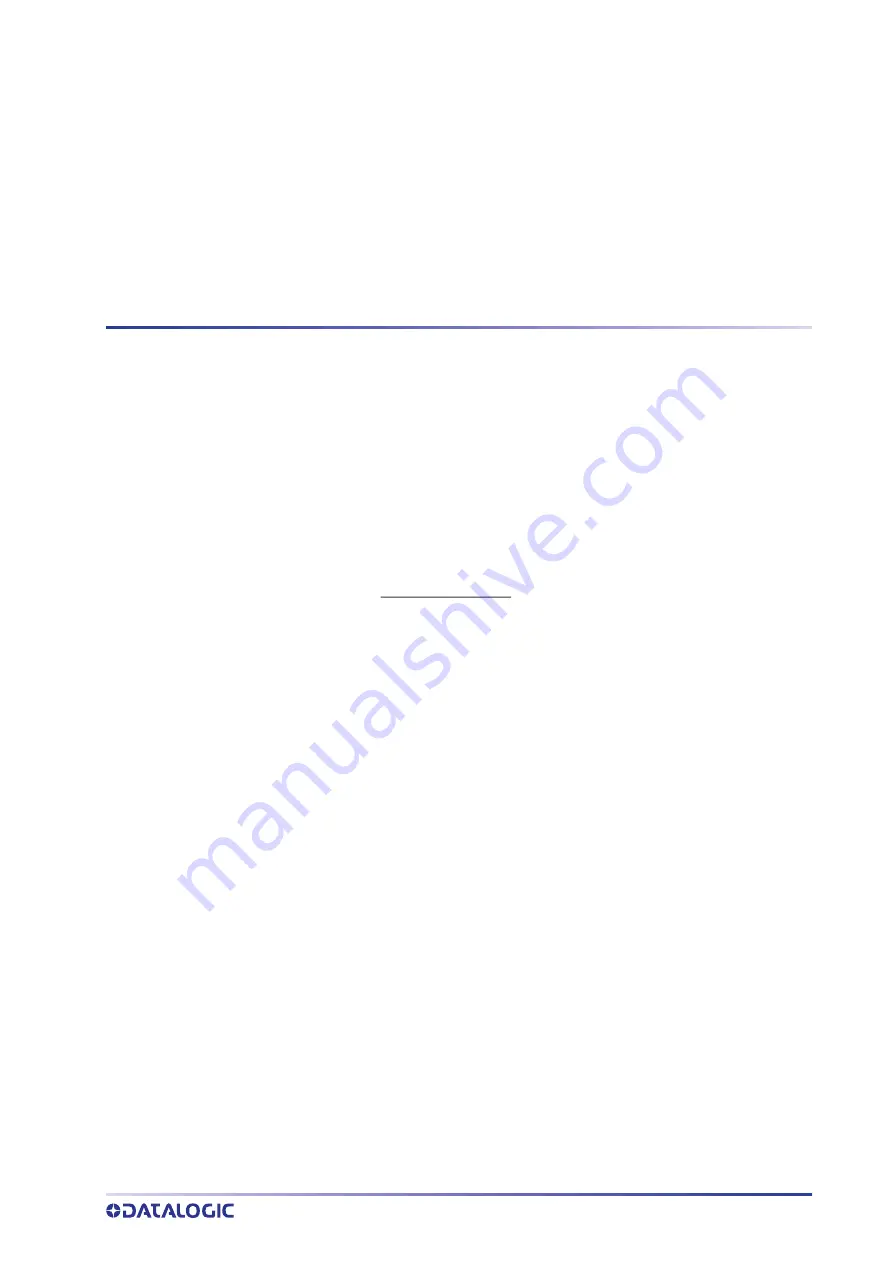
INSTRUCTION MANUAL
43
CHAPTER 6
PROFINET INTERFACE
A BRIEF INTRODUCTION TO PROFINET
PROFINET IO is the open industrial network devised for automation applications and
built on the Ethernet application layer (TCP/IP and IT standards). For PROFINET IO the
layers 1 through 7a of the ISO/OSI (Open Systems Interconnection) reference model are
exclusively based on internationally proven standards. The functionality of PROFINET is
defined in layer 7b. PROFINET IO complies with IEEE802.3 Ethernet Standard and fol
-
lows the standards IEC 61158 and IEC61784, so it is 100% Ethernet compatible.
