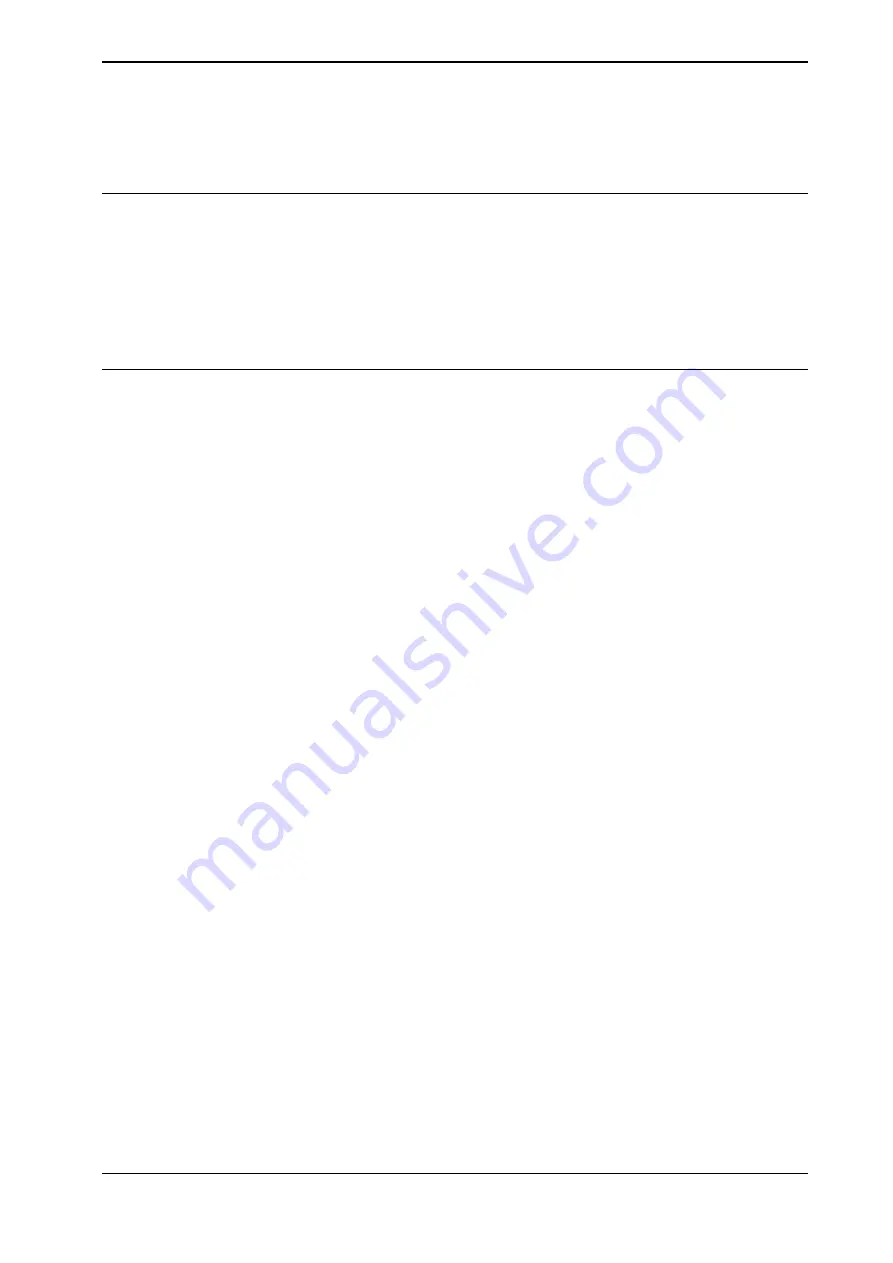
1.2.4 Safe design of SafeMove
Overview
SafeMove has two important types of supervision functionality.
The first one being to ensure that the axis computer and the drive system are
working correctly, making the robot follow the ordered value from the main computer
as expected.
The second being to supervise the robot position and speed and stopping the robot
or setting output signals to indicate a hazard.
Supervision of axis computer and drive system
The main computer calculates the absolute motor position values sent as reference
to the axis computer, and simultaneously sends them to the safety controller. The
axis computer reports the actual rotational motor position values via the main
computer to the safety controller, as a separate process from the reference value.
Since these values are within one revolution, the absolute position is calculated
by adding values from internal revolution counters in both the axis computer and
in SafeMove.
By comparing the ordered motor position and the actual motor position, SafeMove
can detect any difference (outside a permitted lag deviation) between the two
positions, thereby ensuring that the drive system is working properly according to
the first supervision function as described above.
It is important to ensure that the safety controller and the robot controller are
synchronized. The safe sync position is defined during configuration and stored
in the safety controller. In this position, SafeMove will calculate the robot joint
positions and check against a stored value to confirm that the synchronization is
correct, covering the following points:
•
SafeMove is working correctly with the right revolution counter value.
•
The right manipulator is used.
•
The calibration value is correct.
•
The SMB is working correctly.
Category 3 supervision
The supervision complies with category 3, that is, two separate channels shall
always give the same result. One channel consists of the axis computer with the
drive system, motors, resolvers, and measurement system. The second channel
consists of the ordered value from the main computer. These channels are
compared using the SafeMove evaluation circuits, which in itself is dual channel.
Additional safety design
Additional safety, over and above what is formally required, is brought to the
concept by the inherent dual channel character of the resolver, thanks to its dual
sine and cosine output, where the square sum is supervised to be close to 1.
Continues on next page
Application manual - Functional safety and SafeMove2
23
3HAC052610-001 Revision: P
© Copyright 2016-2020 ABB. All rights reserved.
1 Introduction
1.2.4 Safe design of SafeMove
Summary of Contents for SafeMove2
Page 1: ...ROBOTICS Application manual Functional safety and SafeMove2 ...
Page 8: ...This page is intentionally left blank ...
Page 16: ...This page is intentionally left blank ...
Page 34: ...This page is intentionally left blank ...
Page 56: ...This page is intentionally left blank ...
Page 72: ...This page is intentionally left blank ...
Page 112: ...This page is intentionally left blank ...
Page 194: ...This page is intentionally left blank ...
Page 196: ...This page is intentionally left blank ...
Page 234: ...This page is intentionally left blank ...
Page 237: ......