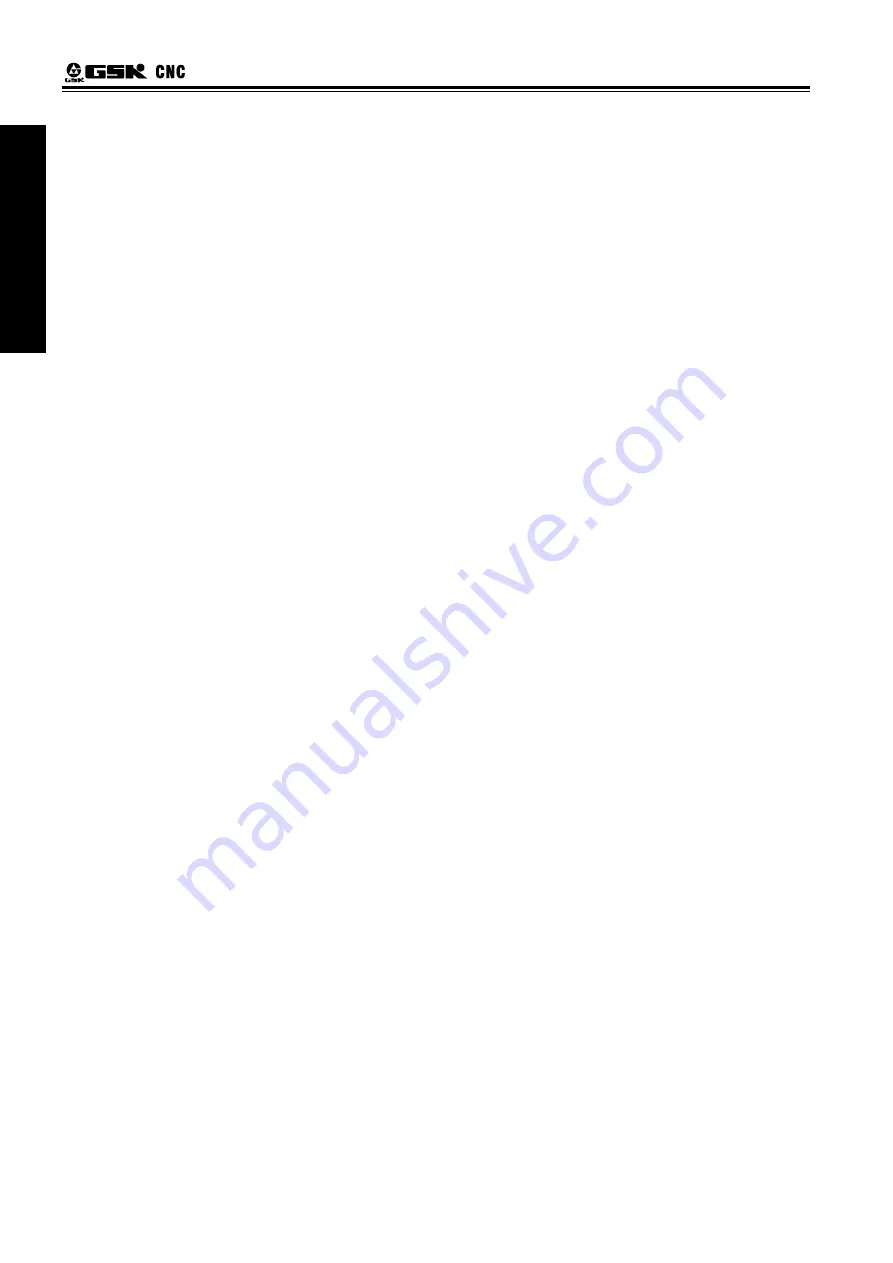
GSK980MDc Milling CNC System User Manual
86
I Programming
(1) G89 (Boring cycle) is basically same as the G85, a dwell is applied at the bottom of a hole (Dwell
time is specified by P, if it is not specified, the dwell is not applied, the command operation is same to
the G85)
(2) The command Q is disabled in this cycle, but its value is reserved as canned cycle modal value.
