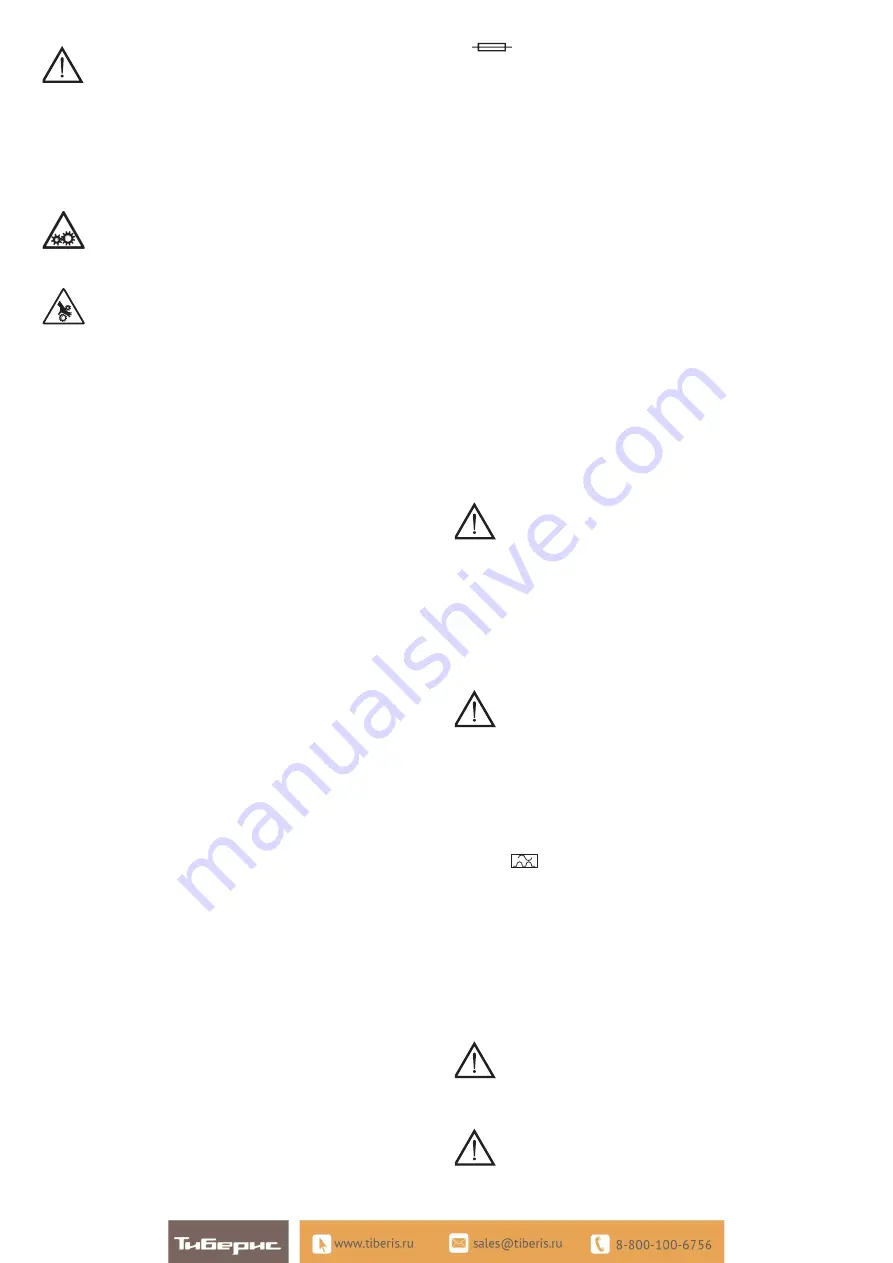
RESIDUAL RISKS
29(57851,1*SRVLWLRQWKHZHOGLQJPDFKLQHRQDKRUL]RQWDOVXUIDFHWKDWLV
DEOHWRVXSSRUWWKHZHLJKWRWKHUZLVHHJLQFOLQHGRUXQHYHQÀRRUVHWFWKHUH
LVGDQJHURIRYHUWXUQLQJ
,03523(5 86( LW LV KD]DUGRXV WR XVH WKH ZHOGLQJ PDFKLQH IRU DQ\ ZRUN
RWKHUWKDQWKDWIRUZKLFKLWZDVGHVLJQHGHJGHLFLQJPDLQVZDWHUSLSHV
029,1* 7+( :(/',1* 0$&+,1( $OZD\V VHFXUH WKH JDV ERWWOH WDNLQJ
VXLWDEOHSUHFDXWLRQVVRWKDWLWFDQQRWIDOODFFLGHQWDOO\LIXVHG
'RQRWXVHWKHKDQGOHWRKDQJWKHZHOGLQJPDFKLQH
7KH VDIHW\ JXDUGV DQG PRYLQJ SDUWV RI WKH FRYHULQJ RI WKH ZHOGLQJ PDFKLQH
DQGRIWKHZLUHIHHGHUVKRXOGEHLQWKHLUSURSHUSRVLWLRQVEHIRUHFRQQHFWLQJWKH
ZHOGLQJPDFKLQHWRWKHSRZHUVXSSO\
:$51,1*$Q\PDQXDORSHUDWLRQFDUULHGRXWRQWKHPRYLQJSDUWVRIWKHZLUH
IHHGHUIRUH[DPSOH
5HSODFLQJUROOHUVDQGRUWKHZLUHJXLGH
,QVHUWLQJZLUHLQWKHUROOHUV
/RDGLQJWKHZLUHUHHO
&OHDQLQJWKHUROOHUVWKHJHDUVDQGWKHDUHDXQGHUQHDWKWKHP
/XEULFDWLQJWKHJHDUV
6+28/' %( &$55,(' 287 :,7+ 7+( :(/',1* 0$&+,1( 6:,7&+(' 2))
$1'',6&211(&7(')5207+(32:(56833/<287/(7
,1752'8&7,21$1'*(1(5$/'(6&5,37,21
7KLVZHOGLQJPDFKLQHLVDVRXUFHRIFXUUHQWIRUDUFZHOGLQJPDGHVSHFL¿FDOO\IRU0$*
welding carbon steel or weak alloys with CO
2
protective gas or Argon/CO
2
mixes,
using full or core electrode wires.
It is also ideal for MIG welding stainless steel with Argon gas cont 1-2%
oxygen, aluminium and CuSi
3
, CuAl
8
(brazing) with Argon gas, using electrode wires
that are suitable for the workpiece to be welded.
Suitable core wires can also be used without Flux protection gas, adapting the polarity
of the torch to what is indicated by the wire producer.
SYNERGIC operation guarantees fast and easy welding parameter setting, always
guaranteeing high arc control and welding quality (One Touch Technology).
It is particularly suitable for light metalwork fabrication and in body shops, for welding
galvanized plates, high stress stainless steel and aluminium.
0$,1&+$5$&7(5,67,&6
- Synergic (automatic) or manual operation;
- 17 pre-set synergic curves;
- Wire speed, welding voltage and welding current shown on an LCD screen;
- 2T, 4T and spot operation selection;
- Adjustments: wire up slope, electronic reactance, wire burn-back time, post gas;
- Polarity change for GAS MIG-MAG/BRAZING welding or NO GAS/FLUX;
