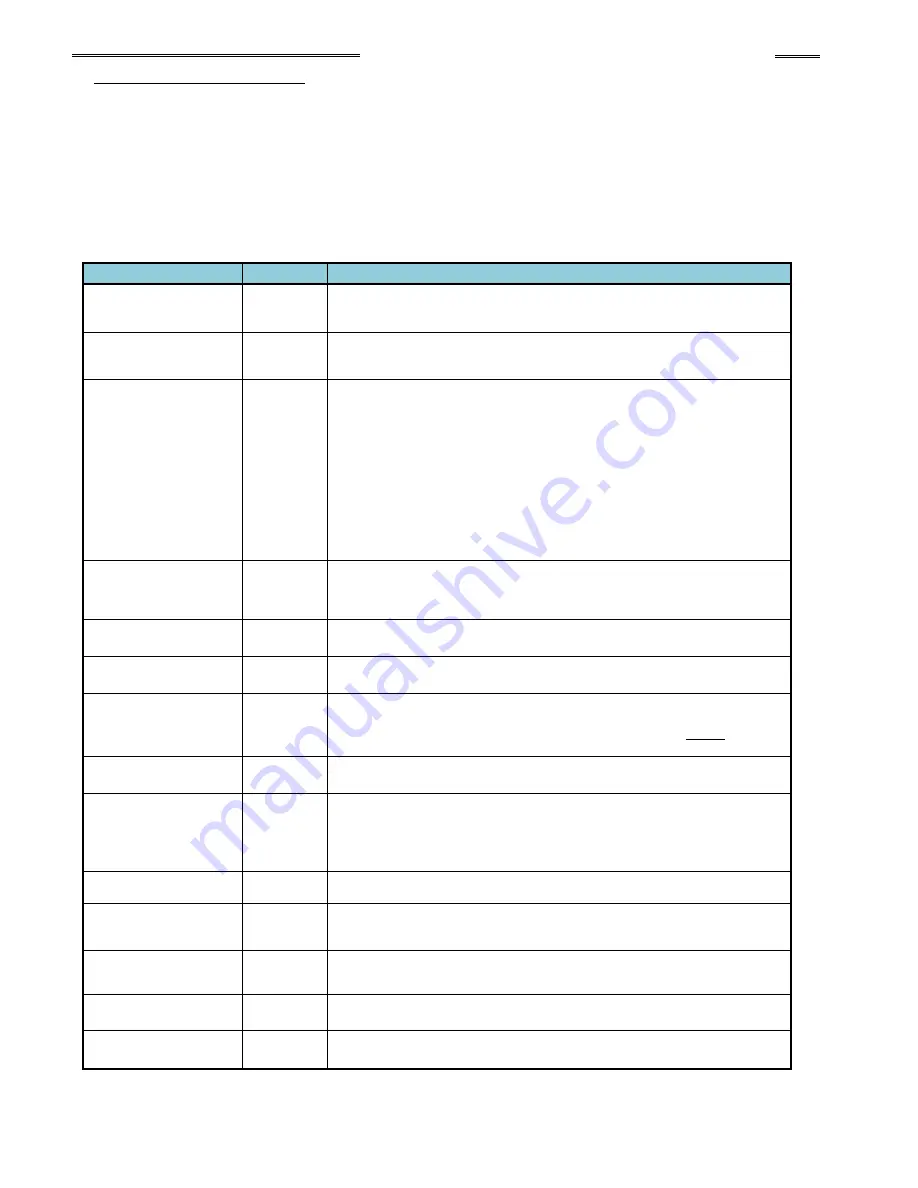
Chapter 5
I/O
Expansion Unit
Page 5-11
5-3-4 PLC Output Layout
The list below contains a description of output signals available on the Expansion I/O Interface.
Further output mapping can be found in the individual Fieldbus manuals. If configured as a MULTI
system, the MASTER controller can provide output signals for the TOTAL group of spindles as well as
invidual spindle signals (up to 32 spindles) These signals are user configurable using the AFC3000
User Console software and may be programmed on any designated output bit.
●
MASTER Output signals (Signals for total configured spindles (all connected spindles))
Signal
Connection
Description of Function/Usage
Total Reject
NO
Output when the fastening result is a REJECT. Indicates that one or more
spindles have failed achieving the fastening limits. This output remains
active until the START signal or RESET signal is input.
