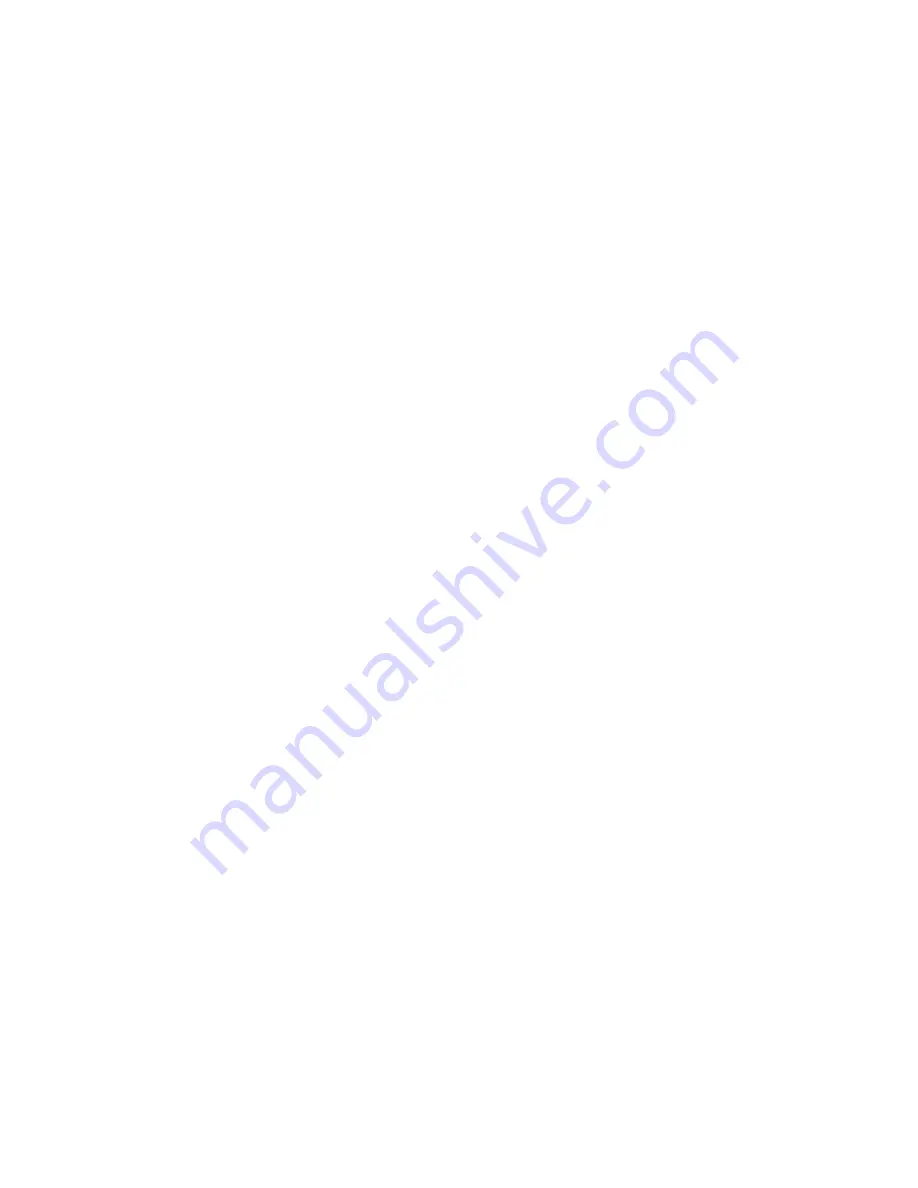
349
APPENDIX J — FACTORY-SUPPLIED PUMPS (cont)
If the adapter was removed from the motor, replace it. Assure
the stationary seat is carefully guided over the stub shaft when
assembling the adapter back onto the motor.
Lubricate the inside of the rotating seal, seal head (9), with a
small amount of silicon or glycerin lubricant and slide onto the
stub shaft (10) with a twisting motion, carbon face first, until
the carbon face is pressed firmly against the stationary seat (8).
Firmly press on the rotating seal, seal head, metal parts with a
screw driver all the way around the seal with a screwdriver to
ensure the faces are mated properly. Remove the spring retain-
er from the seal spring and place the spring seal over the rotat-
ing seal.
REPLACE PUMP IMPELLER
Install the impeller key on the shaft and place the seal spring
retainer onto the impeller hub register. Slide the impeller in the
place on the stub shaft.
Ensure the seal spring is kept in place on the seal rotating as-
sembly and fits well into the retainer on the impeller hub.
TIGHTEN IMPELLER CAP SCREW
Install the impeller cap screw and washer (6 and 7). Hold the
impeller the same way as when the cap screw was loosened
and tighten the cap screw.
INSTALL NEW ADAPTER O-RING
Insert new adapter o-ring into the o-ring groove of the adapter
and apply silicon or glycerin lubricant around the o-ring.
