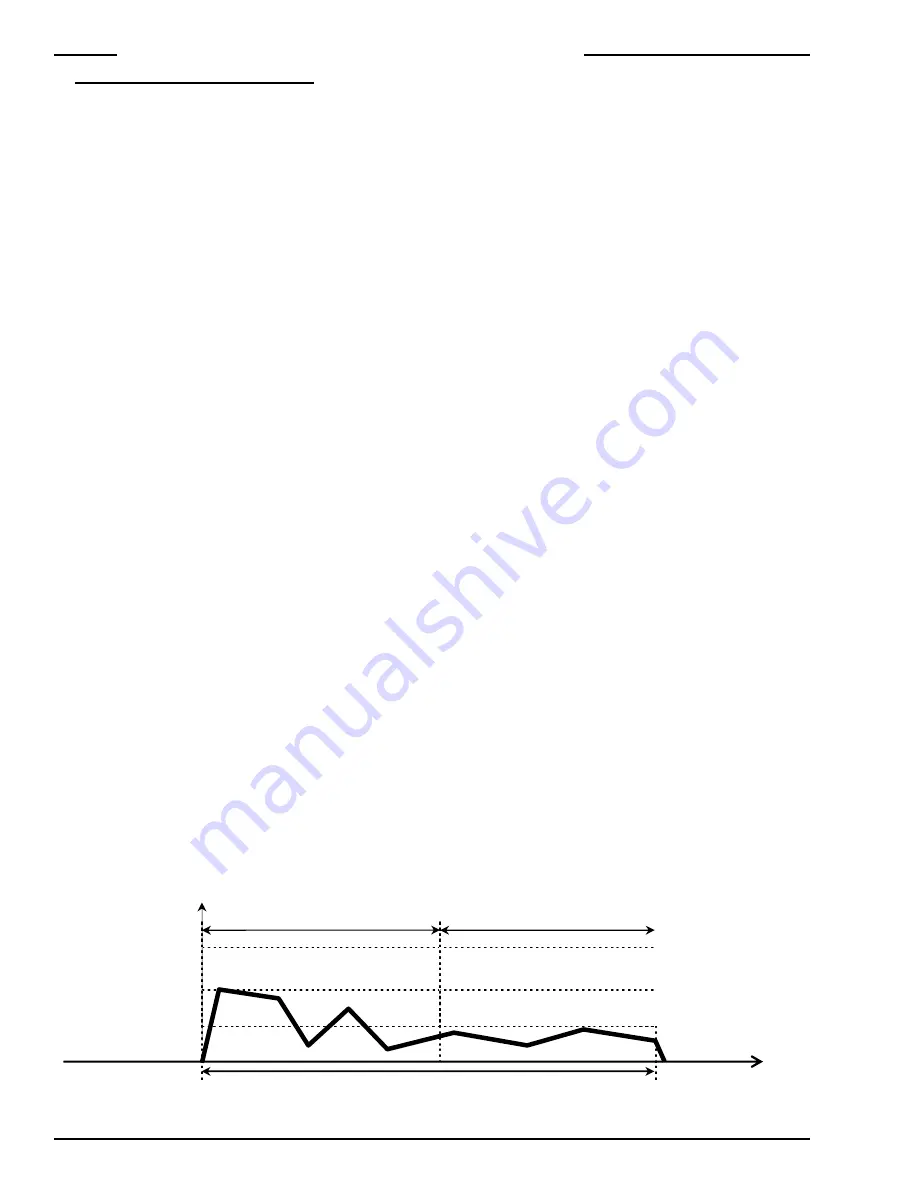
Chapter 7 Fastening Instructions
PAGE 7-24
7-2-5 Offset Check Function
The Offset Check is a function used for “offsetting” prevailing torque / load on the output drive of the tool
assembly during a no load, free spinning condition. Any external load sensed by the tools torque
transducer can detract from torque applied to a fastener during the fastening operation. In order to
detect torque inefficiency (the actual fastening installation torque being lower than the programmed
Standard torque), a rotation at no load checking operation (offset check) can be performed to judge
whether or not there are any influences on the fastening operation.
