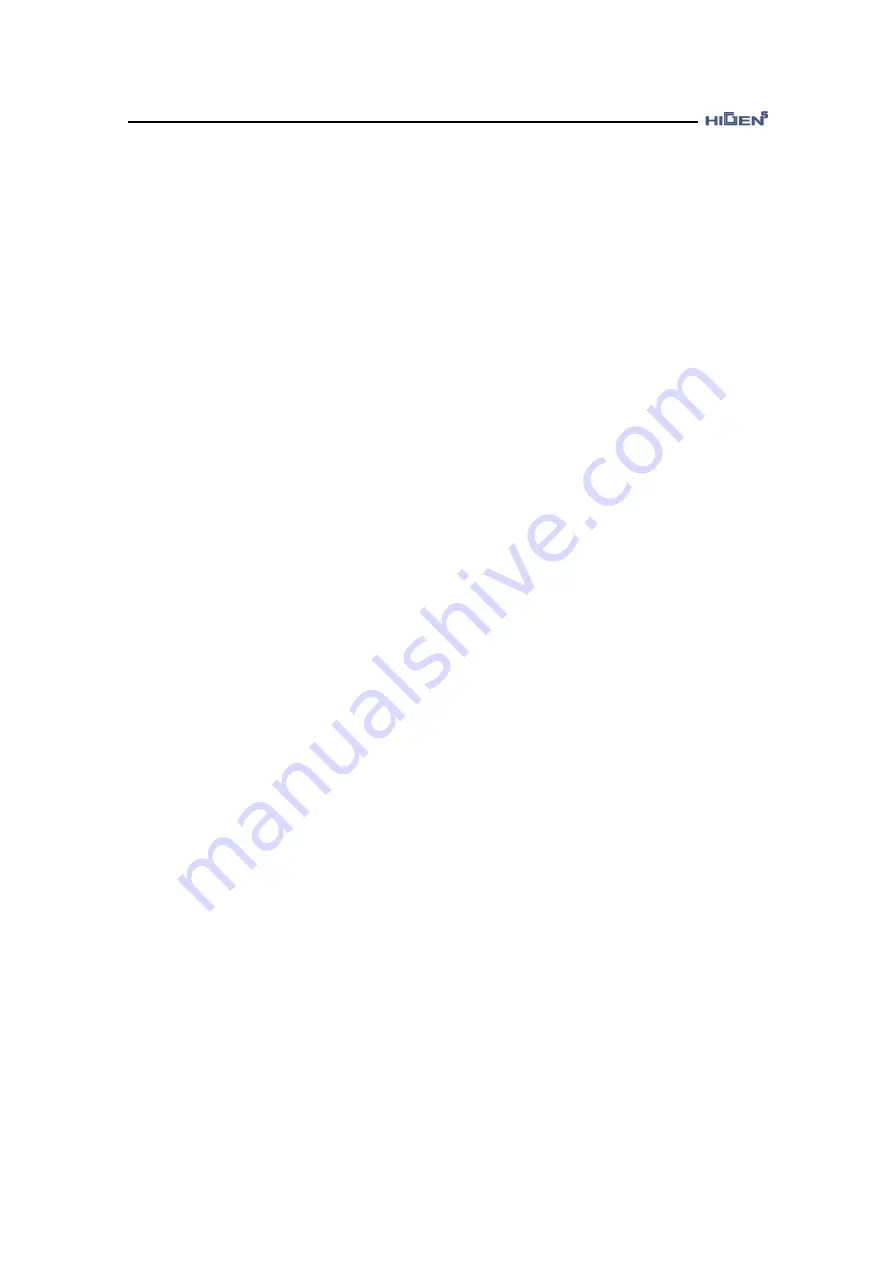
Appendix
Ⅱ
. Noise control
Ⅱ
-1
II.1.
Wiring Precautions
The FDA7000 servo drive uses high-speed switching in the main circuit. It may receive
switching noise from these high-speed switching elements if wiring or grounding around the
servo drive is not correct. To protect the servo drive system from the external noise install the
noise filter in appropriate place as much as possible. To ensure safe and suitable operation, keep
the following precautions.
①
For wiring for reference inputs and encoders, use the specified cables.
-
Use the cables as short as possible.
②
For ground wire, as thick a cable as possible.
-
At least class - 3 ground (100Ω max.) is recommended.
-
Ground to one point common only.
③
Do not bend or apply tension to cables.
④
Use a noise filter to prevent noise interference. FDA7000 is designed as an industrial device,
it provides no mechanism to prevent noise interference.
⑤
To prevent malfunction due to the noise, take the following actions.
-
Location the input reference device and noise filter as close to the servo drive as
possible.
-
Install s surge protector in the relay, solenoid and electromagnetic contactor coils.
-
The distance between a power line and s signal line must be at least 30 cm.
-
Do not put the power line and signal line in the same duct or bundle then together.
-
Do not share the power supply with an electric welding machine or electrical discharge
machine. When the servo drive in placed near a high frequency generator, install a noise
filter and isolation transformer on the input side of the power supply line.
II.2.
Wiring for noise control
Always connect servo motor FG terminal to the drive frame ground terminal. If the servo motor
is grounded via the machine, a switching noise current from the drive power unit through servo
motor stray capacitance. The above grounding in required to prevent the adverse effects of the
switching noise.
Summary of Contents for FDA7000 Series
Page 42: ...1 Model check and handling 1 35...
Page 57: ...2 Wiring and connection 2 14 Drawing C Order Code Please contact our sales office...
Page 130: ...3 Parameter setting 3 51...
Page 167: ...5 Servo operating 5 10...
Page 188: ...8 External view 8 2 External view B CN1 CN3 CN2 External view C...
Page 189: ...8 External view 8 3 External view D External view E...
Page 190: ...8 External view 8 4 External view F External view G...
Page 192: ...8 External view 8 6 External view I External view J...
Page 193: ...8 External view 8 7 External view K External view L...
Page 194: ...8 External view 8 8 External view M...
Page 195: ...8 External view 8 9...