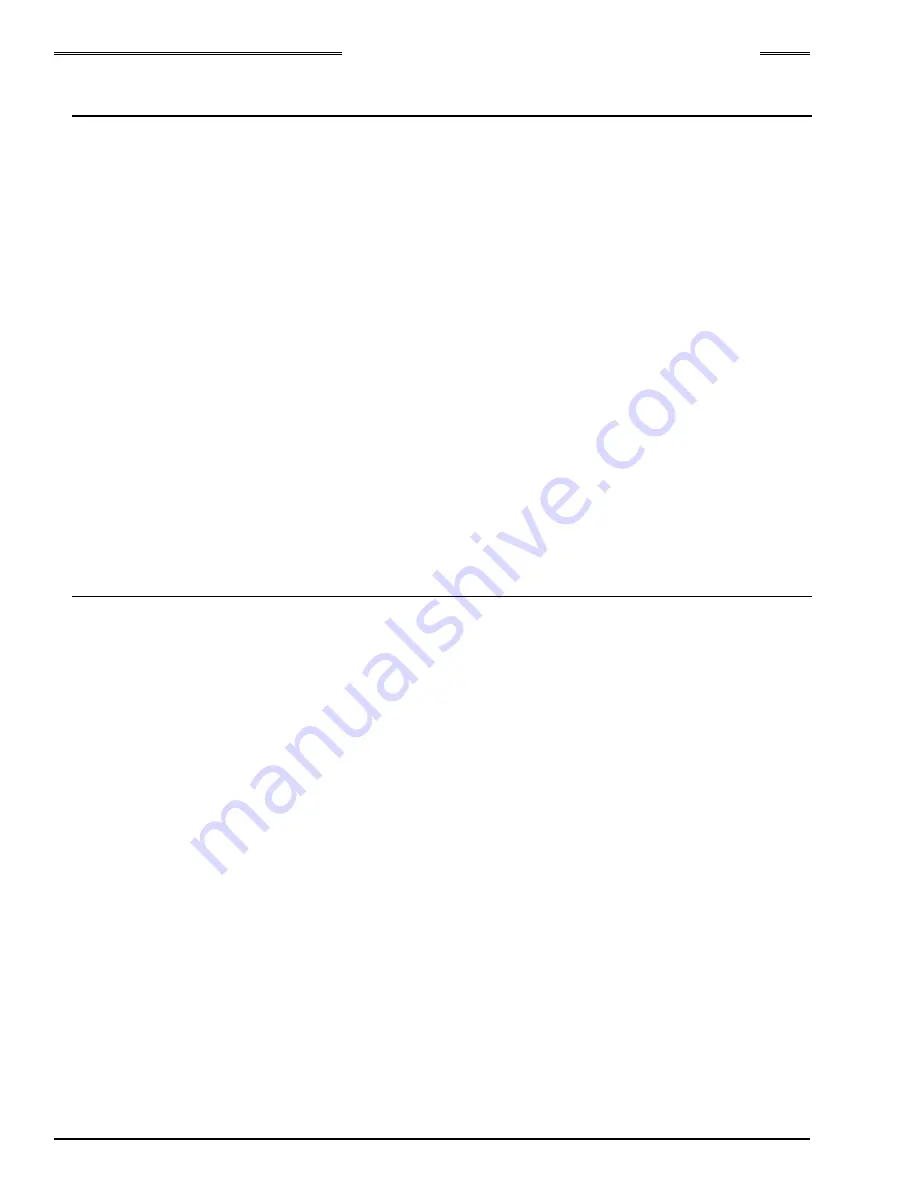
Chapter 10 Troubleshooting
PAGE 10-4
•
Code A01-03 - TORQUE TRANSDUCER / ZERO CHECK ERROR
The System detected a Zero Voltage Level Check error after a fastening START was attempted.
