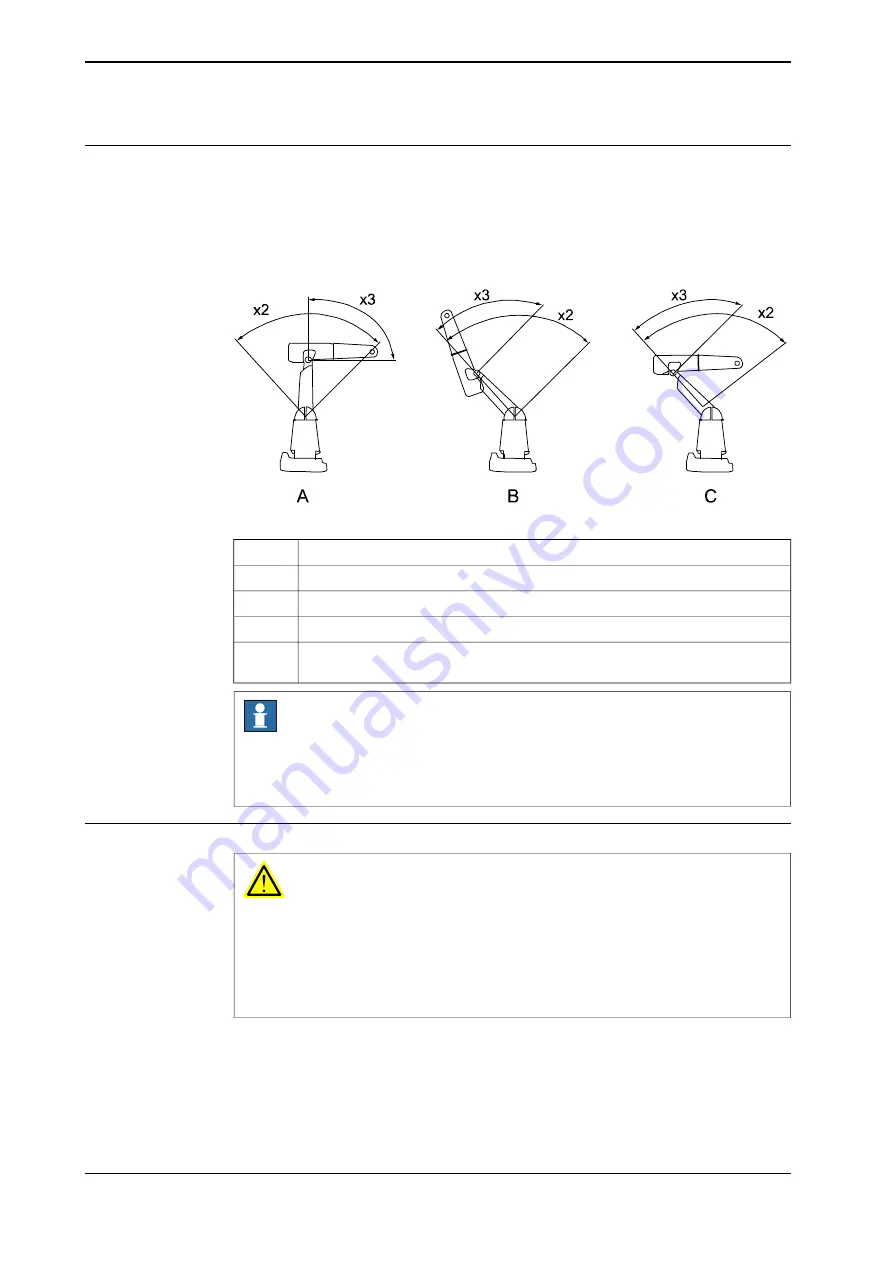
Examples
This example shows a robot with defined axis ranges for axes 2 and 3 in three
different positions. The function Axis Position Supervision supervises that axis 2
is within range x2 and that axis 3 is within range x3.
In positions A and B, all supervised axes are within the allowed ranges. In position
C, axis 3 is not within the defined range.
xx0600003331
Allowed axis position range for axis 2.
x2
Allowed axis position range for axis 3.
x3
Robot position A. Both axis 2 and axis 3 are within the allowed ranges.
A
Robot position B. Both axis 2 and axis 3 are within the allowed ranges.
B
Robot position C. Axis 2 is within the allowed range but axis 3 is not within its
allowed range. This will trigger a violation.
C
Note
The ranges define axis angles, not the position of the TCP. In robot position C,
the TCP is still within what seems to be a safe range, but axis 3 is outside its
defined range.
Limitations
WARNING
Be aware of that the braking starts when the axis exceeds the configured limit
value.
The braking distance depends on robot type, load, position and speed, and
therefore an additional stopping distance may sometimes be required to achieve
the desired safety.
52
Application manual - Functional safety and SafeMove2
3HAC052610-001 Revision: P
© Copyright 2016-2020 ABB. All rights reserved.
2 SafeMove functions
2.5.4 Axis Position Supervision (APO)
Continued
Summary of Contents for SafeMove2
Page 1: ...ROBOTICS Application manual Functional safety and SafeMove2 ...
Page 8: ...This page is intentionally left blank ...
Page 16: ...This page is intentionally left blank ...
Page 34: ...This page is intentionally left blank ...
Page 56: ...This page is intentionally left blank ...
Page 72: ...This page is intentionally left blank ...
Page 112: ...This page is intentionally left blank ...
Page 194: ...This page is intentionally left blank ...
Page 196: ...This page is intentionally left blank ...
Page 234: ...This page is intentionally left blank ...
Page 237: ......