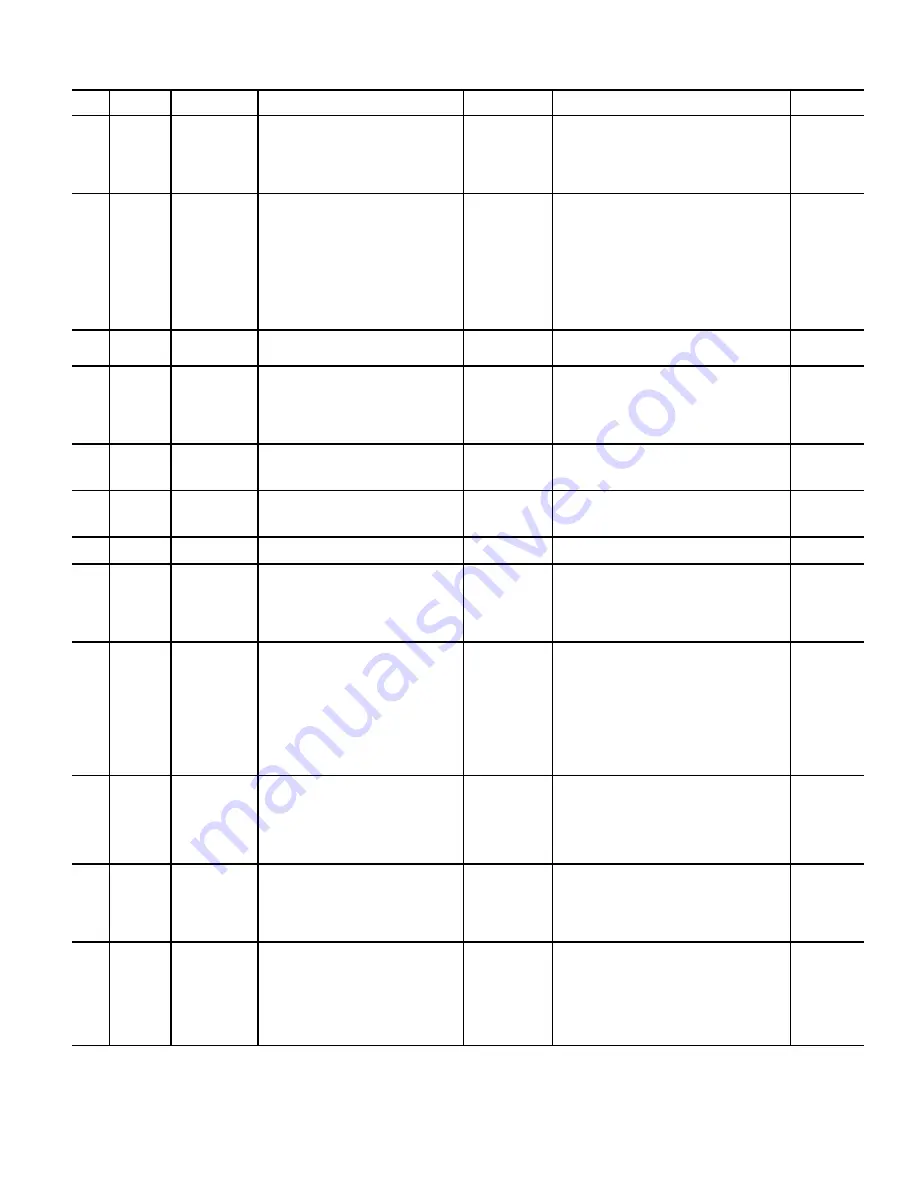
221
Table 171 — Alarms List
CODE WARNING/
ALARM
DESCRIPTION
POSSIBLE CAUSES
DOES MACHINE
SHUT DOWN
ACTION TO
BE TAKEN
REFERENCE
PARAMETER
001
Warning
10 Volts Low
The control card voltage is <10 V from
terminal 50. Remove some of the load from
terminal 50, as the 10 V supply is
overloaded. Maximum 15 mA or minimum
590
Ω
. A short circuit in a connected
potentiometer or incorrect wiring of the
potentiometer can cause this condition.
Remove the wiring from terminal 50. If the warning
clears, the problem is with the wiring. If the
warning does not clear, replace the control card.
002
NOTE 1
Live Zero Error
This warning or alarm only appears if
programmed in parameter 6-01 Live Zero
Timeout Function. The signal on 1 of the
analog inputs is less than 50% of the
minimum value programmed for that input.
Broken wiring or a faulty device sending
the signal can cause this condition.
•
Check the connections on all the analog mains
terminals.
- Control card terminals 53 and 54 for sig-
nals, terminal 55 common. - MCB 101 ter-
minals 11 and 12 for signals, terminal 10
common.
- MCB 109 terminals 1, 3, and 5 for signals,
terminals 2, 4, and 6 common.
•
Check that the frequency converter program-
ming and switch settings match the analog
signal type.
•
Perform an input terminal signal test.
6-01 Live Zero
Timeout
003
Warning
No Motor
Motor wiring disconnected. Reference
Parameter must be programmed to (2) or
(6)
Inspect motor wiring connections at VFD and at
motor
1-80 Function
at Stop
004
NOTE 1
Mains Phase
Loss
A phase is missing on the supply side, or
the mains voltage imbalance is too high.
This message also appears for a fault in
the input rectifier on the frequency
converter. Options are programmed in
parameter 14-12 Function at Mains
Imbalance.