- Thermostatic safeguard;
- Protection against accidental short-circuits caused by contact between torch and
earth;
- Protection against irregular voltage (power supply voltage too high or too low);
67$1'$5'$&&(6625,(6
- torch;
- return cable complete with earth clamp.
237,21$/$&&(6625,(6
- Argon bottle adapter;
- Trolley;
- Self darkening helmet;
- MIG MAG welding kit.
7(&+1,&$/'$7$
'$7$3/$7(
The most important data regarding use and performance of the welding machine are
summarised on the rating plate and have the following meaning:
)LJ$
EUROPEAN standard of reference, for safety and construction of arc welding
machines.
Symbol for internal structure of the welding machine.
Symbol for welding procedure provided.
Symbol
S
: indicates that welding operations may be carried out in environments
with heightened risk of electric shock (e.g. very close to large metallic volumes).
Symbol for power supply line:
1~ : single phase alternating voltage;
3~ : 3-phase alternating voltage.
Protection rating of the covering.
7HFKQLFDOVSHFL¿FDWLRQVIRUSRZHUVXSSO\OLQH
-
U
: Alternating voltage and power supply frequency of welding machine (allowed
limit ±10%).
-
I
PD[
: Maximum current absorbed by the line.
-
I
HII
: effective current supplied.
Performance of the welding circuit:
-
U
: maximum no-load voltage (open welding circuit).
-
I
/U
: current and corresponding normalised voltage that the welding machine
can supply during welding.
-
X
: Duty cycle: indicates the time for which the welding machine can supply the
corresponding current (same column). It is expressed as %, based on a 10 min.
cycle (e.g. 60% = 6 minutes working, 4 minutes pause, and so on)
If the usage factors (on the plate, referring to a 40°C environment) are exceeded,
the thermal safeguard will trigger (the welding machine will remain in standby
until its temperature returns within the allowed limits).
-
A/V-A/V
: shows the range of adjustment for the welding current (minimum
maximum) at the corresponding arc voltage.
0DQXIDFWXUHU¶VVHULDOQXPEHUIRUZHOGLQJPDFKLQHLGHQWL¿FDWLRQLQGLVSHQVDEOHIRU
technical assistance, requesting spare parts, discovering product origin).
: Size of delayed action fuses to be used to protect the power line.
