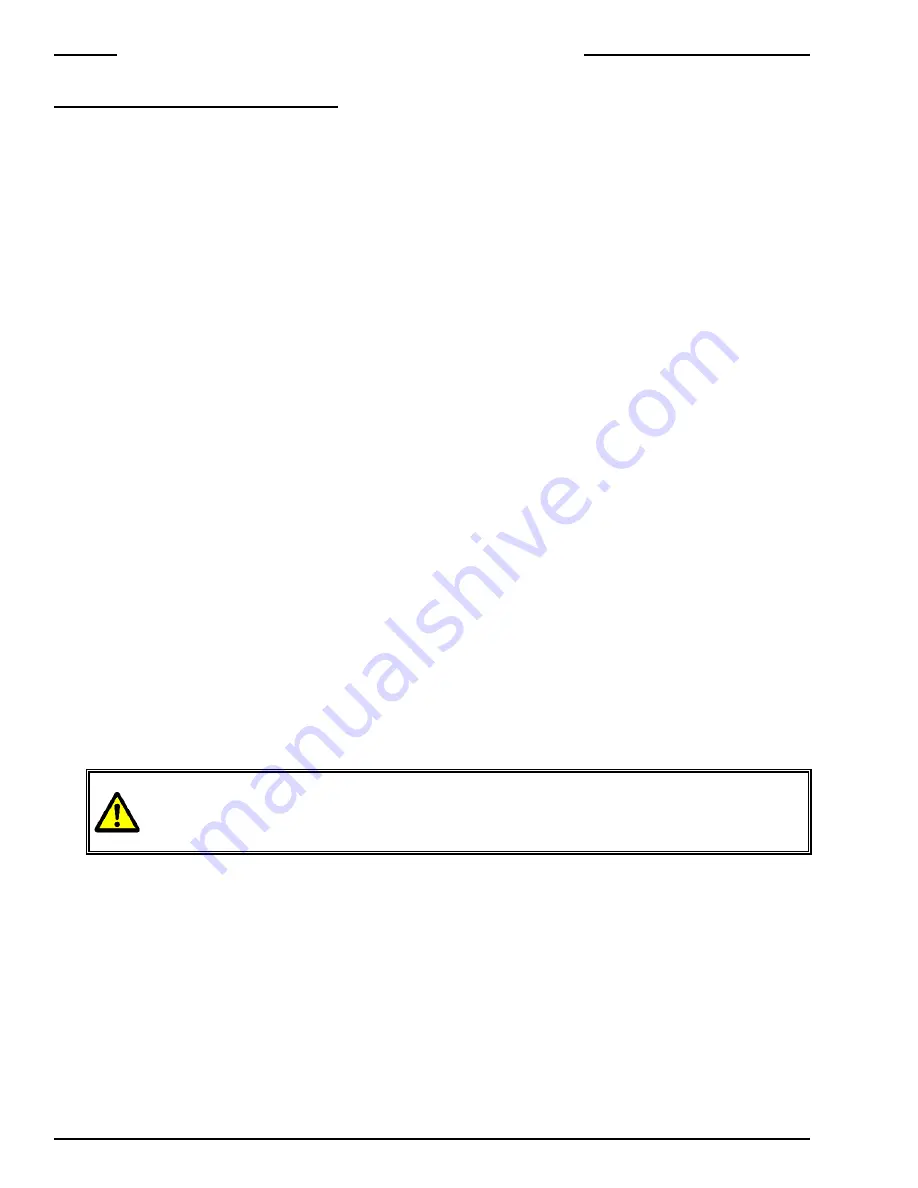
Chapter 7 Fastening Instructions
PAGE 7-38
7-4 Fastening Speed &Time
The AFC3000 System is user-programmable for operations involving multiple speed settings. The use of
multiple speeds during the fastening process aids in socket engagement, achieving cycle time and
controlling the applied torque during all stages. Speed functions work the same for Torque Control and Angle
Control using any of the previously stated standard Judge functions. Special conditions that affect these
operations will be identified in the appropriate section.