3.24.2.13 Groove Rough Milling Inside the Round G110/G111
Format:
G110
G98/G99
X_ Y_ R_ Z_ I_ W_ Q_ K_ V_ D_ F_
G111
Function:
From the beginning of the center point, arc interpolations are performed helically till the
round groove of programming dimension has been machined.
Explanation:
For command explanation of the canned cycle, see the table 3-2.
G110
:
Groove rough-milling inside the round in CCW;
G111: Groove rough-milling inside the round in CW;
I: I is radius inside the round groove, it should be more than the radius of current tool.
W: The firstly cutting depth is from the R reference level to the undersurface along the Z axis
direction, it should be more than 0 (The first cutting position is over the bottom of the groove,
then bottom position is regarded as machining position);
Q: The cutting incremental value each time along Z axis direction;
K: The width increment of cut inside XY plane, it should be less than the tool radius, and more
than 0;
V: The distance to the end machining plane at the rapid traverse, it should be more than 0
when cutting;
D: Tool radius serial number, the value range is 0~32, 0 is the default of D0. The current tool
radius is determined by the specified serial number.
Cycle process:
(1) Positioning to the XY plane level at the rapid traverse rate;
(2) Down to the point R plane at the rapid traverse rate;
(3) Cut W depth downwards in cutting feedrate
(4) Mill a round face with radius I helically by K increment each time from center point to outside.
(5) The Z axis is retracted to the R reference surface at the rapid traverse rate;
(6) X and Y axes are positioned to the center at the rapid traverse rate;
(7) Down to distance V to the end machining surface along Z axis at the rapid traverse rate;
(8) Cut along Z axis for (Q+V) depth;
(9) Cycling the operations from (4) ~ (8) till the round surface of total depth is finished.
(10) Return to the initial plane or point R plane according to G98 or G99.
Command Path:
Summary of Contents for 980MDc
Page 19: ...GSK980MDc Milling CNC User Manual XVIII ...
Page 20: ...1 I Programming Programming Ⅰ ...
Page 21: ...GSK980MDc Milling CNC System User Manual 2 I Programming ...
Page 139: ...GSK980MDc Milling CNC System User Manual 120 I Programming ...
Page 191: ...GSK980MDc Milling CNC System User Manual 172 I Programming ...
Page 192: ...173 Ⅱ Operation Ⅱ Operation ...
Page 193: ...GSK980MDc Milling CNC System User Manual 174 Ⅱ Operation ...
Page 200: ...Chapter 1 Operation Mode and Display 181 Ⅱ Operation ...
Page 201: ...GSK980MDc Milling CNC System User Manual 182 Ⅱ Operation ...
Page 249: ...GSK980MDc Milling CNC System User Manual 230 Ⅱ Operation ...
Page 253: ...GSK980MDc Milling CNC System User Manual 234 Ⅱ Operation ...
Page 259: ...GSK980MDc Milling CNC System User Manual 240 Ⅱ Operation ...
Page 265: ...GSK980MDc Milling CNC System User Manual 246 Ⅱ Operation ...
Page 293: ...GSK980MDc Milling CNC System User Manual 274 Ⅱ Operation ...
Page 295: ...GSK980MDc Milling CNC System User Manual 276 Ⅱ Operation ...
Page 319: ...GSK980MDc Milling CNC System User Manual 300 Ⅱ Operation ...
Page 320: ...301 Ⅲ Installation Ⅲ Installation ...
Page 321: ...GSK980MDc Milling CNC System User Manual 302 Ⅲ Installation ...
Page 345: ...GSK980MDc Milling CNC System User Manual 326 Ⅲ Installation ...
Page 391: ...GSK980MDc Milling CNC System User Manual 372 Ⅲ Installation ...
Page 392: ...Appendix 373 Appendix Appendix ...
Page 393: ...GSK980MDc Milling CNC System User Manual 374 Appendix ...
Page 394: ...Appendix 375 Appendix Appendix 1 Outline Dimension of GSK980MDc L N ...