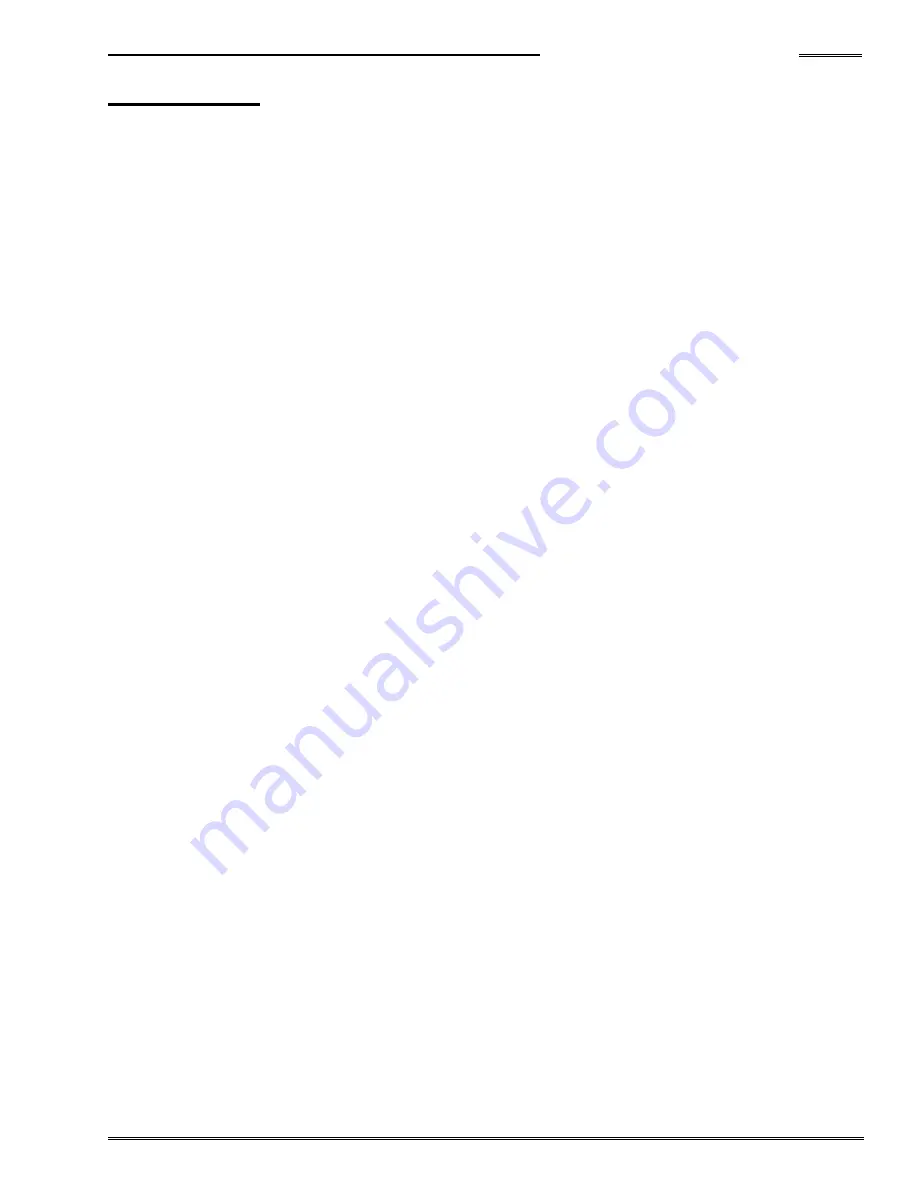
Chapter 1 Outline
PAGE 1-5
1-3 Functions
(1) Fastening functions
The AFC3000 is user programmable to select from two different fastening methods, referred to as
the Torque Control and the Angle Control methods. These methods can be selected for either
clockwise (CW) or counter-clockwise (CCW) operation.
