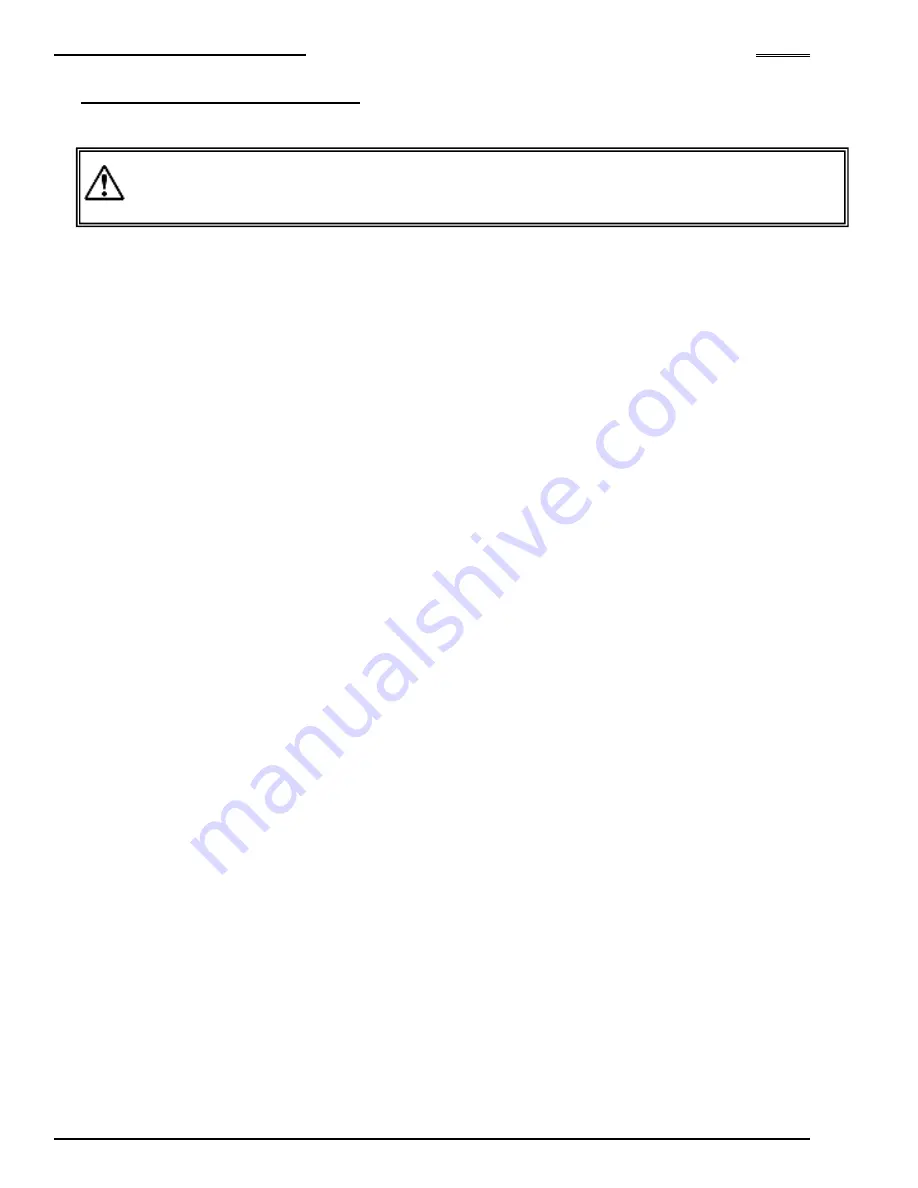
Chapter 4 Installation and Wiring
PAGE 4-34
4-6-6 Description of I/O Signals
[Input Signals]
Inputs can be sourced (PNP) or sinked (NPN) depending on the polarity of the 24VDC input power.
