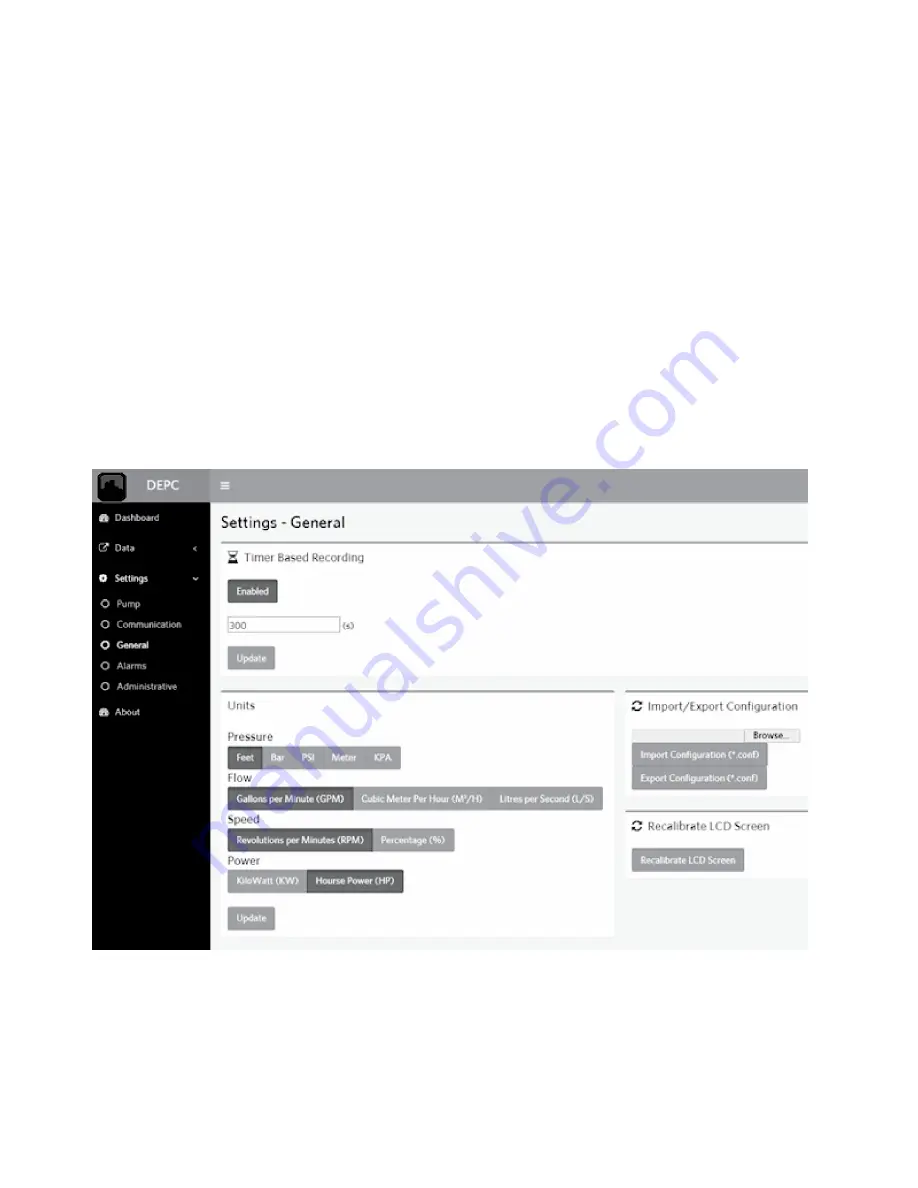
344
APPENDIX J — FACTORY-SUPPLIED PUMPS (cont)
Control Mode: Set to “Parallel”.
Operational Mode: Set to “Quad Pressure Min Flow”.
Id: This is a number, 1-4 depending on number of pumps, to
identify each pump. It will be different for each pump. The
pump identified as 1 will be the master. Make this the furthest
left pump looking at the displays.