1. Torque Control Method: Angle Monitoring
・
Torque Rate Monitoring
・
1/2/3 Step Fastening.
2. Angle Control Method: Torque Monitoring
・
Torque Rate Monitoring
・
1/2/3 Step Fastening.
3. Offset Check: Torque generated “outside” of the tooling (ie. external gearing, drives, spindles)
can be compensated for using the Offset check function.
Two or Three-step fastening will be used for performing synchronized fastenings using multiple
spindles. Each spindle stops and waits when they reach the previously defined step value. When all
connected spindles have reached the same value, they will simultaneously start again and rundown
to the next step value.
(2) Bypass Function (BYPASS)
When a PLC Bypass input signal is activated or when the RUN/BYPASS switch on the front panel is
switched to the Bypass position, the Bypass output signal is activated. In this condition, the spindle
will not START, REVERSE, CAL OR RESET. If a BYPASS condition occurs during the fastening
operation, the fastening operation will stop. When the unit is in the bypass mode, the red "Bypass"
LED on the front panel of the bypassed unit will light. In a mutli-spindle configuration, the bypassed
spindle is ignored as if it doesn’t exist. This allows a spindle to be bypassed while all other
connected spindles continue to operate.
(3) Abnormal Signal Output Function
Any system fault Abnormal state code numbers are displayed on the Controller (MFC) Unit front
panel.
If a system error occurs during a system check, connection check or overload check, an abnormal
signal will be output. In this situation, the STATUS LED (Red) on the unit will light up and an
abnormal state number and sub code will be displayed.
(4) Tool Type Checking Function
The parameter tool type and the connected tool type will be checked when the power turns on or the
tools are replaced. If the tool types are different, an abnormal will occur identifying that there is a tool
typre mis-match.
(5) Self-check function
When control power is turned “ON”, the values of the torque tranducer ZERO voltage and CAL
voltage are acquired (these are reference values used for fastening). Before each fastening cycle,
the ZERO voltage and the CAL voltage of the torque transducer are acquired and compared to the
reference values from the power on check before the fastening operation is executed (the self-check
is not executed in the case of reverse operation).
Also, the fastening operation can be started without execution of the self-check function by using the
following settings,.
・
Single system
・・・
PLC I/O input signal “SELF CHECK DISABLE”: “ON”
・
Multi system
・・・
Sequence command “SELF CHECK”: “OFF”
Summary of Contents for AFC3000
Page 1: ...AFC3000E HW 1 ...
Page 17: ......
Page 18: ...Chapter 1 Outline PAGE 1 1 Chapter 1 Outline 1 ...
Page 25: ......
Page 26: ...Chapter 2 Specifications PAGE 2 1 Chapter 2 Specifications 2 ...
Page 34: ...Chapter 3 System Description PAGE 3 1 Chapter 3 System Description 3 ...
Page 64: ...Chapter 4 Installation and Wiring PAGE 4 1 Chapter 4 Installation and Wiring 4 ...
Page 131: ...Chapter 4 Installation and Wiring PAGE 4 68 Blank Page ...
Page 132: ...Chapter 5 I O Expansion Unit Page 5 1 Chapter 5 I O Expansion Unit 5 ...
Page 164: ...Chapter 6 Power up and Initial Checks PAGE 6 1 Chapter 6 Power Up and Initial Checks 6 ...
Page 168: ...Chapter 7 Fastening Instructions PAGE 7 1 Chapter 7 Fastening Instructions 7 ...
Page 207: ... Blank Page ...
Page 208: ...Chapter 8 System Operation PAGE 8 1 Chapter 8 System Operation 8 ...
Page 259: ...Chapter 8 System Operation PAGE 8 52 ...
Page 260: ...Chapter 9 Maintenance Inspection PAGE 9 1 Chapter 9 Maintenance Inspection 9 ...
Page 268: ...Chapter 10 Troubleshooting PAGE 10 1 Chapter 10 Troubleshooting 10 ...
Page 294: ......