STOP
: Emergency Stop signal (Normally Closed)
This signal must be active (on) for controller operation. When it is inactive (off), controller
operation will stop, spindle motion stops and input/outputs will be disabled. If the signal is
turned off during a fastening cycle, spindle motion stops but the cycle data collected is
retained. A judgment will be made based upon the limits set in the active parameter.
RESET
: Reset signal (Normally Open)
When active (on), this signal will clear all data and discrete outputs. A Zero Check of the
torque transducer will be performed. During the Zero Check, the ACCEPT or REJECT lamp
will light to indicate the result of the Zero Check. If the system has been disabled by an
ABNORMAL output, the system will not return to normal operation until the abnormal
condition has been corrected.
This signal has to be input for 200~500ms.
Do not input this
signal between cycles due to the potential for data loss.
If the reset signal is turned “ON” while in cycle, the fastening cycle will be aborted.
REVERSE
: Reverse operation signal (Normally Open)
While the signal is “ON”, the spindle will turn in the direction opposite to the tightening
direction (IE: If the tightening direction is set to clockwise, the spindle will turn in the
counter-clockwise direction during Reverse operation and visa-versa).
The spindle unit will be is BUSY status while is Reverse operation. A signal will not be
accepted during the following conditions:
Stop condition
While fastening (when BUSY)
While resetting
Bypass condition
Abnormal condition
When a START or another REVERSE signal is output
During a CAL check
START
:
Cycle Start signal (Normally Open)
The unit reads the PARAMETER SELECT signal and SELF-CHECK signal at the start
(“OFF”-> “ON”) of this signal and then starts fastening.
The Start input requires a pulse of
200~500 milliseconds if the MFC Unit DIP switches are set up for AUTOMATIC Start input.
If the MFC Unit DIP switches are set up for DEADMAN (hand-held operations) input, the
Start input must be maintained "on" for the entire cycle.
The spindle unit will be in BUSY (in cycle) status after start of fastening. (BUSY can be used
to turn OFF the Start signal when start signal is set to Automatic)
In the following conditions, the READY output signal is turned “OFF” and the START signal
input cannot be received:
STOP condition
While fastening (when BUSY)
While resetting
Bypass condition
Abnormal condition
During a CAL check
If programmed for DEADMAN operation and the START input signal is turned off while
in cycle, the unit will stop and fastening will be judged.
・・・・
The input signals used in the standard I/O are described in this section. Please refer to
“Description of Input Signals” in regard to input signals used in the Fieldbus or the
expansion I/O.
Caution
Summary of Contents for AFC3000
Page 1: ...AFC3000E HW 1 ...
Page 17: ......
Page 18: ...Chapter 1 Outline PAGE 1 1 Chapter 1 Outline 1 ...
Page 25: ......
Page 26: ...Chapter 2 Specifications PAGE 2 1 Chapter 2 Specifications 2 ...
Page 34: ...Chapter 3 System Description PAGE 3 1 Chapter 3 System Description 3 ...
Page 64: ...Chapter 4 Installation and Wiring PAGE 4 1 Chapter 4 Installation and Wiring 4 ...
Page 131: ...Chapter 4 Installation and Wiring PAGE 4 68 Blank Page ...
Page 132: ...Chapter 5 I O Expansion Unit Page 5 1 Chapter 5 I O Expansion Unit 5 ...
Page 164: ...Chapter 6 Power up and Initial Checks PAGE 6 1 Chapter 6 Power Up and Initial Checks 6 ...
Page 168: ...Chapter 7 Fastening Instructions PAGE 7 1 Chapter 7 Fastening Instructions 7 ...
Page 207: ... Blank Page ...
Page 208: ...Chapter 8 System Operation PAGE 8 1 Chapter 8 System Operation 8 ...
Page 259: ...Chapter 8 System Operation PAGE 8 52 ...
Page 260: ...Chapter 9 Maintenance Inspection PAGE 9 1 Chapter 9 Maintenance Inspection 9 ...
Page 268: ...Chapter 10 Troubleshooting PAGE 10 1 Chapter 10 Troubleshooting 10 ...
Page 294: ......