Use the offset check function in the following cases:
•
Tooling or equipment with an offset gear installed on the output square drive of the tool
•
Tooling or equipment with an angle head gear installed on the output square drive of the tool
•
Tooling with a complex mechanism from the output square drive of the tool to the socket or drive
bit (automatic bolt feeders, special adapter, any large mass, etc.)
Perform the offset check periodically during preparation for operation or upon change of
workpiece, etc., (off normal production) to confirm that the fastening torque is within the
normal range and no offset is being detected.
Operation Details of Offset Check
While the tool is not engaged to a part and is able to rotate freely, the Offset may be checked.
Typically, this should be programmed in a separate parmeter which can be called for when an Offset
Check is desired. (The system must be started using this assigned parameter) The average value
of the torque detected during the offset check operation will be judged. Data parameters:
•
D-No. 409 [Offset Check Speed] Speed at which the Offset Check is performed. (Should be
set to 60rpm or lower for stable results)
•
D-No. 505 [Offset Check Revolutions] Number of revolutions used for the Offset Check
•
D-No. 205 [Starting Torque Inhibit Angle] Number of degrees to ignore (inhibit) any temporary
torque signal anomalies which should not be included in the offset check (caused by inertia,
acceleration, backlash, vibration, etc.) Note: Torque Inhibit Check must be enabled in
Judgement Item 2 (D-No. 004)
•
D-No. 111 [Starting Torque Inhibit High Limit] Torque exceeding the Starting Torque Inhibit limit
during the offset check, will STOP operation and output a REJECT.
•
D-No. 102 [Peak Torque High Limit] Torque exceeding the Peak Torque High limit during the
offset check, will not stop the operation but the axis judgment result in a REJECT.
•
D-No. 119 [Final Torque High Limit] (Offset Torque High Limit)
If the average value of the torque detected within D-No. 505 [Offset Check Revolutions] exceeds
the final torque high limit, the axis judgment results in REJECT.
Also, the average torque value of the offset check will be displayed as the “Final Torque”
(Display fastening result mode: D-No. 20).
205 Starting Torque Inhibit Angle
505 Offset Check Revolutions
111 Starting Torque
Inhibit High Limit
102 Peak Torque
High Limit
The average torque in the torque
119 Final Torque High Limit
Start
check area must be below this.
(Offset Torque High Limit)
Torque
409 Offset Check Speed
Torque
Angle/
Revolutions
Summary of Contents for AFC3000
Page 1: ...AFC3000E HW 1 ...
Page 17: ......
Page 18: ...Chapter 1 Outline PAGE 1 1 Chapter 1 Outline 1 ...
Page 25: ......
Page 26: ...Chapter 2 Specifications PAGE 2 1 Chapter 2 Specifications 2 ...
Page 34: ...Chapter 3 System Description PAGE 3 1 Chapter 3 System Description 3 ...
Page 64: ...Chapter 4 Installation and Wiring PAGE 4 1 Chapter 4 Installation and Wiring 4 ...
Page 131: ...Chapter 4 Installation and Wiring PAGE 4 68 Blank Page ...
Page 132: ...Chapter 5 I O Expansion Unit Page 5 1 Chapter 5 I O Expansion Unit 5 ...
Page 164: ...Chapter 6 Power up and Initial Checks PAGE 6 1 Chapter 6 Power Up and Initial Checks 6 ...
Page 168: ...Chapter 7 Fastening Instructions PAGE 7 1 Chapter 7 Fastening Instructions 7 ...
Page 207: ... Blank Page ...
Page 208: ...Chapter 8 System Operation PAGE 8 1 Chapter 8 System Operation 8 ...
Page 259: ...Chapter 8 System Operation PAGE 8 52 ...
Page 260: ...Chapter 9 Maintenance Inspection PAGE 9 1 Chapter 9 Maintenance Inspection 9 ...
Page 268: ...Chapter 10 Troubleshooting PAGE 10 1 Chapter 10 Troubleshooting 10 ...
Page 294: ......