BEP: This is the “Best Efficiency Point” for a single pump. It is
set from the factory and does not need to be adjusted.
Maximum Operating Pump Count: Enter the number of pumps
in the chiller.
Total Design Flow and Total Minimum Flow: Values are calcu-
lated from the design flows below and the Maximum Operat-
ing Pump Count. This is what the chiller will see.
Operational Limits: Set as “Standard”.
Design Flow: Enter the system design flow divided by the
number of pumps.
Design Head: Enter the system design head for the pump. Use
the total head including the building and chiller.
Zero Flow Head: Enter 40% of the design head.
Min Flow: Enter the min flow divided by the number of
pumps. Assure the Total Minimum Flow shown above is high-
er than the chiller specified minimum. If value is not available,
enter chiller nominal size times 1.5, divided by the number of
pumps.
Once selections are made, touch the “Update” button at the
bottom left of this section.
If wireless connection cannot be made, the following procedure
can be used on a temporary basis to get the pumps running.
1. Using the manual mode on the pump, set the pumps to run at
design flow. If this value is not available, use the nominal
flow of the chiller, 2.4 * tons. The flow is per pump so set
each pump to the design flow divided by the number of
pumps used to meet the load. For the N+0 option, use the
number of pumps. For the N+1 option, use the number of
pumps minus one.
2. Record the head pressure at the design flow from the display.
3. Using the manual mode on the pump, set the pumps to run at
minimum flow. Assure this is above the rated minimum flow
of the chiller.
4. Record the head pressure at the minimum flow from the
display.
5. Set these values at the pump display. Go to Pump Configura-
tion/Pump Control/Parallel/Quadratic. Enter the design flow.
Enter the design head pressure and minimum head pressure
recorded from the steps above.
Fig. S — General Settings
Summary of Contents for AquaForce 30XV140
Page 79: ...79 Fig 76 VFD Communication Wiring Compressor A B Fan VFD A1 A2 B1 B2...
Page 228: ...228 Fig 90 30XV Typical Field Wiring Schematic cont...
Page 229: ...229 Fig 91 30XV Standard Tier 140 275 All Voltages Power Schematic NOTE See Legend on page 226...
Page 230: ...230 Fig 92 30XV Standard Tier 300 325 All Voltages Power Schematic NOTE See Legend on page 226...
Page 240: ...240 Fig 99 30XV Communication Wiring...
Page 241: ...241 Fig 100 30XV 115V Control Wiring All Tonnages All Voltages...
Page 242: ...242 Fig 101 30XV 24V Control Wiring 30XV140 325 All Voltages...
Page 243: ...243 Fig 101 30XV 24V Control Wiring 30XV140 325 All Voltages cont...
Page 244: ...244 Fig 102 30XV 24V Control Wiring 30XV350 500 All Voltages...
Page 245: ...245 Fig 102 30XV 24V Control Wiring 30XV350 500 All Voltages cont...
Page 246: ...246 Fig 103 Component Arrangement Diagram for 30XV140 325...
Page 247: ...247 Fig 103 Component Arrangement Diagram for 30XV140 325 cont...
Page 248: ...248 Fig 104 Component Arrangement Diagram for 30XV350 500...
Page 337: ...337 APPENDIX J FACTORY SUPPLIED PUMPS cont Fig L System Information...
Page 338: ...338 APPENDIX J FACTORY SUPPLIED PUMPS cont Fig M Unit and Language Settings...
Page 341: ...341 APPENDIX J FACTORY SUPPLIED PUMPS cont Fig P Data Input 2...
Page 342: ...342 APPENDIX J FACTORY SUPPLIED PUMPS cont Fig Q Data Input 3...
Page 347: ...347 APPENDIX J FACTORY SUPPLIED PUMPS cont Fig U Pump Wiring Diagram...