CAUSE:
•
When the tool torque transducer is sensing excessive torque due to pressure on the tool body
during a START signal to the controller (when tool normally should be in an idle state with no
external forces applied)
•
The tool cable is disconnected or lost connection while a START was attempted.
•
If the controller or the tool cable is located in an electric or magnetic noise field.
•
When the torque transducer, tool cable or the controller malfunctions.
RECOVERY:
1. Check that the tool has no external force applied to it (IE: anything touching the tool assembly,
misalignment, etc.). Also verify there is no excessive friction in the spindle assembly.
2. Verify that no excessive vibration or shock takes place on the tool mounting at the same time the
START signal is given to the system. (Vibration could be sensed by torque transducer)
3. Verify that the tool cable is securely connected at both ends and free from cuts, abrasive wear or
kinks
4. Verify that the tool cable or controller are not located near any high voltage transient power
sources. Relocate as required and reinitialize.
5. Turn control power off to the unit for at least 5 seconds then re-apply power
6. Exchange tool cable, tool and/or controller with known working units. Reinitialize the system after
each exchange to determine which component may have caused the failure (abnormal).
7. Replace the defective component.
•
Code A01-04 – TORQUE TRANSDUCER / CAL CHECK ERROR
The System detected a Calibration Voltage Check error after a fastening START was attempted
CAUSE:
•
When the tool torque transducer is sensing excessive torque due to pressure on the tool body
during a START signal to the controller (when tool normally should be in an idle state with no
external forces applied)
•
The tool cable is disconnected or lost connection while a START was attempted.
•
If the controller or the tool cable is located in an electric or magnetic noise field.
•
When the torque transducer, tool cable or the controller malfunctions.
RECOVERY:
1. Check that the tool has no external force applied to it (IE: anything touching the tool assembly,
misalignment, etc.). Also verify there is no excessive friction in the spindle assembly.
2. Verify that no excessive vibration or shock takes place on the tool mounting at the same time the
START signal is given to the system. (Vibration could be sensed by torque transducer)
3. Verify that the tool cable is securely connected at both ends and free from cuts, abrasive wear or
kinks
4. Verify that the tool cable or controller are not located near any high voltage transient power
sources. Relocate as required and reinitialize.
5. Turn control power off to the unit for at least 5 seconds then re-apply power
6. Exchange tool cable, tool and/or controller with known working units. Reinitialize the system after
each exchange to determine which component may have caused the failure (abnormal).
7. Replace the defective component.
Summary of Contents for AFC3000
Page 1: ...AFC3000E HW 1 ...
Page 17: ......
Page 18: ...Chapter 1 Outline PAGE 1 1 Chapter 1 Outline 1 ...
Page 25: ......
Page 26: ...Chapter 2 Specifications PAGE 2 1 Chapter 2 Specifications 2 ...
Page 34: ...Chapter 3 System Description PAGE 3 1 Chapter 3 System Description 3 ...
Page 64: ...Chapter 4 Installation and Wiring PAGE 4 1 Chapter 4 Installation and Wiring 4 ...
Page 131: ...Chapter 4 Installation and Wiring PAGE 4 68 Blank Page ...
Page 132: ...Chapter 5 I O Expansion Unit Page 5 1 Chapter 5 I O Expansion Unit 5 ...
Page 164: ...Chapter 6 Power up and Initial Checks PAGE 6 1 Chapter 6 Power Up and Initial Checks 6 ...
Page 168: ...Chapter 7 Fastening Instructions PAGE 7 1 Chapter 7 Fastening Instructions 7 ...
Page 207: ... Blank Page ...
Page 208: ...Chapter 8 System Operation PAGE 8 1 Chapter 8 System Operation 8 ...
Page 259: ...Chapter 8 System Operation PAGE 8 52 ...
Page 260: ...Chapter 9 Maintenance Inspection PAGE 9 1 Chapter 9 Maintenance Inspection 9 ...
Page 268: ...Chapter 10 Troubleshooting PAGE 10 1 Chapter 10 Troubleshooting 10 ...
Page 294: ......