1. The system will fasten to the 1
ST
TORQUE/ANGLE value during the specified 1
st
TIME limits. The
following fastening operations occur during 1
st
time:
a) The system starts off running at INITIAL SPEED for the period specified by INITIAL TIME.
The initial time should be set to mitigate shock occurred at the fastening start time or to
engage a bolt and a socket.
b) Upon completion of INITIAL TIME the system switches to FREERUN SPEED for the period
specified by FREERUN REVOLUTIONS. The number of revolutions required to complete
INITIAL TIME will be deducted from the number of revolutions ran at FREERUN SPEED.
c) Once RAMP DOWN START TORQUE is detected or FREERUN REVOLUTIONS expires, the
system will switch from FREERUN SPEED to 1
st
SPEED and continue to fasten until 1
st
TORQUE/ANGLE is attained or the 1ST TIME HIGH LIMIT is reached. 1
st
SPEED is
switched right before the fastener is seated and is intended to provide adequate speed to
seat the fastener without getting a load to the tool.
2. Upon reaching 1ST Torque/Angle, 1
st
Time ends and 2
ND
Time begins. 1ST Torque/Angle is the shift
point from 1
st
Speed to 2
nd
Speed and the synchronization point prior to commencing the 2
nd
Step.
3. For a 2 step fastening, the system will fasten to Standard Torque/Angle using 2
nd
Speed during the
specified 2
nd
Time limits. Standard Torque/Angle must be reached within the 2
nd
Time Low/High
Limits or a reject will occur. The fastening result will output as REJECT (NG). (The time judgment
cannot be disabled.)
4. If the 2
nd
Torque/Angle is detected before the Standard Torque/Angle, the speed is switched from
2
nd
Speed to 3
rd
Speed. 2
nd
Torque/Angle is the synchronization point prior to commencing the
3rd step.
For a 3 step fastening, the system will fasten to Standard Torque/Angle using 3
rd
Torque Speed
during the specified 2
nd
Time Limits. Standard Torque/Angle must be reached within the 2
nd
Time
Low/High Limits or a reject will occur. The fastening result will output as REJECT (NG). (The time
judgment cannot be disabled.)
・
・
・
・
When D-No.109 [2
ND
Torque] is set to 95
~
~
~
~
100
%
%
%
%
of D-No.103 [Standard Torque], the
fastening speed is automatically set to 3rpm after the 2
nd
Torque is detected.
・
・
・
・
This function is not recommended for fastening a soft joint. An Abnormal A.8-10
[OVERLOAD ABNORMAL] may occur.
Summary of Contents for AFC3000
Page 1: ...AFC3000E HW 1 ...
Page 17: ......
Page 18: ...Chapter 1 Outline PAGE 1 1 Chapter 1 Outline 1 ...
Page 25: ......
Page 26: ...Chapter 2 Specifications PAGE 2 1 Chapter 2 Specifications 2 ...
Page 34: ...Chapter 3 System Description PAGE 3 1 Chapter 3 System Description 3 ...
Page 64: ...Chapter 4 Installation and Wiring PAGE 4 1 Chapter 4 Installation and Wiring 4 ...
Page 131: ...Chapter 4 Installation and Wiring PAGE 4 68 Blank Page ...
Page 132: ...Chapter 5 I O Expansion Unit Page 5 1 Chapter 5 I O Expansion Unit 5 ...
Page 164: ...Chapter 6 Power up and Initial Checks PAGE 6 1 Chapter 6 Power Up and Initial Checks 6 ...
Page 168: ...Chapter 7 Fastening Instructions PAGE 7 1 Chapter 7 Fastening Instructions 7 ...
Page 207: ... Blank Page ...
Page 208: ...Chapter 8 System Operation PAGE 8 1 Chapter 8 System Operation 8 ...
Page 259: ...Chapter 8 System Operation PAGE 8 52 ...
Page 260: ...Chapter 9 Maintenance Inspection PAGE 9 1 Chapter 9 Maintenance Inspection 9 ...
Page 268: ...Chapter 10 Troubleshooting PAGE 10 1 Chapter 10 Troubleshooting 10 ...
Page 294: ......