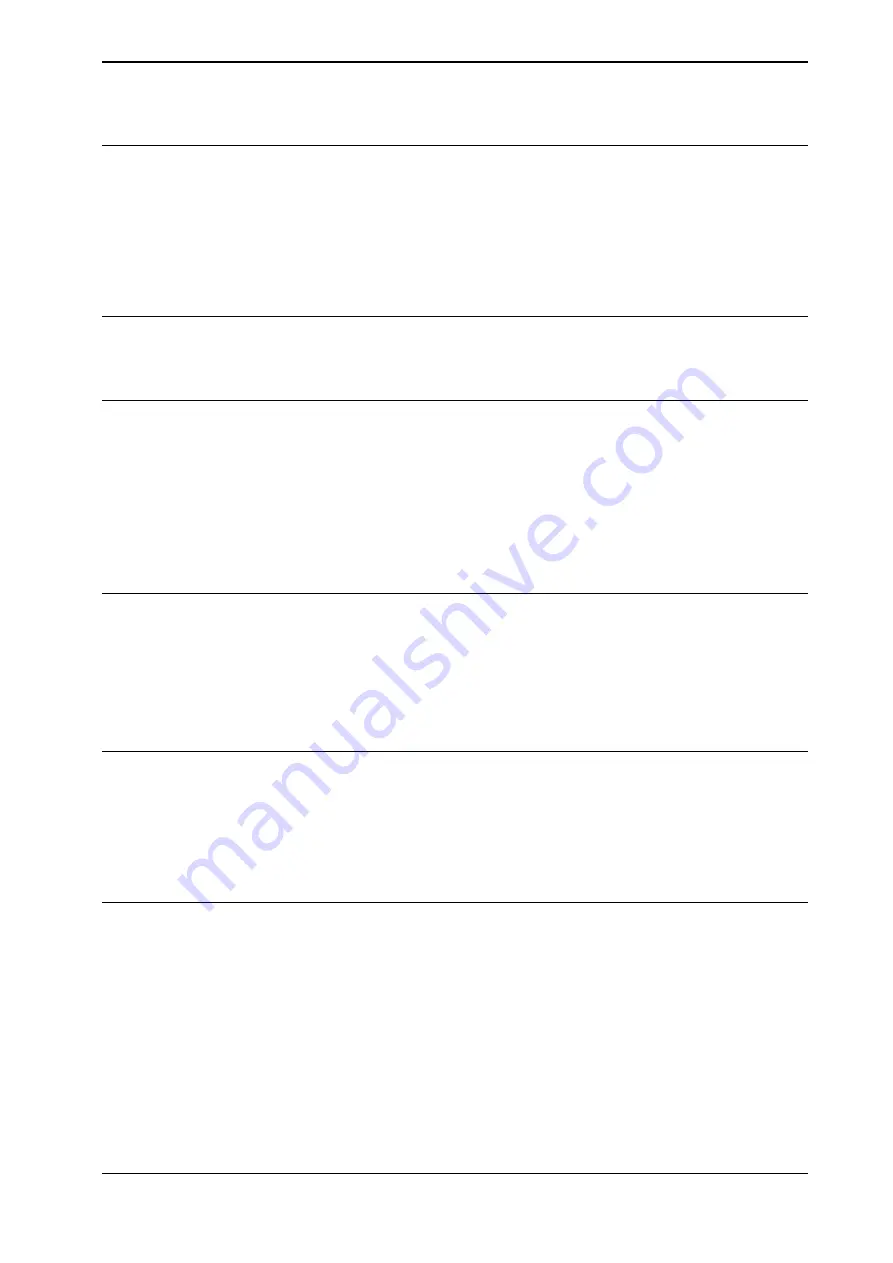
Supported positioners
SafeMove supports positioners that are single axis mechanical units. Positioners
with several axes are treated as multiple single axes, for example two axes
positioners will be treated by SafeMove as two single axes and can be monitored
as such using axis supervision.
Positioners that are used with activation/deactivation feature, is not supported.
The axes of the positioner must be active at all times.
Servo welding gun
SafeMove does not support supervision of servo welding guns. That is, the robot
axes can be supervised, but not the axis of the servo welding gun.
Non ABB additional axes
Non ABB track motion units, non ABB positioners, and other additional axis may
be supported by the SafeMove option but this needs to be verified case by case.
To verify if a non ABB additional axis can be used with SafeMove, tune the additional
axis before configuring the SafeMove parameters. If a properly tuned and configured
non ABB additional axis still generates error messages regarding servo lag, then
it cannot be used with SafeMove. For more information about tuning an additional
axis see
Application manual - Additional axes and stand alone controller
.
Work area for additional axes
There are always the following upper and lower work area limitations for additional
axes:
•
Track unit length (arm side) max ± 448 m
•
Rotating axis (arm side) max ± 25700 degrees or ± 448 radians
On the motor side there is also a limitation of ± 32000 revolutions.
Combined external axes and robot with gantry
SafeMove does not support supervision of combined external axes, such as a
gantry, or supervision of robots moved by the gantry.
It is possible to supervise robots moved by a gantry using the Basic joint supervision
mode. In Basic joint supervision mode, only SafeMove functions working on axes
are available.
Basic joint supervision mode
In Basic joint supervision mode, SafeMove supports supervision of some robots
and external axes that are not normally allowed. Examples are robots mounted on
a gantry, or other non-track external axes.
In Basic joint supervision mode, no safe zones or tool supervision functions are
allowed. In addition, there are changes to some internal SafeMove supervision
functions:
•
The manual mode speed supervision of the TCP, wrist center point, and
elbow are disabled. Instead, axis speed limits are set to approximate a
Cartesian speed limit. The user is responsible for validating that this speed
limit satisfies the requirements for safe manual mode operation.
Continues on next page
Application manual - Functional safety and SafeMove2
29
3HAC052610-001 Revision: P
© Copyright 2016-2020 ABB. All rights reserved.
1 Introduction
1.3 Limitations
Continued
Summary of Contents for SafeMove2
Page 1: ...ROBOTICS Application manual Functional safety and SafeMove2 ...
Page 8: ...This page is intentionally left blank ...
Page 16: ...This page is intentionally left blank ...
Page 34: ...This page is intentionally left blank ...
Page 56: ...This page is intentionally left blank ...
Page 72: ...This page is intentionally left blank ...
Page 112: ...This page is intentionally left blank ...
Page 194: ...This page is intentionally left blank ...
Page 196: ...This page is intentionally left blank ...
Page 234: ...This page is intentionally left blank ...
Page 237: ......