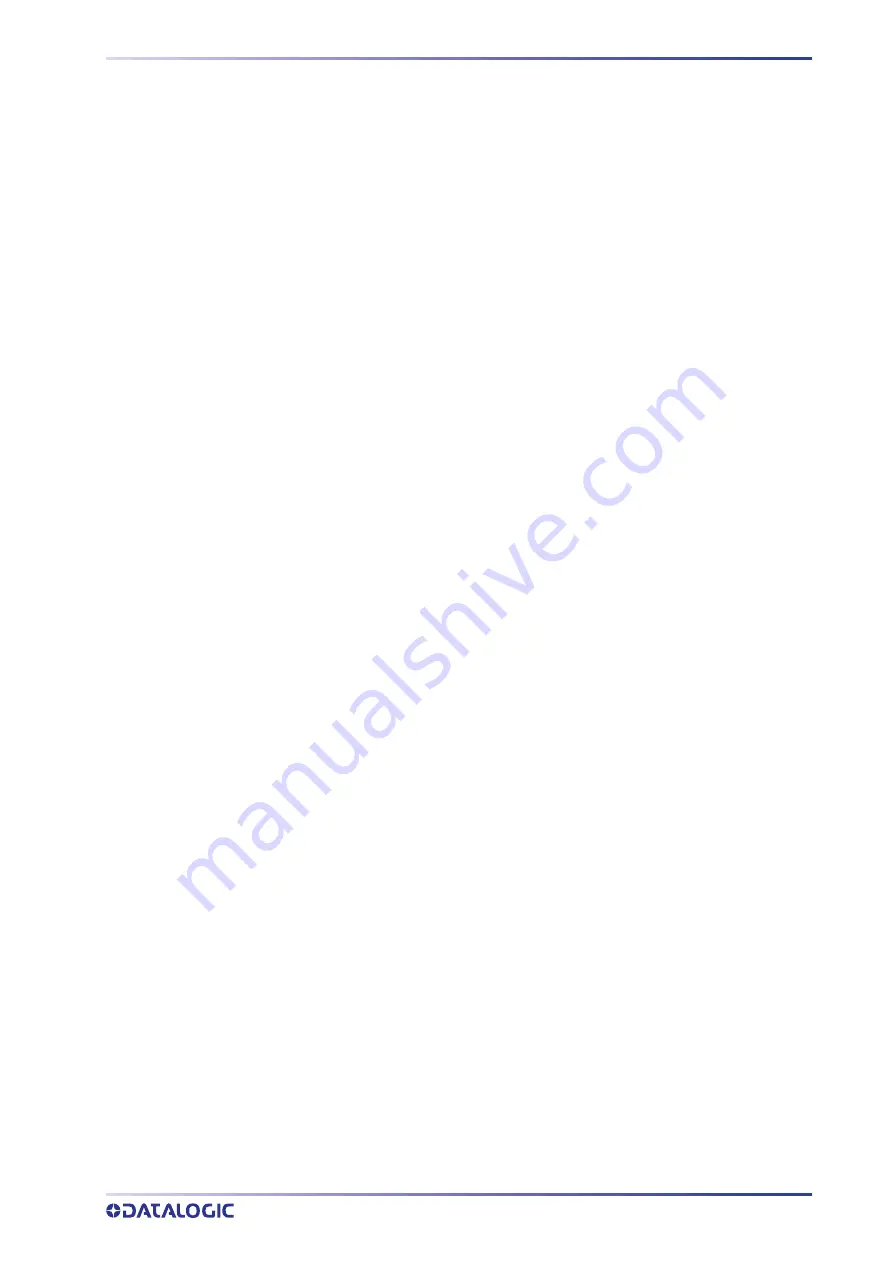
LINE TERMINATION
INSTRUCTION MANUAL
9
The maximum segment length for electrical data transmission with copper cables
between two nodes (field devices or switches) is 100 m. The copper cables are designed
uniformly in AWG 22. The installation guide defines different cable
types, whose range has been optimally adapted to general requirements for industry.
Sufficient system reserves allow industry-compatible installation with no limitation on
transmission distance.
The PROFINET cables conform to the cable types used in industry:
• PROFINET Type A: Standard permanently routed cable, no movement after instal
-
lation
• PROFINET Type B: Standard flexible cable, occasional movement or vibration
• PROFINET Type C: Special applications: for example, highly-flexible, constant
movement (trailing cable or torsion)
For complete information please refer to IEC 61918, IEC 61784-5-13 and IEC 61076-2-
101.
