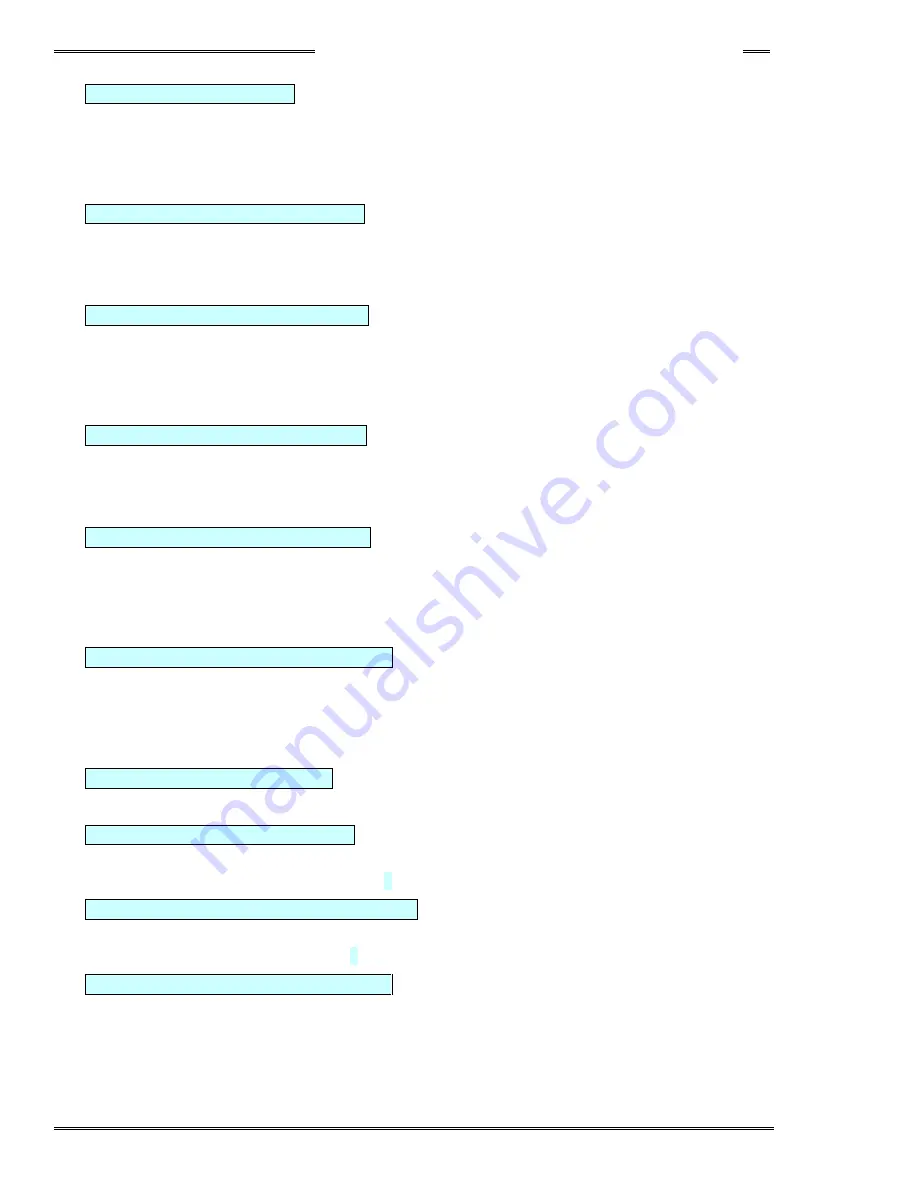
Chapter 8 System Operation
PAGE 8- 48
D-No.310 Initial Time
[sec]
Setting Range: 0
~
999.9
Set the time accordingly to mitigate shock occurred at the fastening start time or to slowly engage a
fastener (to improve engagement). During the D-No.310 [Initial Time], the start of the fastening will be
conducted at D-No.400 [Initial Speed].
When D-No.310 [Initial Time] is set as “0.0”, the operation will start in D-No.401 [Freerun Speed].
D-No.311
1
ST
Time Low Limit
[sec]
Setting Range
:
0
~
999.9
Set the time low limit between the start of fastening and the point D-No.105 [1
ST
Torque] or D-No.203 [1
ST
Angle] is reached.
