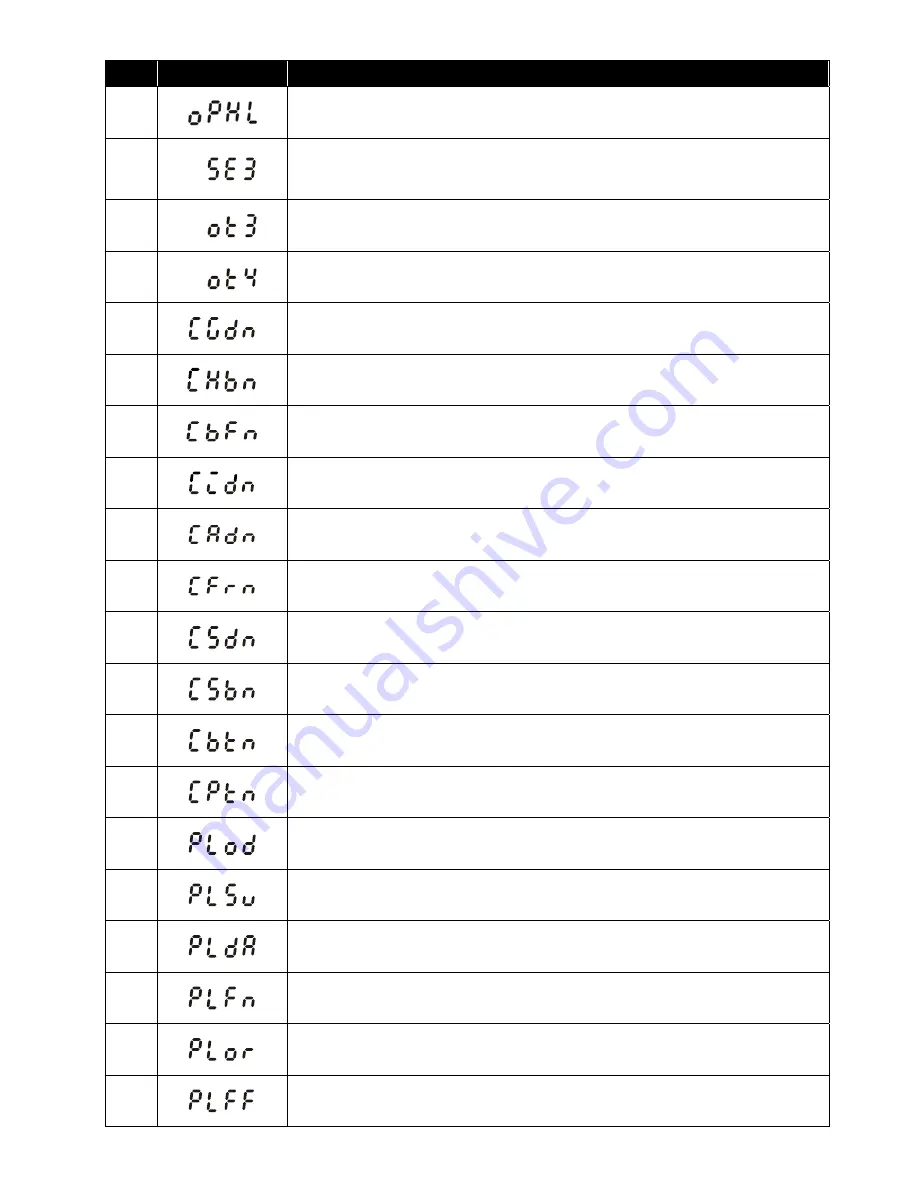
Chapter 13 Warning Codes
MS300
(High Speed Model)
13-3
ID No.
Display
Descriptions
28
Output phase loss
30
Keypad COPY error 3
Keypad copy between different power range drive
31
Over torque warning of motor 3
32
Over torque warning of motor 4
36
CANopen guarding time-out 1
37
CANopen heartbeat time-out 2
39
CANopen bus off
40
CANopen index error
41
CANopen station address error
42
CANopen memory error
43
CANopen SDO transmission time-out
44
CANopen SDO received register overflow
45
CANopen boot up fault
46
CANopen protocol format error
50
PLC download error, opposite data defect
51
PLC download and save error
52
Data error during PLC operation
53
PLC download Function code error
54
PLC register overflow
55
PLC operation Function code error
Summary of Contents for VFD11AMS21AFSHA
Page 5: ...IV This page intentionally left blank...
Page 8: ...Chapter 1 Introduction MS300 High Speed Model 1 3 1 2 Model Name 1 3 Serial Number...
Page 20: ...Chapter 3 Installation MS300 High Speed Model 3 3...
Page 21: ...Chapter 3 Installation MS300 High Speed Model 3 4 This page intentionally left blank...
Page 24: ...Chapter 4 Wiring MS300 High Speed Model 4 3 4 1 Wiring...
Page 25: ...Chapter 4 Wiring MS300 High Speed Model 4 4 Figure 1...
Page 27: ...Chapter 4 Wiring MS300 High Speed Model 4 6 4 2 System Wiring Diagram...
Page 43: ...Chapter 6 Control Terminals MS300 High Speed Model 6 6 This page intentionally left blank...
Page 91: ...Chapter 8 Optional Cards MS300 High Speed Model 8 8 Frame F Fig 8 16...
Page 115: ...Chapter 9 Specification MS300 High Speed Model 9 10 This page intentionally left blank...
Page 123: ...Chapter 10 Digital Keypad MS300 High Speed Model 10 8 This page intentionally left blank...
Page 293: ...Chapter 13 Warning Codes MS300 High Speed Model 13 6 This page intentionally left blank...
Page 303: ...Chapter 14 Error Codes MS300 High Speed Model 14 10 This page intentionally left blank...