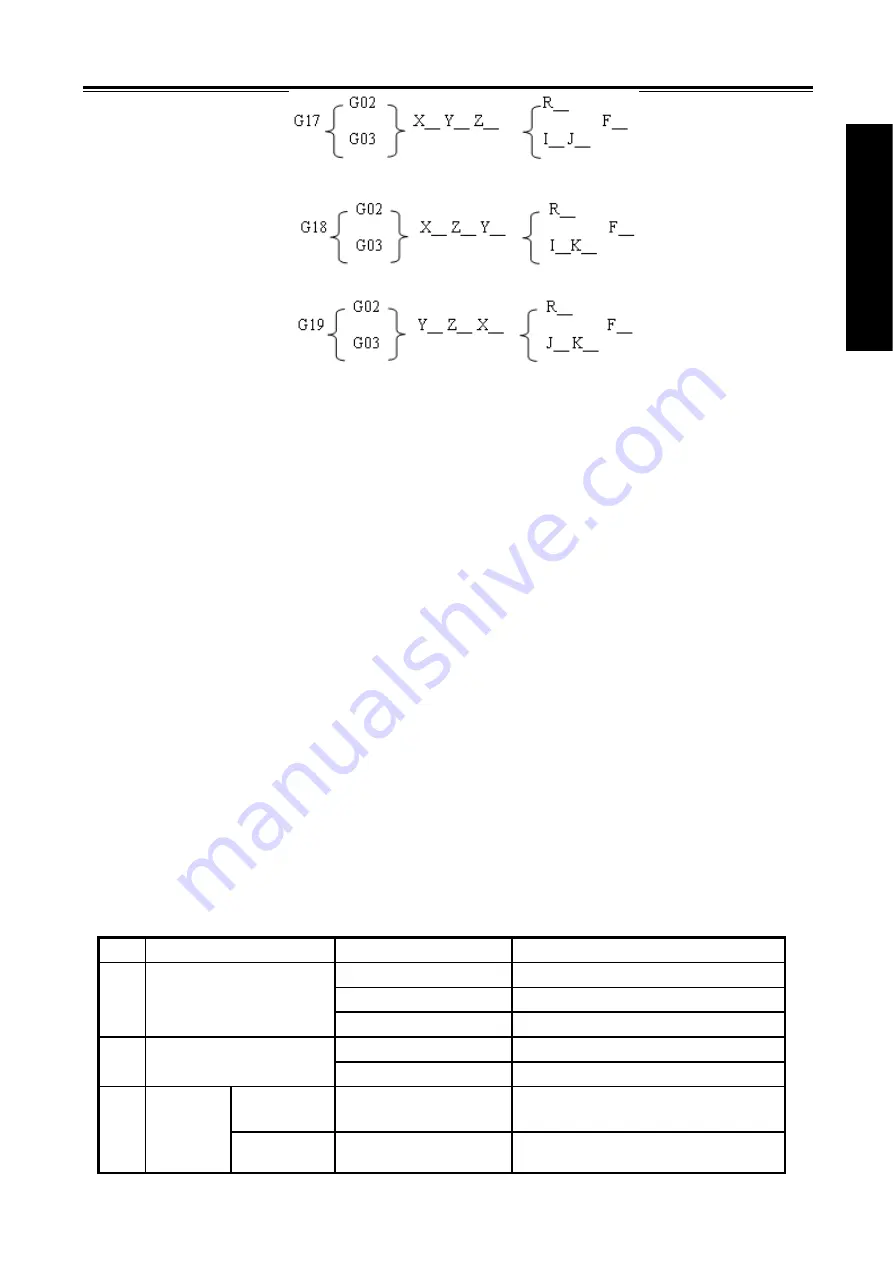
Chapter 3 G Command
33
I Programming
Arc interpolation in XZ plane, Y axis linear interpolation linkage;
Arc interpolation in YZ plane, X axis linear interpolation linkage;
Function:
Only two axes of circular interpolation can be linked for controlling tool movement along with the
arc on the selected plane in any time. If the 3rd axis is specified simultaneously in linear
interpolation mode, it will be linked by linear interpolation type to constitute helical interpolation.
G02 movement path is CW from start to end points. G03 movement path is CCW from start to
end points.
Explanation:
G02 and G03 are modal G commands;
R is an arc radius, its value
:
-99999999
~
99999999×least input increment
;
When the circle center is specified by address I, J and K, they are corresponding with the X, Y and Z
axes separately.
I is the difference between the center point and the arc start point in the X axis direction, I= center
point coordinate X- X coordinate of arc start point; its value
:
-99999999
~
99999999×least input
increment;
J is the difference between the center point and the arc start point in the Y axis direction, J=center
point coordinate Y- Y coordinate of circle arc start point; its value
:
-99999999
~
99999999×least input increment ;
K is the difference between the center point and circle start point in the Z axis direction, K=center
point coordinate Z- Z coordinate of circle start point; its value
:
-99999999
~
99999999×least input
increment.
Note
:
When I, J and K are for whole-circle that they have signs according to the direction. And they are positive
values when I, J and K share the same directions with X, Y and Z axes; otherwise they are negative ones.
Item
Specified content
Command
Meaning
G17
Specifying XY plane arc
G18
Specifying ZX plane arc
1 Plane
specification
G19
Specifying YZ plane arc
G02 CW
2 Rotating
direction
G03 CCW
G90 mode Two axes of X, Y and Z
End point in the part
coordinate system
3 End
point
G91 mode Two axes of X, Y and Z
Distance from start to end points
Summary of Contents for 980MDc
Page 19: ...GSK980MDc Milling CNC User Manual XVIII ...
Page 20: ...1 I Programming Programming Ⅰ ...
Page 21: ...GSK980MDc Milling CNC System User Manual 2 I Programming ...
Page 139: ...GSK980MDc Milling CNC System User Manual 120 I Programming ...
Page 191: ...GSK980MDc Milling CNC System User Manual 172 I Programming ...
Page 192: ...173 Ⅱ Operation Ⅱ Operation ...
Page 193: ...GSK980MDc Milling CNC System User Manual 174 Ⅱ Operation ...
Page 200: ...Chapter 1 Operation Mode and Display 181 Ⅱ Operation ...
Page 201: ...GSK980MDc Milling CNC System User Manual 182 Ⅱ Operation ...
Page 249: ...GSK980MDc Milling CNC System User Manual 230 Ⅱ Operation ...
Page 253: ...GSK980MDc Milling CNC System User Manual 234 Ⅱ Operation ...
Page 259: ...GSK980MDc Milling CNC System User Manual 240 Ⅱ Operation ...
Page 265: ...GSK980MDc Milling CNC System User Manual 246 Ⅱ Operation ...
Page 293: ...GSK980MDc Milling CNC System User Manual 274 Ⅱ Operation ...
Page 295: ...GSK980MDc Milling CNC System User Manual 276 Ⅱ Operation ...
Page 319: ...GSK980MDc Milling CNC System User Manual 300 Ⅱ Operation ...
Page 320: ...301 Ⅲ Installation Ⅲ Installation ...
Page 321: ...GSK980MDc Milling CNC System User Manual 302 Ⅲ Installation ...
Page 345: ...GSK980MDc Milling CNC System User Manual 326 Ⅲ Installation ...
Page 391: ...GSK980MDc Milling CNC System User Manual 372 Ⅲ Installation ...
Page 392: ...Appendix 373 Appendix Appendix ...
Page 393: ...GSK980MDc Milling CNC System User Manual 374 Appendix ...
Page 394: ...Appendix 375 Appendix Appendix 1 Outline Dimension of GSK980MDc L N ...