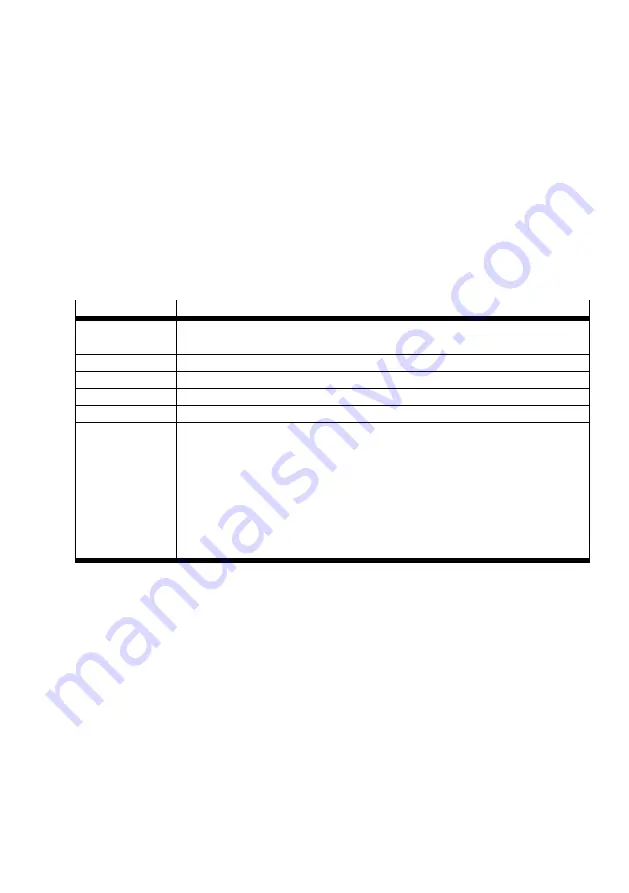
B
Diagnostic messages
Festo – GDCP-CMMP-M3/-M0-C-CO-EN – 1510b – English
219
B
Diagnostic messages
If an error occurs, the motor controller CMMP‐AS‐...‐M3/-M0 shows a diagnostic message cyclically in
the 7-segments display. An error message consists of an E (for Error), a main index and sub-index,
e.g.:
- E 0 1 0 -
.
Warnings have the same number as an error message. In contrast to error messages, however,
warnings are preceded and followed by hyphens, e.g.
- 1 7 0 -
.
B.1
Explanations on the diagnostic messages
The following table summarises the significance of the diagnostic messages and the actions to be
taken in response to them:
Terms
Significance
No.
Main index (error group) and sub-index of the diagnostic message.
Shown in the display, in FCT or diagnostic memory via FHPP.
Code
The Code column includes the error code (Hex) via CiA 301.
Message
Message that is displayed in the FCT.
Cause
Possible causes for the message.
Action
Action by the user.
Reaction
The Reaction column includes the error response (default setting, partially
configurable):
–
PS off (switch off output stage),
–
MCStop (fast stop with maximum current),
–
QStop (fast stop with parameterised ramp),
–
Warn (warning),
–
Ignore (No message, only entry in diagnostic memory),
–
NoLog (No message and no entry in diagnostic memory).
Tab. B.1
Explanations of the diagnostic messages
Under section B.2, you will find the error codes in accordance with CiA301/402 with assignment to the
error numbers of the diagnostic messages.
A complete list of the diagnostic messages corresponding to the firmware statuses at the time of print