Check the supply voltage and supply currents to
the frequency converter
14-12
Function at
Mains
Imbalance
005
Warning
DC Link Voltage
High
The DC-link voltage (DC) is higher than the
high-voltage warning limit. The limit
depends on the frequency converter
voltage rating. The unit is still active.
Check the supply voltage and supply currents to
the frequency converter
006
Warning
DC Link Voltage
Low
The DC-link voltage (DC) is lower than the
low-voltage warning limit. The limit
depends on the frequency converter
voltage rating. The unit is still active.
Check the supply voltage and supply currents to
the frequency converter
007
NOTE 1
DC Overvoltage
If the DC-link voltage exceeds the limit, the
frequency converter trips after a time.
•
Extend
the
ramp
time.
•
Change the ramp type.
008
NOTE 1
DC Undervoltage
If the DC-link voltage drops below the
undervoltage limit, the frequency converter
checks if a 24 V DC back-up supply is
connected. If no 24 V DC back-up supply is
connected, the frequency converter trips
after a fixed time delay. The time delay
varies with unit size.
•
Check that the supply voltage matches the fre-
quency converter voltage.
•
Perform an input voltage test.
•
Perform a soft charge circuit test.
009
NOTE 1
Inverter
Overloaded
The frequency converter has run with more
than 100% overload for too long and is
about to cut-out. The counter for electronic
thermal inverter protection issues a
warning at 98% and trips at 100%, while
giving an alarm. The frequency converter
cannot be reset until the counter is below
90%.
•
Compare the output current shown on the
LCP with the frequency converter rated cur-
rent.
•
Compare the output current shown on the
LCP with the measured motor current.
•
Display the thermal frequency converter load
on the LCP and monitor the value. When run-
ning above the frequency converter continu-
ous current rating, the counter increases.
When running below the frequency converter
continuous current rating, the counter de-
creases.
010
NOTE 1
Motor ETR
Overtemperature
According to the electronic thermal
protection (ETR), the motor is too hot.
Select whether the frequency converter
issues a warning or an alarm when the
counter reaches 100% in parameter 1-90
Motor Thermal Protection. The fault occurs
when the motor runs with more than 100%
overload for too long.
•
Check
for
motor
overheating.
•
Check if the motor is mechanically overload-
ed.
•
Check that the motor current set in 1-24 Motor
Current is correct.
•
Ensure that the motor data in parameters 1–
20 to 1–25 are set correctly.
1-90 Motor
Thermal
Protection
(this
parameter
should be set
to [0])
011
NOTE 1
Motor Thermistor
Overtemperature
Check whether the thermistor is
disconnected. Select whether the
frequency converter issues a warning or an
alarm in parameter 1-90 Motor Thermal
Protection
•
Check
for
motor
overheating.
•
Check if the motor is mechanically overload-
ed.
1-90 Motor
Thermal
Protection
(this
parameter
should be set
to [0])
012
NOTE 1
Torque Limit
The torque has exceeded the value in
parameter 4-16 Torque Limit Motor Mode
or the value in parameter 4-17 Torque Limit
Generator Mode. Parameter 14-25 Trip
Delay at Torque Limit can change this
warning from a warning-only condition to a
warning followed by an alarm.
•
If the motor torque limit is exceeded during
ramp-up, extend the ramp-up time.
•
If the generator torque limit is exceeded during
ramp-down, extend the ramp-down time.
•
If torque limit occurs while running, increase
the torque limit. Make sure that the system
can operate safely at a higher torque.
•
Check the application for excessive current
draw on the motor
Summary of Contents for AquaForce 30XV140
Page 79: ...79 Fig 76 VFD Communication Wiring Compressor A B Fan VFD A1 A2 B1 B2...
Page 228: ...228 Fig 90 30XV Typical Field Wiring Schematic cont...
Page 229: ...229 Fig 91 30XV Standard Tier 140 275 All Voltages Power Schematic NOTE See Legend on page 226...
Page 230: ...230 Fig 92 30XV Standard Tier 300 325 All Voltages Power Schematic NOTE See Legend on page 226...
Page 240: ...240 Fig 99 30XV Communication Wiring...
Page 241: ...241 Fig 100 30XV 115V Control Wiring All Tonnages All Voltages...
Page 242: ...242 Fig 101 30XV 24V Control Wiring 30XV140 325 All Voltages...
Page 243: ...243 Fig 101 30XV 24V Control Wiring 30XV140 325 All Voltages cont...
Page 244: ...244 Fig 102 30XV 24V Control Wiring 30XV350 500 All Voltages...
Page 245: ...245 Fig 102 30XV 24V Control Wiring 30XV350 500 All Voltages cont...
Page 246: ...246 Fig 103 Component Arrangement Diagram for 30XV140 325...
Page 247: ...247 Fig 103 Component Arrangement Diagram for 30XV140 325 cont...
Page 248: ...248 Fig 104 Component Arrangement Diagram for 30XV350 500...
Page 337: ...337 APPENDIX J FACTORY SUPPLIED PUMPS cont Fig L System Information...
Page 338: ...338 APPENDIX J FACTORY SUPPLIED PUMPS cont Fig M Unit and Language Settings...
Page 341: ...341 APPENDIX J FACTORY SUPPLIED PUMPS cont Fig P Data Input 2...
Page 342: ...342 APPENDIX J FACTORY SUPPLIED PUMPS cont Fig Q Data Input 3...
Page 347: ...347 APPENDIX J FACTORY SUPPLIED PUMPS cont Fig U Pump Wiring Diagram...