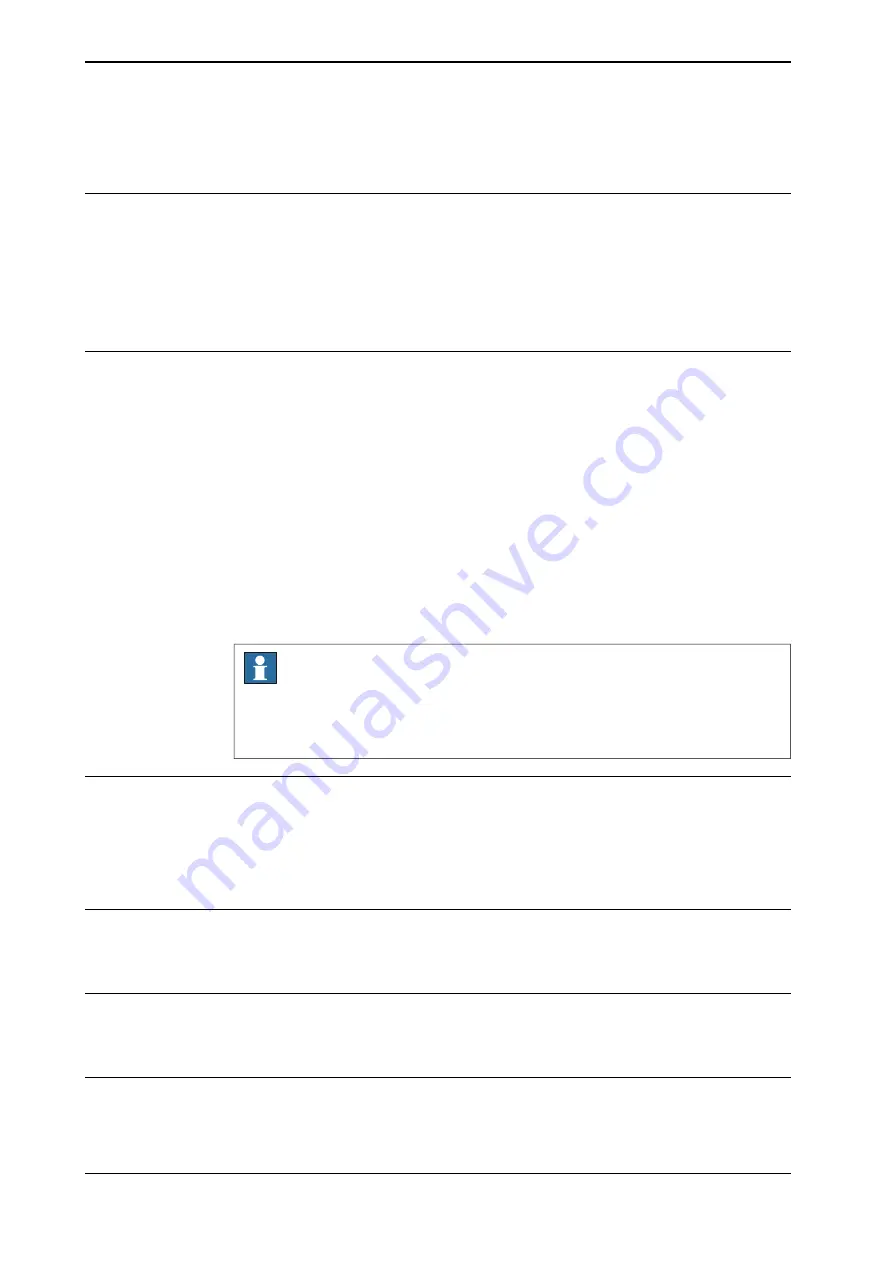
2.3.2 Hardware synchronization
Hardware synchronization
Hardware synchronization is a function that makes sure that the robot calibration
is correct by using a physical synchronization switch.
Unsynchronized state can, for example, occur:
•
If one or more axes were moving during shutdown or power off.
•
After a failed synchronization.
Functionality
The robot must move to a safe synchronization position to ensure that the safety
controller and the robot controller are synchronized. The safe synchronization
position is defined during configuration and stored in the safety controller.
The robot must move to the safe synchronization position and activate a switch.
When the switch is activated, the safety controller assumes that the robot revolution
counters are correct. It also calculates the arm position from the motor positions,
the gear ratio, and its internal revolution counter. If the position matches the stored
synchronization position within half a motor revolution, then the synchronization
is assumed to be correct.
If the synchronization is correct, the safety controller then sends a message to the
robot controller, confirming that the safety controller is synchronized to its
mechanical units, and continues with its regular operation.
Note
The supervision functions can only be active while SafeMove is synchronized.
When unsynchronized, only manual mode operation with reduced speed is
possible until synchronization is executed successfully.
Settings
The following settings need to be configured for hardware synchronization:
•
Synchronization signal.
•
Angles and positions of robot (and additional axes) at the synchronization
position.
Dependencies to other supervision functions
Software synchronization is always available even if hardware synchronization is
configured.
Limitations
•
The safe sync position must be within reach for the robot. It must not be a
singularity, that is all six axis must have unique positions.
Related information
Configure the synchronization position on page 148
Continues on next page
42
Application manual - Functional safety and SafeMove2
3HAC052610-001 Revision: P
© Copyright 2016-2020 ABB. All rights reserved.
2 SafeMove functions
2.3.2 Hardware synchronization
Summary of Contents for SafeMove2
Page 1: ...ROBOTICS Application manual Functional safety and SafeMove2 ...
Page 8: ...This page is intentionally left blank ...
Page 16: ...This page is intentionally left blank ...
Page 34: ...This page is intentionally left blank ...
Page 56: ...This page is intentionally left blank ...
Page 72: ...This page is intentionally left blank ...
Page 112: ...This page is intentionally left blank ...
Page 194: ...This page is intentionally left blank ...
Page 196: ...This page is intentionally left blank ...
Page 234: ...This page is intentionally left blank ...
Page 237: ......