To increase noise immunity only S/FTP or SF/FTP cables must be used (CAT-5).
The maximum cable length (100 meters) predefined by Ethernet 100Base-TX must be
compulsorily fulfilled.
Regarding wiring and EMC measures, the IEC 61918 and IEC 61784-5-13 must be consid
-
ered.
LINE TERMINATION
Profinet network needs no line termination because the line is terminated automati
-
cally. Every Slave is able to detect the presence of the downstream Slaves.
MAC ADDRESS AND IP ADDRESS
The unit can be identified in the network through the MAC address and the IP address.
MAC address has to be intended as a permanent and globally unique identifier assigned
to the unit for communication on the physical layer; while the IP address is the name of
the unit in a network using the Internet protocol. MAC address is 6-byte long and can
-
not be modified. It consists of two parts, numbers are expressed in hexadecimal nota
-
tion: the first three bytes are used to identify the manufacturer (OUI, namely
Organizationally Unique Identifier), while the last three bytes are the specific identifier
of the unit. The MAC address can be found on the label applied to the encoder. The IP
address (and the subnet mask) must be assigned by the user to each interface of the
unit to be connected in the network. For additional information on the MAC address
refer to "
. For additional information on the IP address refer to
Setting the device name and the IP address" on page 26
.
GROUND CONNECTION
To minimize noise connect properly the shield and/or the connector housing and/or the
frame to ground. Connect properly the cable shield to ground on user's side. Datalogic's
EC- pre-assembled cables are fitted with shield connection to the connector ring nut in
order to allow grounding through the body of the device. Datalogic's CN- connectors
have a plastic gland, thus grounding is not possible. If metal connectors are used, con
-
nect the cable shield properly as recommended by the manufacturer. Anyway make
sure that ground is not affected by noise. It is recommended to provide the ground con
-
nection as close as possible to the device. We suggest using the ground point provided
in the cap (see Figure 1, use 1 TCEI M3 x 6 cylindrical head screw with 2 tooth lock wash
-
ers).
Summary of Contents for AMT58 Series
Page 1: ......
Page 8: ......
Page 13: ...AMT58x CB CANopen 5 3 1 3 Fissaggio con flangia codice ST 58 FLNG ...
Page 52: ......
Page 55: ...Subject index ...
Page 62: ...AMT58x PB Profibus 5 3 1 3 Installation using a flange code ST 58 FLNG ...
Page 101: ......
Page 102: ......
Page 109: ......
Page 114: ...AMT58x EC EtherCAT 5 3 1 3 Installation using a flange code ST 58 FLNG ...
Page 166: ......
Page 167: ...AMT58 PN INSTRUCTION MANUAL Absolute Encoders ...
Page 180: ...LIST OF ABBREVIATIONS xiv AMT58 PN ...
Page 221: ...TO TECHNOLOGY OBJECTS INSTRUCTION MANUAL 41 Figure 28 TO encoder enabled ...
Page 231: ...INSTRUCTION MANUAL 51 ...
Page 265: ...NORMAL OPERATION DIAGRAM INSTRUCTION MANUAL 85 NORMAL OPERATION DIAGRAM ...
Page 266: ...ENCODER STATE MACHINE 86 AMT58 PN PRESET DIAGRAM ...
Page 267: ...PARKING SENSOR DIAGRAM INSTRUCTION MANUAL 87 PARKING SENSOR DIAGRAM ...
Page 269: ...ERROR DIAGRAM INSTRUCTION MANUAL 89 Acknowledgment of not acknowledgeable sensor error ...
Page 284: ......
Page 285: ......
Page 287: ......
Page 294: ......
Page 299: ...AMT58x CB CANopen 5 3 1 3 Installation using a flange code ST 58 FLNG ...
Page 335: ......
Page 345: ...AMT58x DN DeviceNET 5 3 1 3 Installation using a flange code ST 58 FLNG ...
Page 380: ...AMT58x DN DeviceNET 40 Default 21h ...
Page 384: ...AMT58x DN DeviceNET 44 Default 00h ...
Page 394: ......
Page 404: ...AMT58x PB Profibus 5 3 1 3 Installation using a flange code ST 58 FLNG ...