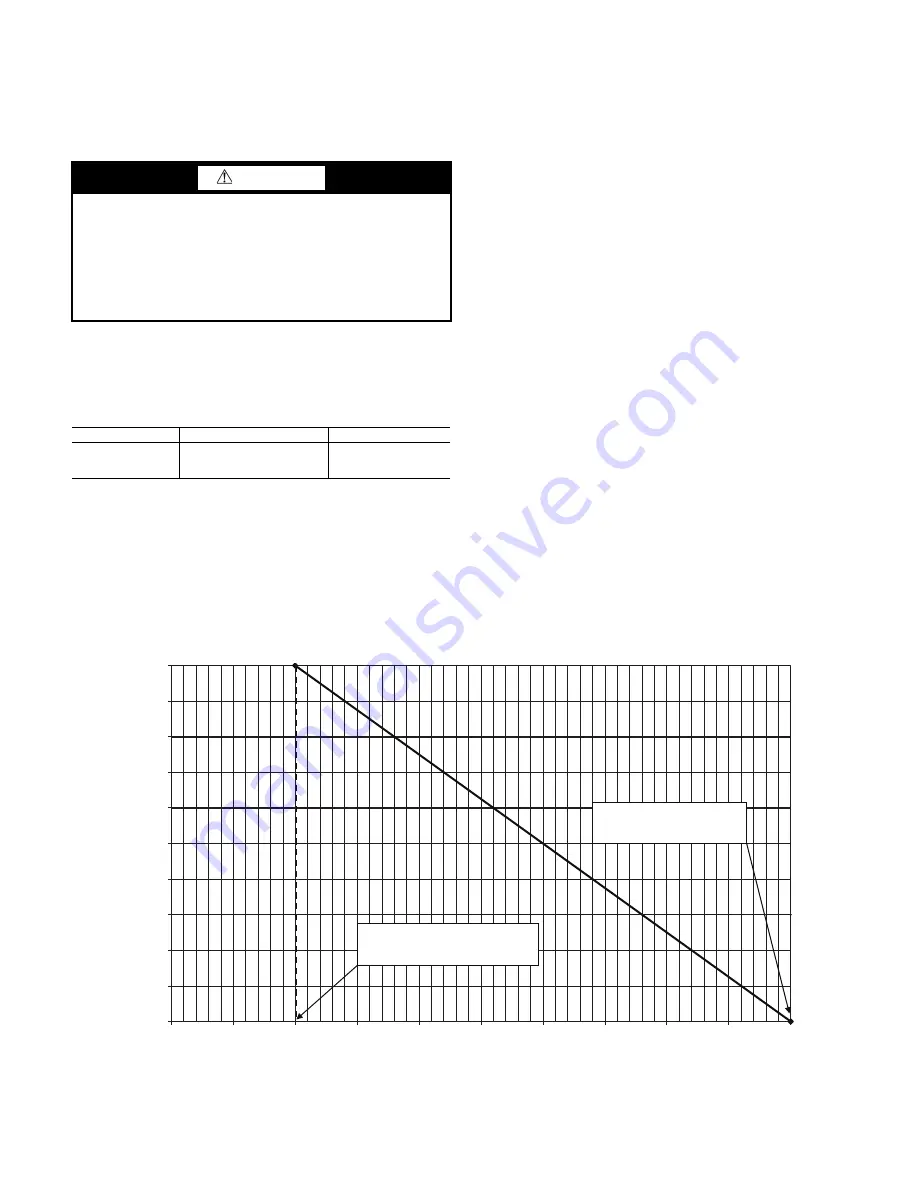
45
EXTERNALLY POWERED (4 TO 20 MA) DEMAND LIMIT
The energy management module is required for 4 to 20 mA
demand limit control. An externally powered 4 to 20 mA sig-
nal must be connected to TB6-1 and TB6-2. This signal is
read by a transducer type (0 to 5 vdc) on the EMM board via
a field-installed 0.5 W 250-ohm resistor.
To configure demand limit for 4 to 20 mA control based on unit
capacity, one parameter must be configured. The parameter is
Demand Limit Type Select. The value of the capacity limit will
vary linearly for 0% to 100% based on the input signal where 4
mA is 100% and 20 mA is 0% of total unit capacity.
To configure this option with the Carrier Controller display:
In the example in Fig. 43, a 4 mA signal is Demand Limit
100% and a 20 mA Demand Limit signal is 0%. The 4 to 20
mA signal is connected to TB6-1 and TB6-2. The demand limit
is a linear interpolation between the two values entered. If the
machine receives a 12 mA signal, the machine controls will
limit the capacity to 50%.
CCN LOADSHED CONTROLLED DEMAND LIMIT
To configure Demand Limit for CCN Loadshed control, the unit
Operating Type Control must be in CCN control. With the Carrier
Controller display, the machine must be started in Network Mode.