Its technology development and standardization are entrusted to Profibus & Profinet
International (PI), the international umbrella organization including members of more
www.profibus.com
).
PROFINET IO is expressly developed to connect controllers (named IO controllers, equiv
-
alent to Profibus DP Masters), peripheral devices (named IO devices, similar to Profibus
DP Slaves) and programming devices / PCs (named IO supervisors) with Ethernet Real
Time (RT) and Isochronous Real Time (IRT) communication all the way. Real Time chan
-
nel is used for time-critical process data and allows to meet the real-time requirements
of the automation engineering (cycle times < 500 µs, jitter < 1 µs); while IRT is suitable
for sophisticated motion control and high performance applications in factory automa
-
tion and permits cycle times lower than 250 µs with less than 1 µs jitter. The standard
TCP/IP channel is used for parametrization, configuration and acyclic read/write opera
-
tions.
A PROFINET IO system requires at least one IO Controller and one IO Device. The most
frequent network topologies can be implemented and even mixed together including
Star, Line, Tree and Ring structures by means of copper or fiber-optic cables. The num
-
ber of devices (each one fitted with its own MAC address, IP address and device name)
which can be connected in the PROFINET network is virtually unlimited. The transmis
-
sion rate is 100Mbit/s with full duplex communication (Fast Ethernet).
PROFINET IO Devices are configured using a configuration tool which acts as the IO
Supervisor. The IO Supervisor uses a GSD (General Station Description) file based on
XML language, thus it is called GSDML file, see "
Summary of Contents for AMT58 Series
Page 1: ......
Page 8: ......
Page 13: ...AMT58x CB CANopen 5 3 1 3 Fissaggio con flangia codice ST 58 FLNG ...
Page 52: ......
Page 55: ...Subject index ...
Page 62: ...AMT58x PB Profibus 5 3 1 3 Installation using a flange code ST 58 FLNG ...
Page 101: ......
Page 102: ......
Page 109: ......
Page 114: ...AMT58x EC EtherCAT 5 3 1 3 Installation using a flange code ST 58 FLNG ...
Page 166: ......
Page 167: ...AMT58 PN INSTRUCTION MANUAL Absolute Encoders ...
Page 180: ...LIST OF ABBREVIATIONS xiv AMT58 PN ...
Page 221: ...TO TECHNOLOGY OBJECTS INSTRUCTION MANUAL 41 Figure 28 TO encoder enabled ...
Page 231: ...INSTRUCTION MANUAL 51 ...
Page 265: ...NORMAL OPERATION DIAGRAM INSTRUCTION MANUAL 85 NORMAL OPERATION DIAGRAM ...
Page 266: ...ENCODER STATE MACHINE 86 AMT58 PN PRESET DIAGRAM ...
Page 267: ...PARKING SENSOR DIAGRAM INSTRUCTION MANUAL 87 PARKING SENSOR DIAGRAM ...
Page 269: ...ERROR DIAGRAM INSTRUCTION MANUAL 89 Acknowledgment of not acknowledgeable sensor error ...
Page 284: ......
Page 285: ......
Page 287: ......
Page 294: ......
Page 299: ...AMT58x CB CANopen 5 3 1 3 Installation using a flange code ST 58 FLNG ...
Page 335: ......
Page 345: ...AMT58x DN DeviceNET 5 3 1 3 Installation using a flange code ST 58 FLNG ...
Page 380: ...AMT58x DN DeviceNET 40 Default 21h ...
Page 384: ...AMT58x DN DeviceNET 44 Default 00h ...
Page 394: ......
Page 404: ...AMT58x PB Profibus 5 3 1 3 Installation using a flange code ST 58 FLNG ...