Symbols referring to safety regulations, whose meaning is given in chapter 1
“General safety considerations for arc welding”.
Note: The data plate shown above is an example to give the meaning of the symbols
and numbers; the exact values of technical data for the welding machine in your
possession must be checked directly on the data plate of the welding machine itself.
27+(57(&+1,&$/'$7$
:(/',1*0$&+,1(VHHWDEOH7$%
725&+VHHWDEOH7$%
7KHZHOGLQJPDFKLQHZHLJKWLVVKRZQLQWDEOH7$%
'(6&5,37,212)7+(:(/',1*0$&+,1(
&21752/'(9,&(6$'-8670(17$1'&211(&7,21
:(/',1*0$&+,1()LJ%
$WWKHIURQW
1- Control panel (see description).
2- Cable and welding torch.
3- Cable and earth clamp.
$WWKHEDFN
4- Main ON/OFF switch.
5- Shielding gas hose connector.
6- Power supply cable.
,QWKHUHHOVSDFH
7- Positive terminal (+).
8- Negative terminal (-).
1%3RODULW\LQYHUVLRQIRU)/8;ZHOGLQJQRJDV
:(/',1*0$&+,1(&21752/3$1(/)LJ&
1- Adjustment of the welding power (synergic operation) or of the wire feed speed
(manual operation). Press the knob to select either SYNERGIC or MANUAL
operation.
2- Adjustment of the arc length (synergic operation) or of the welding voltage (manual
operation). Press the knob to access the various welding machine settings menu;
3- LCD display.
,167$//$7,21
:$51,1* $// ,167$//$7,21 23(5$7,216 $1' (/(&75,&$/
&211(&7,216 0867 $/:$<6 %( &$55,(' 287 :,7+ 7+( :(/',1*
0$&+,1(6:,7&+('2))$1'',6&211(&7(')5207+(32:(56833/<
7+((/(&75,&&211(&7,216086721/<%(&$55,('287%<(;3(5725
48$/,),('7(&+1,&,$16
Return cable-clamp assembly
)LJ'
326,7,21,1*7+(:(/',1*0$&+,1(
Choose the place where the welding machine is to be installed so that there are no
obstructions to the cooling air inlets and outlets; at the same time make sure that
conductive dust, corrosive vapours, humidity etc. cannot be drawn into the machine.
Leave at least 250 mm of free space all around the welding machine.
:$51,1* 3RVLWLRQ WKH ZHOGLQJ PDFKLQH RQ D OHYHO VXUIDFH ZLWK
VXI¿FLHQW ORDGEHDULQJ FDSDFLW\ VR WKDW LW FDQQRW EH WLSSHG RYHU RU VKLIW
GDQJHURXVO\
&211(&7,21727+(0$,132:(56833/<
- Before making any electrical connection, check the rating plate data on the welding
machine to make sure they correspond to the voltage and frequency of the available
power supply where the machine is to be installed.
- The welding machine must be connected only and exclusively to a power supply with
the neutral conductor connected to earth.
- To guarantee protection against indirect contact use the following types of residual
current devices:
- A type (
) for single-phase machines.
- In order to satisfy the requirements of the EN 61000-3-11 (Flicker) standard we
recommend connecting the welding machine to the interface points of the main
power supply that have an impedance of less than Zmax = 0.25 ohm.
- The IEC/EN 61000-3-12 Standard does not apply to the welding machine.
If the welding machine is connected to an electrical grid, the installer or user must
make sure that the machine can indeed be connected (if necessary, consult the
company that manages the electrical grid).
3OXJDQGRXWOHW
&RQQHFWWKHSRZHUVXSSO\SOXJWRDPDLQVVRFNHW¿WWHGZLWKIXVHVRUDQDXWRPDWLF
circuit-breaker; the corresponding earth terminal should be connected to the (yellow-
green) earth conductor of the power supply. Table 1 (TAB. 1) shows the recommended
delayed fuse sizes, in amps, for the main supply, which have been chosen according
to the maximum rated current output from the welding machine, and to the nominal
power supply voltage.
:$51,1* 1RQFRPSOLDQFH ZLWK WKH DERYH UHJXODWLRQV UHQGHUV WKH
PDQXIDFWXUHU¶VVDIHW\V\VWHPFODVV,LQHI¿FLHQWZLWKUHVXOWLQJVHULRXVULVNVWR
SHRSOHHJHOHFWULFVKRFNDQGWKLQJVHJ¿UH
:(/',1*&,5&8,7&211(&7,216
:$51,1*
%()25(
&$55<,1*
287
7+(
)2//2:,1*
&211(&7,2160$.(685(7+$77+(:(/',1*0$&+,1(,66:,7&+('2))
$1'',6&211(&7(')5207+(32:(56833/<
Table 1
7$%
shows the recommended sizes of the welding cables (in mm
2
),
according to the maximum current output from the welding machine.