Network control can be executed from the GENUNIT table.
The unit must be controlled by a Chillervisor module. The
Chillervisor module can force the demand limit variable and
directly control the capacity of the machine. Additionally, the
unit’s set point will be artificially lowered to force the chiller to
load to the demand limit value.
Machine Start Delay
An option to delay the start of the machine is available. This
parameter is useful in keeping multiple machines from starting
at the same time in case of a power failure. The parameter has a
factory default of 1 minute. This parameter also has a role in
the timing for a chilled water flow switch alarm. To configure
this option with the Carrier Controller display, select
Main
Menu
Configuration Menu
General Configuration
and
select
Unit Off to On Delay
.
Fast Loading
The Fast Capacity Recovery function allows for an accelerated
unit start-up. This is especially useful following brief power out-
ages at data centers where rapid restart can keep data center op-
erating. This should not be used on normal comfort cooling ap-
plications. To activate the Fast Capacity Recovery, go to
Main
Menu
Configuration Menu
Service Parameters
and set
Fast Capacity Recovery
. The available options are as follows:
• Disabled (normal loading sequence): Follows the set delays
for unit and circuit start up
• Quick start Load - (Quick Start Loading): With Flow es-
tablished, ignores Capacity Control Override #53 (ON-
OFF-ON Delay)
• Fast Capacity Recov (Fast Capacity Recovery): With Flow
established, ignores Capacity Control Override #53 (ON-
OFF-ON Delay), and allows both compressors to start at
the same time (with a 10-second delay between starts)
NOTE: Unit cannot operate with Ramp Loading enabled if
Fast Capacity Recovery is set to Quick start Load or Fast Ca-
pacity Recov.
Fig. 43 — Example: 4 to 20 mA Demand Limit
CAUTION
Care should be taken when interfacing with other control sys-
tems due to possible power supply differences such as a full
wave bridge versus a half wave rectification. Connection of
control devices with different power supplies may result in
permanent damage. Carrier Controller controls incorporate
power supplies with half wave rectification. A signal isola-
tion device should be utilized if the signal generator incorpo-
rates a full wave bridge rectifier.
DISPLAY NAME
PATH
VALUE
Demand Limit
Type Select
Main Menu
Configuration Menu
General Configuration
Default = 0 (None)
4 to 20mA Control = 2
0
10
20
3
0
40
50
60
70
8
0
90
100
12 14 16 1
8
20
mA Demand Limit
S
i
g
nal
% Demand Limit
0
2
4 6
8
10
mA for Dem
a
nd Limit = 100
%
(lim_mx)
mA for Dem
a
nd Limit = 0
%
(lim_ze)
a30-5883
Summary of Contents for AquaForce 30XV140
Page 79: ...79 Fig 76 VFD Communication Wiring Compressor A B Fan VFD A1 A2 B1 B2...
Page 228: ...228 Fig 90 30XV Typical Field Wiring Schematic cont...
Page 229: ...229 Fig 91 30XV Standard Tier 140 275 All Voltages Power Schematic NOTE See Legend on page 226...
Page 230: ...230 Fig 92 30XV Standard Tier 300 325 All Voltages Power Schematic NOTE See Legend on page 226...
Page 240: ...240 Fig 99 30XV Communication Wiring...
Page 241: ...241 Fig 100 30XV 115V Control Wiring All Tonnages All Voltages...
Page 242: ...242 Fig 101 30XV 24V Control Wiring 30XV140 325 All Voltages...
Page 243: ...243 Fig 101 30XV 24V Control Wiring 30XV140 325 All Voltages cont...
Page 244: ...244 Fig 102 30XV 24V Control Wiring 30XV350 500 All Voltages...
Page 245: ...245 Fig 102 30XV 24V Control Wiring 30XV350 500 All Voltages cont...
Page 246: ...246 Fig 103 Component Arrangement Diagram for 30XV140 325...
Page 247: ...247 Fig 103 Component Arrangement Diagram for 30XV140 325 cont...
Page 248: ...248 Fig 104 Component Arrangement Diagram for 30XV350 500...
Page 337: ...337 APPENDIX J FACTORY SUPPLIED PUMPS cont Fig L System Information...
Page 338: ...338 APPENDIX J FACTORY SUPPLIED PUMPS cont Fig M Unit and Language Settings...
Page 341: ...341 APPENDIX J FACTORY SUPPLIED PUMPS cont Fig P Data Input 2...
Page 342: ...342 APPENDIX J FACTORY SUPPLIED PUMPS cont Fig Q Data Input 3...
Page 347: ...347 APPENDIX J FACTORY SUPPLIED PUMPS cont Fig U Pump Wiring Diagram...