Total Accept
NO
Output when the fastening result is a ACCEPT. Indicates all spindles are
within fastening limits. This output remains active until the START signal or
RESET signal is input.
Abnormal
NO
Output when an Abnormal condition occurs. This signal indicates that the
System has detected an internal fault, and can no longer proceed. The
fault maybe generated from a connected spindle during a self-check
function. Check the individual spindle status to identify which spindle is
reporting the abnormal condition. (see AFC3000 Operation Manual for
troubleshooting) The spindle reporting an abnormal may be bypassed to
resume normal operation, however, the bypassed spindle will be ignored
and not run while in bypass. An Abnormal condition must be corrected
before the System will resume normal operation. The RESET signal clears
the abnormal condition.
Ready
NO
Output when the system is in the READY condition. Indicates system is
ready to operate, and inputs are enabled. This signal is inactive (off) when
the BUSY output is active (on).
Busy
NO
Output after a START signal is received, and active until the fastening
cycle is complete and the READY signal is output.
End
NO
Output when a fastening cycle is complete. Remains active until the
START, RESET or REVERSE signal is input.
Sequence Select
(BIT)
NO
Output confirmation of SEQUENCE SELECT 0~4 input selections.
Sequence bits are active according to what sequence is set from the
sequence select inputs. Used to confirm proper sequence before fastening
starts.
Sequence Select
(Individual 1-32)
NO
Output confirmation of Individual SEQUENCE SELECT 1-32 input
selections.
Signal Output Ports
(1 to 8)
NO
These signals will output when the fastening sequence reaches a step that
has a [PLC OUTPUT] instruction inserted. Used to provide sequence
operation status to external PLC’s and/or control outputs for slide motion,
lights, & buzzers, etc without the use of a PLC. (The AFC User Console
Software can set these outputs on and off in the fastening sequence)
Spindle in Bypass
NO
Signal is active when any of the connected spindles are bypassed either
from San Unit bypass input signals or from the San Unit bypass switch.
Current Limit
Warning
NO
Active when the high current limit has been exceeded. This can be used to
identify potential motor failure before total failure occurs by identifying high
current draws over what the typical current draw is for the application.
Data Available
(Fastening Result)
NO
This output turns “ON” when fastening data is available in the controller. It
turns “OFF” when the data is collected by the AFC3000 Software.
CAL Voltage Error
Warning
NO
This is output when a CAL voltage error has occurred in any of the
controllers
ZERO Voltage Error
Warning
NO
This is output when a ZERO voltage error has occurred in any of the
controllers
* NO: Normal Open
Summary of Contents for AFC3000
Page 1: ...AFC3000E HW 1 ...
Page 17: ......
Page 18: ...Chapter 1 Outline PAGE 1 1 Chapter 1 Outline 1 ...
Page 25: ......
Page 26: ...Chapter 2 Specifications PAGE 2 1 Chapter 2 Specifications 2 ...
Page 34: ...Chapter 3 System Description PAGE 3 1 Chapter 3 System Description 3 ...
Page 64: ...Chapter 4 Installation and Wiring PAGE 4 1 Chapter 4 Installation and Wiring 4 ...
Page 131: ...Chapter 4 Installation and Wiring PAGE 4 68 Blank Page ...
Page 132: ...Chapter 5 I O Expansion Unit Page 5 1 Chapter 5 I O Expansion Unit 5 ...
Page 164: ...Chapter 6 Power up and Initial Checks PAGE 6 1 Chapter 6 Power Up and Initial Checks 6 ...
Page 168: ...Chapter 7 Fastening Instructions PAGE 7 1 Chapter 7 Fastening Instructions 7 ...
Page 207: ... Blank Page ...
Page 208: ...Chapter 8 System Operation PAGE 8 1 Chapter 8 System Operation 8 ...
Page 259: ...Chapter 8 System Operation PAGE 8 52 ...
Page 260: ...Chapter 9 Maintenance Inspection PAGE 9 1 Chapter 9 Maintenance Inspection 9 ...
Page 268: ...Chapter 10 Troubleshooting PAGE 10 1 Chapter 10 Troubleshooting 10 ...
Page 294: ......