When the 1
ST
Time Low Limit is not reached, the fastening judgment will be REJECT.
D-No.312
1
ST
Time High Limit
[sec]
Setting Range
:
0
~
999.9
Set the time high limit between the start of fastening and the point D-No.105 [1
ST
Torque] or D-No.203
[1
ST
Angle] is reached. Allow enough time to reach 1
st
Torque, but not so much time that cycle time
would be unacceptable if no fastener is present (or does not engage).
When the 1
ST
Time High Limit is exceeded, the fastening judgment will be REJECT .
D-No.313
2
ND
Time Low Limit
[sec]
Setting Range
:
0
~
999.9
Set the time low limit between D-No.105 [1
ST
Torque] or D-No.203 [1
ST
Angle] and the point D-No.103
[Standard Torque] or D-No.202 [Standard Angle] is reached.
When the 2
ND
Time Low Limit is not reached, the fastening judgment will be REJECT .
D-No.314
2
ND
Time High Limit
[sec]
Setting Range
:
0
~
999.9
Set the time high limit between D-No.105 [1
ST
Torque] or D-No.203 [1
ST
Angle] and the point D-No.103
[Standard Torque] or D-No.202 [Standard Angle] is reached. Allow enough time to reach Standard
Torque (from 1
st
Torque).
When the 2
ND
Time High Limit is exceeded, the fastening judgment will be REJECT .
D-No.315
Torque Recovery Time
[sec]
Setting Range
:
0
~
5.0
After fastening, Standard torque is maintained for this specified time.
•
This is not normally required and should be used with caution. (Mainly used for applications where
“joint relaxation” may occur) If time is set too long or causes duty cycle to go above 60%,
abnormal A.8-10 “Overload Abnormal” may occur.
D-No.318
Ramp Up Time
[sec]*
Setting Range
:
0.1
~
5.0
Set the time constant from the ZERO speed to when the tool’s maximum speed is reached.
D-No.319
Ramp Down Time
[sec]*
Setting Range
:
0.1
~
5.0
Set the time constant from the tool’s maximum speed to when ZERO speed is reached
from D-No. 104 [Ramp Down Start Torque]
D-No.320
Freerun Ramp Down Time
[sec]*
Setting Range
:
0.1
~
5.0
Set the time constant from the tool’s maximum speed to when ZERO speed is reached
from D-No. 500 [Freerun Revolutions]
D-No.321
1 Pulse Reverse Time
[sec]*
Setting Range
:
0
~
999.9
This is time used for D-No.005 [After Fastening Operation]
:
“1 Pulse Reverse”.
Set the operation time of D-No.XXX [1 Pulse Reverse Speed]
*Note: Unless required by special application, do not change D-No. 318, 319 or 320. These are
set automatically for optimum performance.
Summary of Contents for AFC3000
Page 1: ...AFC3000E HW 1 ...
Page 17: ......
Page 18: ...Chapter 1 Outline PAGE 1 1 Chapter 1 Outline 1 ...
Page 25: ......
Page 26: ...Chapter 2 Specifications PAGE 2 1 Chapter 2 Specifications 2 ...
Page 34: ...Chapter 3 System Description PAGE 3 1 Chapter 3 System Description 3 ...
Page 64: ...Chapter 4 Installation and Wiring PAGE 4 1 Chapter 4 Installation and Wiring 4 ...
Page 131: ...Chapter 4 Installation and Wiring PAGE 4 68 Blank Page ...
Page 132: ...Chapter 5 I O Expansion Unit Page 5 1 Chapter 5 I O Expansion Unit 5 ...
Page 164: ...Chapter 6 Power up and Initial Checks PAGE 6 1 Chapter 6 Power Up and Initial Checks 6 ...
Page 168: ...Chapter 7 Fastening Instructions PAGE 7 1 Chapter 7 Fastening Instructions 7 ...
Page 207: ... Blank Page ...
Page 208: ...Chapter 8 System Operation PAGE 8 1 Chapter 8 System Operation 8 ...
Page 259: ...Chapter 8 System Operation PAGE 8 52 ...
Page 260: ...Chapter 9 Maintenance Inspection PAGE 9 1 Chapter 9 Maintenance Inspection 9 ...
Page 268: ...Chapter 10 Troubleshooting PAGE 10 1 Chapter 10 Troubleshooting 10 ...
Page 294: ......