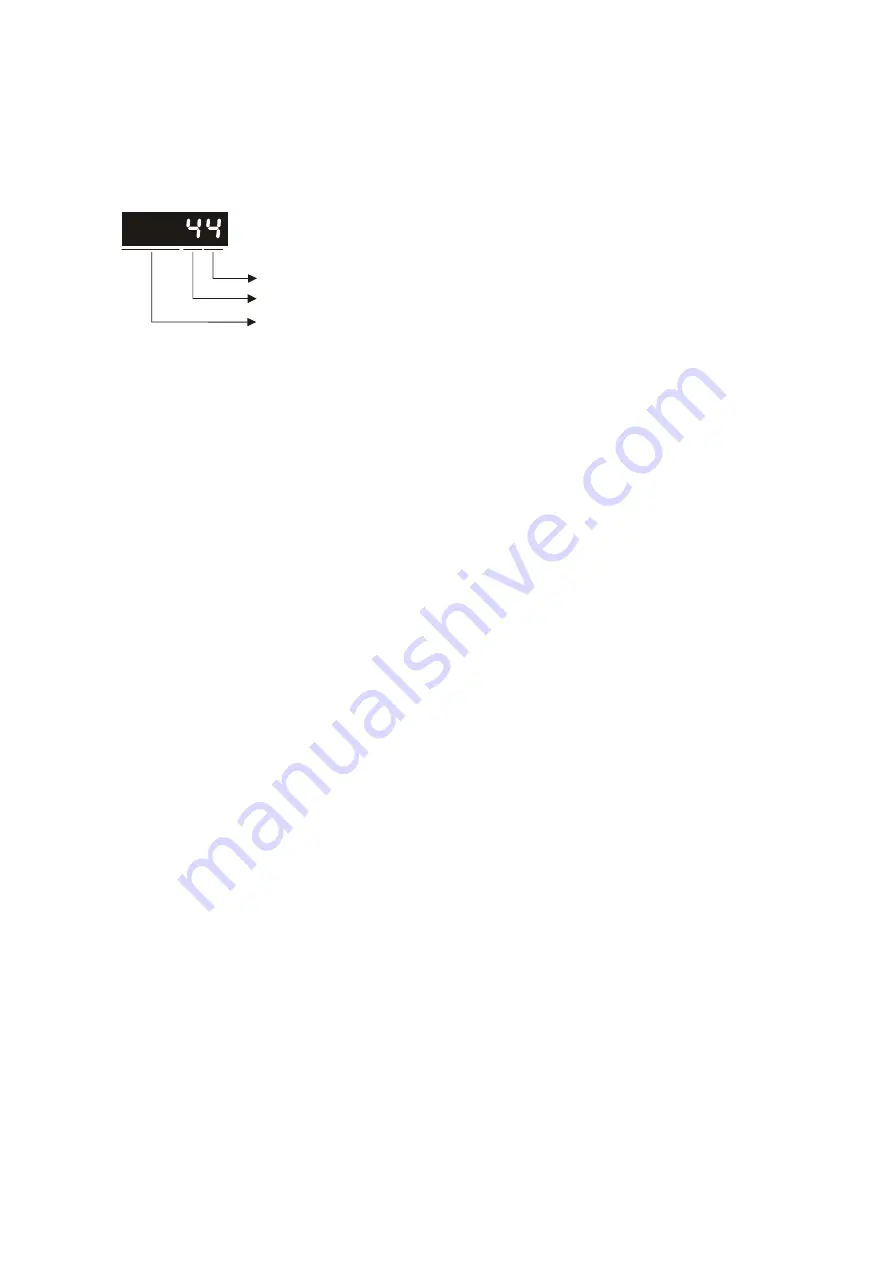
Chapter 5 Trial Run and Tuning Procedure
|
ASDA-A&A+ Series
Revision April 2009
5-17
5.6.3 Easy Mode Tuning Flowchart
Set P2-31 to 1 (Easy Mode, for ASDA-A series only, ASDA-A+ series does not support this mode)
P2-31 Auto and Easy Mode Selection (Default setting is 4)
Settings:
not used
A
B
ASDA-A series:
This parameter allows the users to set the stiffness setting of easy mode and the responsiveness level
of auto-tuning mode. Users can control the stiffness and responsiveness according to application
condition. When the setting value is higher, the stiffness and the responsiveness is higher.
A: Stiffness setting of easy mode
B: Responsiveness level of auto-tuning mode
ASDA-A+ series:
This parameter allows the users to set the responsiveness level setting of auto-tuning mode. Users can
control the responsiveness according to application condition. When the setting value is higher, the
responsiveness is higher.
A: No function
B: Responsiveness level of auto-tuning mode
In Easy Mode, the value “A” indicates the stiffness setting. When the setting value is higher, the control
stiffness is also higher
Adjust P2-31: Increase the setting value of P2-31. Increase the value “A” to add the control stiffness or
reduce the noise.
Adjust P2-25: According to the setting value of P2-31 add and adjust the control stiffness.
Continuously adjust until the satisfactory performance is achieved, and then the tuning is completed.
Call 1(800)985-6929 for Sales
deltaacdrives.com
Call 1(800)985-6929 for Sales
deltaacdrives.com