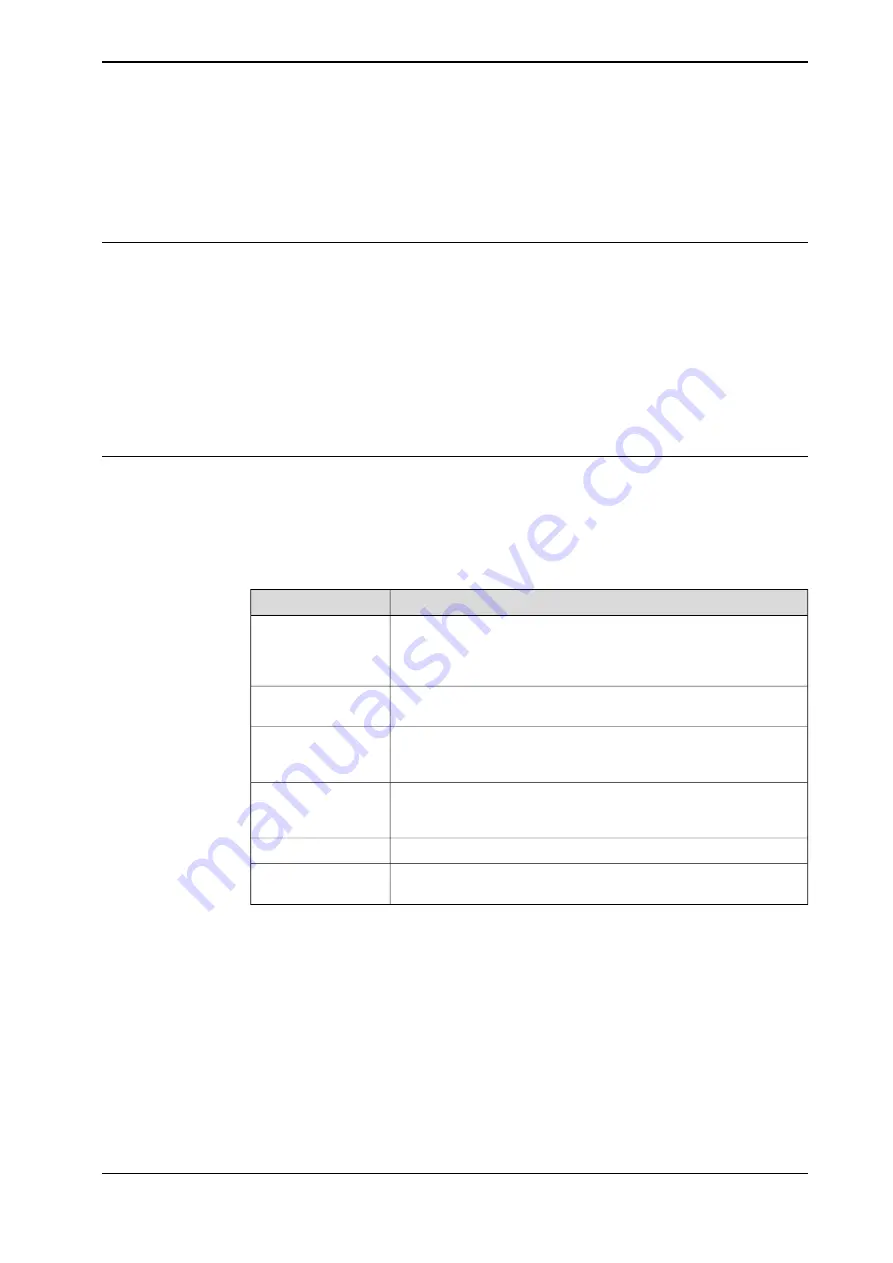
1 Introduction
1.1 Overview of functional safety
Purpose
The purpose of the safety module and the functional safety options is to provide
a robust and easy-to-use safety controller in the robot system. Functional safety
includes a complete software and hardware solution that is fully integrated with
the robot controller and the RobotStudio programming environment.
SafeMove is the main functional safety option, but the safety module can also be
used in various applications without the SafeMove option. For example to
communicate with a safety PLC through safe fieldbus communication, or when
using the keyless mode selector.
SafeMove functions
When using SafeMove, the safety controller ensures a high safety level in the robot
system by using supervision functions that can stop the robot. Note that the safety
module and the functional safety options is one component in the safety system
of a complete robot cell, normally complemented by other equipment (for example
light barriers) for detecting the whereabouts of the operator.
Description
Function
Protects the operator and enhances machine and equipment safety
by supervising the position (
Tool Position Supervision
), speed (
Tool
Speed Supervision
) and orientation (
Tool Orientation Supervision
)
of the tool.
Tool supervision
functions
Protects the surroundings by supervising the axis position (
Axis
Position Supervision
) and the axis speed (
Axis Speed Supervision
).
Axis supervision
functions
Supervises the stand-still of robot axes without having to switch the
robot to Motors Off. It enables operators to perform tasks in the
immediate vicinity of the robot.
Stand Still Supervi-
sion
Allows the robot to be in contact with the work-piece in limited areas.
This can for example be used in applications where the robot is
used for grinding or during tool change.
Contact application
tolerance
Supervises that the brakes are checked with a cyclic interval.
Cyclic brake check
Triggers stop of the robot using safe fieldbus inputs from the safety
PLC.
Stop functions
Some examples of applications:
•
Manual loading stations
•
Manual workpiece inspection during operation
•
Optimization of cell size
•
Protection of sensitive equipment
•
Ensuring safe orientation of emitting processes
Continues on next page
Application manual - Functional safety and SafeMove2
17
3HAC052610-001 Revision: P
© Copyright 2016-2020 ABB. All rights reserved.
1 Introduction
1.1 Overview of functional safety
Summary of Contents for SafeMove2
Page 1: ...ROBOTICS Application manual Functional safety and SafeMove2 ...
Page 8: ...This page is intentionally left blank ...
Page 16: ...This page is intentionally left blank ...
Page 34: ...This page is intentionally left blank ...
Page 56: ...This page is intentionally left blank ...
Page 72: ...This page is intentionally left blank ...
Page 112: ...This page is intentionally left blank ...
Page 194: ...This page is intentionally left blank ...
Page 196: ...This page is intentionally left blank ...
Page 234: ...This page is intentionally left blank ...
Page 237: ......