CLAMP RING
Insert the clamp ring through the impeller and adapter flange.
Tighten the nut on the clamp ring to 90 to 100 in-lbs.
LOWER ROTATING ASSEMBLY INTO PLACE
The rotating assembly motor, adapter, and impeller combina-
tion may now be lowered into the casing.
CASING AND ADAPTER CLAMP-RING
The casing and adapter clamp-ring is now installed and tight-
ened. Reconnect the flush line flex hose.
ISOLATION VALVES
Replace the casing drain plug and open the suction and dis-
charge isolation valves.
MOTOR WIRING
The motor conduit and its wiring are now replaced. If the mo-
tor is new, double check the voltage and rpm are identical to
the original motor.
Be sure to check rotation of the motor after rewiring.
Ensure the pump is filled with water before operating to check
rotation.
Pump Software
The pump control board contains the operating software for the
pump and the calibration parameters that support sensorless
operation. The calibration parameters are unique to the pump
volute. If the motor is replaced, the calibration parameters must
be entered into the new pump motor. These can be transferred
from the old motor if the control system is still functional or
can be obtained from Armstrong using the pump volute part
number and serial number. The follow process covers upgrad-
ing software and moving the calibration file (sensorless map)
and the configuration file from one motor to another.
Software change must be done with a computer connected to
the pump. This can be done wireless or with an Ethernet cable.
See operation section above for details on wireless connec-
tions. Ethernet cable connection is in the back of the pump dis-
play. Front cover of the motor must be removed to access this.
For all imports/updates, the progress is shown by a red bar at
the top of the pump display. Wait for the bar to scroll complete-
ly across the top of the pump display prior to the next step.
RETRIEVE SENSORLESS MAP
Go to Pump under the Settings screen. Click the Export Sen-
sorless Map (*.map) link. The export feature works best with
Google Chrome. Save the downloadable file. On the new pump
motor or after software upgrade, chose Import Sensorless Map
(*.map) on the same screen to add the map to the controller.
RETRIEVE CONFIGURATION
Go to General under Settings screen. Click Export Configura-
tion. Save the downloadable file. On the new pump motor or
after software upgrade, chose Import Configuration on the
same screen to add the configuration file to the controller.
UPDATE PUMP SOFTWARE
Make sure the Sensorless Map and Configuration files are
saved on your computer prior to updating the software. Go to
Administrative under Settings. Locate the Upload Packages
block. Use the Choose file icon to search for the file, uC_up-
grade_#.##.pkg. Click upload. A red bar will scroll across the
top of the pump display showing progress.
Next, upload the following files with the same process:
• fonts_upgrade.pkg
• lcd_upgrade.pkg
• web_upgrade.pkg
Verify the software is uploaded by clicking the information
button, i, on the pump display. Click System then Version. Ver-
ify the Web Package status shows Installed.
Summary of Contents for AquaForce 30XV140
Page 79: ...79 Fig 76 VFD Communication Wiring Compressor A B Fan VFD A1 A2 B1 B2...
Page 228: ...228 Fig 90 30XV Typical Field Wiring Schematic cont...
Page 229: ...229 Fig 91 30XV Standard Tier 140 275 All Voltages Power Schematic NOTE See Legend on page 226...
Page 230: ...230 Fig 92 30XV Standard Tier 300 325 All Voltages Power Schematic NOTE See Legend on page 226...
Page 240: ...240 Fig 99 30XV Communication Wiring...
Page 241: ...241 Fig 100 30XV 115V Control Wiring All Tonnages All Voltages...
Page 242: ...242 Fig 101 30XV 24V Control Wiring 30XV140 325 All Voltages...
Page 243: ...243 Fig 101 30XV 24V Control Wiring 30XV140 325 All Voltages cont...
Page 244: ...244 Fig 102 30XV 24V Control Wiring 30XV350 500 All Voltages...
Page 245: ...245 Fig 102 30XV 24V Control Wiring 30XV350 500 All Voltages cont...
Page 246: ...246 Fig 103 Component Arrangement Diagram for 30XV140 325...
Page 247: ...247 Fig 103 Component Arrangement Diagram for 30XV140 325 cont...
Page 248: ...248 Fig 104 Component Arrangement Diagram for 30XV350 500...
Page 337: ...337 APPENDIX J FACTORY SUPPLIED PUMPS cont Fig L System Information...
Page 338: ...338 APPENDIX J FACTORY SUPPLIED PUMPS cont Fig M Unit and Language Settings...
Page 341: ...341 APPENDIX J FACTORY SUPPLIED PUMPS cont Fig P Data Input 2...
Page 342: ...342 APPENDIX J FACTORY SUPPLIED PUMPS cont Fig Q Data Input 3...
Page 347: ...347 APPENDIX J FACTORY SUPPLIED PUMPS cont Fig U Pump Wiring Diagram...